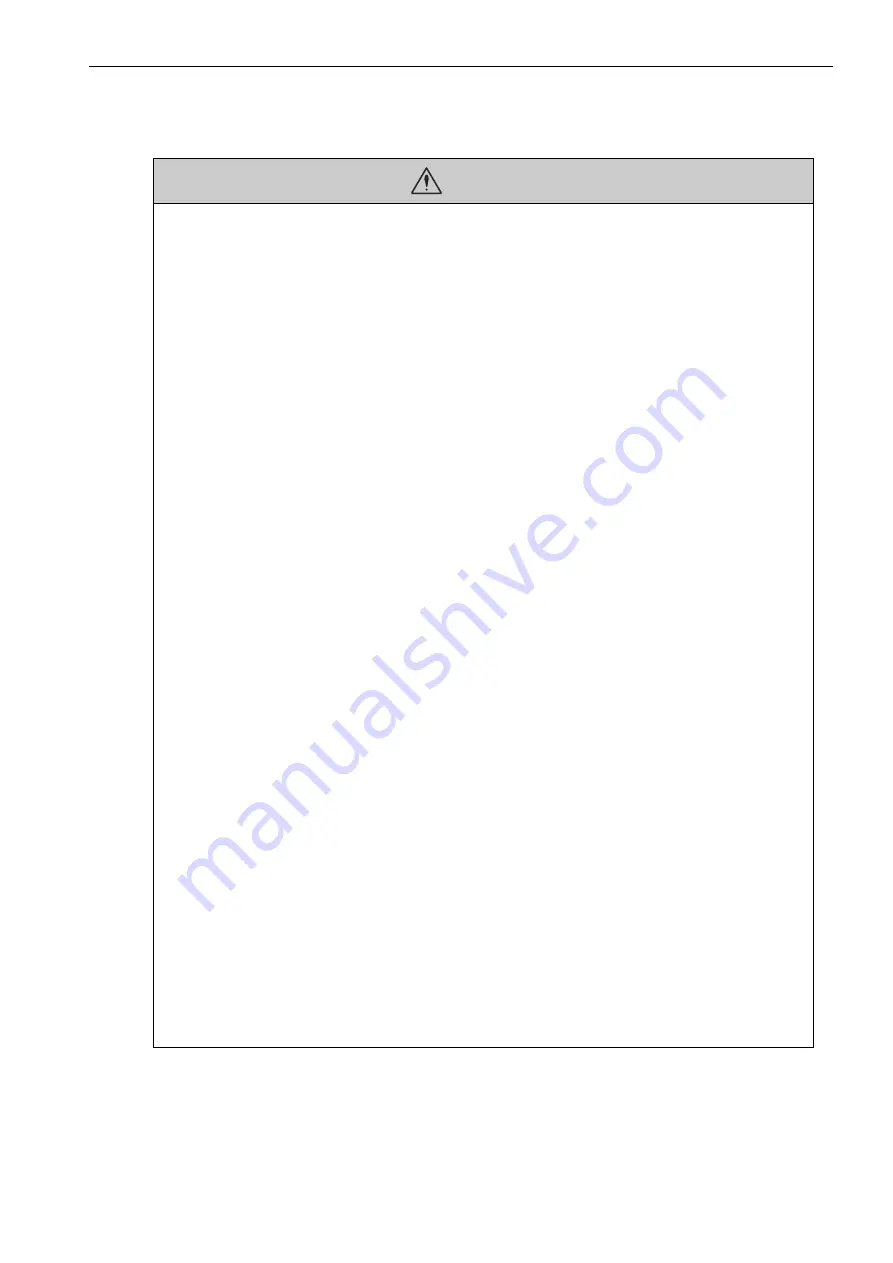
ix
Wiring
CAUTION
• Check the wiring to confirm that it has been performed correctly.
There is a risk of motor runaway, injury, or malfunction.
• Do not bundle the main circuit and the I/O signal cables/encoder cables together or run them
through the same duct. Keep the main circuit cable and I/O signal cables at least 30 cm away from
each other.
Malfunction may result if these cables are too close to each other.
• The maximum wiring length is 3 m for I/O signal cables, 20 m for motor main circuit cables or
encoder cables, and 10 m for control power supply cables (+24 V, 0 V).
• Provide sufficient shielding when using the products in the following locations.
• Locations that are subject to noise, such as from static electricity
• Locations that are subject to strong electromagnetic or magnetic fields
• Locations that are subject to radiation
• Locations that are near power lines
There is a risk of equipment damage.
• Wiring and inspections must be performed by qualified engineers only.
• Do not connect a commercial power supply to the U, V, or W motor connection terminals.
There is a risk of injury or fire.
• Firmly connect the power supply terminals and motor connection terminals.
There is a risk of fire.
• Do not touch terminals before the main-circuit capacitor has had time to discharge after the power
supply has been turned OFF. A high voltage may still remain in the power regeneration converter
and SERVOPACK.
First make sure that the CHARGE indicator is not lit and that the DC bus voltage (between P and N) is correct
by using a tester or other device before performing wiring or starting inspections.
• Observe the following precautions when wiring the main circuit terminal block.
• Do not turn ON the power supply to the servo drive until all wiring, including the main circuit terminals,
has been completed.
• If the main circuit terminals have a connector, remove the connector from the SERVOPACK before you
perform wiring.
• Only insert one wire into each wire insertion slot on the terminal block or connector.
• When inserting wires, be sure not to short-circuit the exposed portion of the core wire on adjacent wires.
• Always use the specified power supply voltage.
There is a risk of fire or malfunction of the power regeneration converter or SERVOPACK.
• Make sure that the polarity is correct (P (+), N (-)).
Incorrect polarity may cause rupture or damage.
• In places with poor power supply conditions, take all steps necessary to ensure that the input power
is supplied within the specified voltage range.
There is a risk of equipment damage.
• Install breakers and other safety measures to provide protection against shorts in external wiring.
There is a risk of fire.
• Use a 24-VDC control power supply with double insulation or reinforced insulation. Make sure that
the output holding time is 100 ms or longer.
• Use shielded twisted-pair cables or shielded multicore twisted-pair cables for I/O signal and
encoder cables.
• When connecting the battery, connect the polarity correctly.
There is a risk of damaging the battery, power regeneration converter, SERVOPACK, or servomotor and a
risk of explosion.
• Mount a battery into the power regeneration converter.
It is dangerous to install batteries on the encoder cable, because there is a risk of creating a loop circuit
between the batteries.