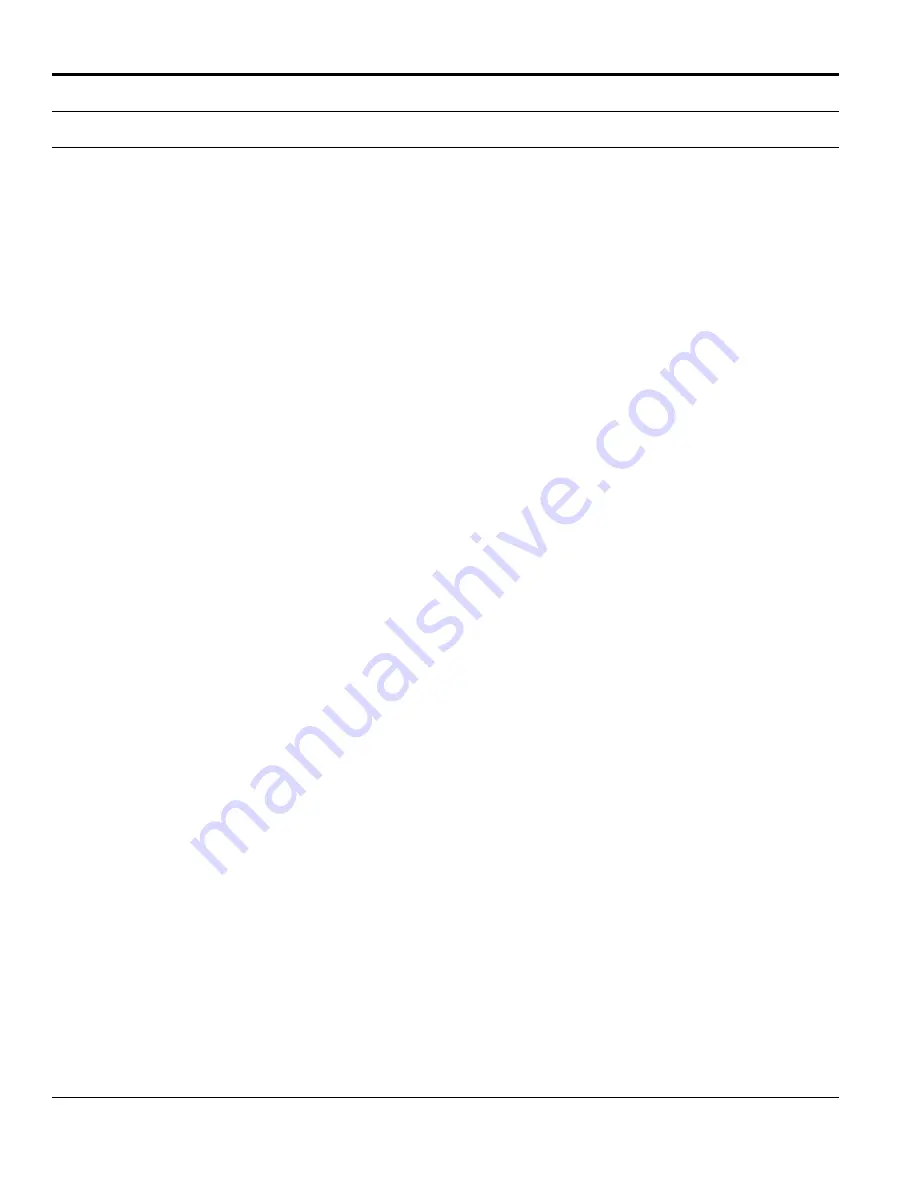
Appendix D - Micro SD Backup & Restore MM147 - D4 Hot Melt Unit
152
Error Codes
Code 1:
SD card failed to initialize
•
It is likely there is not a card installed, it is damaged, or it is not formatted as FAT32
Code 2:
SD failed to mount
Code 3:
SD card failed to unmount
Code 4:
CPU failed to open the backup file
Code 5:
CPU failed to close the backup file
Code 6:
CPU failed to write information to the backup file during backup creation
Code 7:
CPU failed to read information from the backup file during restore
Code 8:
Backup file is invalid
•
Upon creation, a checksum is calculated and saved at the beginning of the file. A file should only be
invalid if it was edited outside of the CPU
Summary of Contents for D4
Page 1: ...D4 Hot Melt Unit Manual Number MM147 Revision Date 6 2018 ...
Page 4: ......
Page 10: ...Table of Contents MM147 D4 Hot Melt Unit 10 Module Status LED 170 Link Activity LED 170 ...
Page 20: ...Section 2 Safety and Use MM147 D4 Hot Melt Unit 20 ...
Page 22: ...Section 3 Basic Features MM147 D4 Hot Melt Unit 22 ...
Page 35: ...MM147 D4 Hot Melt Unit Section 5 Setup 35 Section 5 Setup Control Panel ...
Page 42: ...Section 5 Setup MM147 D4 Hot Melt Unit 42 Set Language Continued Next Page ...
Page 43: ...MM147 D4 Hot Melt Unit Section 5 Setup 43 Set Language Continued ...
Page 44: ...Section 5 Setup MM147 D4 Hot Melt Unit 44 Set Temperature Units ...
Page 47: ...MM147 D4 Hot Melt Unit Section 5 Setup 47 Hose Valve Temperature Continued ...
Page 54: ...Section 5 Setup MM147 D4 Hot Melt Unit 54 Beacon Alarm Setup Continued ...
Page 55: ...MM147 D4 Hot Melt Unit Section 5 Setup 55 Beacon 2 ...
Page 70: ...Section 5 Setup MM147 D4 Hot Melt Unit 70 Sequential Start Valve ...
Page 100: ...Section 6 Operation MM147 D4 Hot Melt Unit 100 ...
Page 106: ...Section 7 Maintenance MM147 D4 Hot Melt Unit 106 ...
Page 110: ...Section 9 Specifications MM147 D4 Hot Melt Unit 110 Dimensions ...
Page 112: ...Section 10 Part Number List MM147 D4 Hot Melt Unit 112 D4 Unit ...
Page 113: ...MM147 D4 Hot Melt Unit Section 10 Part Number List 113 D4 Unit Continued ...
Page 120: ...Section 10 Part Number List MM147 D4 Hot Melt Unit 120 D4 Base Unit 776xx392 ...
Page 142: ...Section 11 Warranty MM147 D4 Hot Melt Unit 142 ...
Page 144: ...Section 12 Service MM147 D4 Hot Melt Unit 144 ...
Page 146: ...Appendix A Password Levels MM147 D4 Hot Melt Unit 146 Setting Level 0 as Default Continued ...
Page 148: ...Appendix B Power Requirements MM147 D4 Hot Melt Unit 148 ...
Page 150: ...Appendix C Instruction Sheets for Option Kits MM147 D4 Hot Melt Unit 150 ...
Page 208: ...5 Valco Melton IS0343 Anybus Installation Installation Continued ...
Page 245: ...Appendix E Communication Protocols Modus MM147 D4 Hot Melt Unit 162 ...