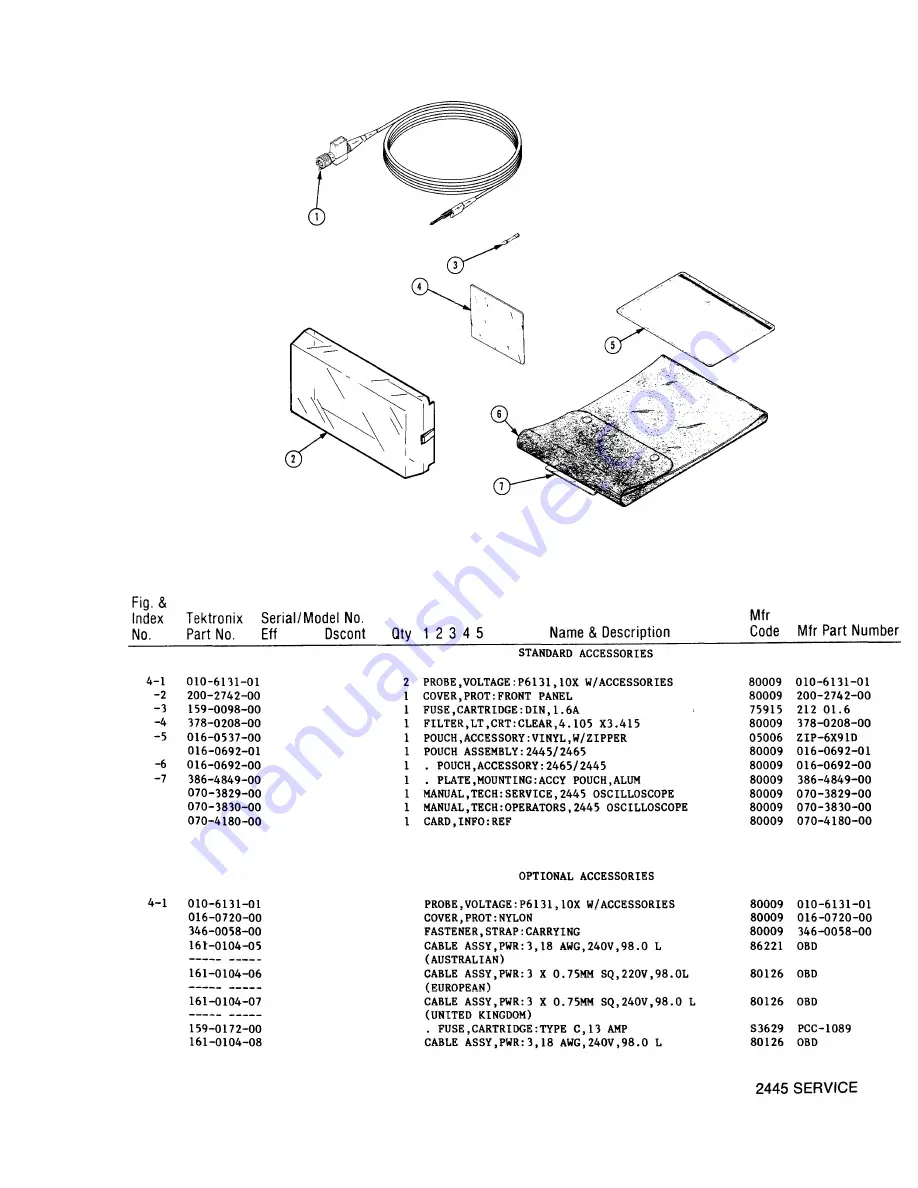
Fig. &
Index
Tektronix
Serial/M odel No.
No.
Part No.
Eft
Dscont
Qty 1 2 3 4 5
Name & Description
STANDARD ACCESSORIES
Mfr
Code
Mfr Part Number
4-1
010-6131-01
2
PROBE,VOLTAGE:P61 3 1 ,10X W/ACCESSORIES
80009
010-6131-01
-2
200-2742-00
1
COVER,PROT:FRONT PANEL
80009
200-2742-00
-3
159-0098-00
1
FUSE, CARTRIDGE:DIN, 1 . 6A
75915
212 01.6
-4
378-0208-00
1
FILTER,LT,CRT:CLEAR,4.105 X3.415
80009
378-0208-00
-5
016-0537-00
1
POUCH,ACCESSORY:VINYL,W/ZIPPER
05006
ZIP-6X91D
016-0692-01
1
POUCH ASSEMBLY:2445/2465
80009
016-0692-01
-6
016-0692-00
1
. POUCH,ACCESSORY:2465/2445
80009
016-0692-00
-7
386-4849-00
1
. PLATE,MOUNTING:ACCY POUCH,ALUM
80009
386-4849-00
070-3829-00
1
MANUAL, TECH: SERVICE,2445 OSCILLOSCOPE
80009
070-3829-00
070-3830-00
1
MANUAL, TECH:OPERATORS,2445 OSCILLOSCOPE
80009
070-3830-00
070-4180-00
1
CARD,INFO:REF
80009
070-4180-00
4-1
010-6131-01
OPTIONAL ACCESSORIES
PROBE.VOLTAGE:P613 1 ,10X W/ACCESSORIES
80009
010-6131-01
016-0720-00
COVER,PROT:NYLON
80009
016-0720-00
346-0058-00
FASTENER,STRAP:CARRYING
80009
346-0058-00
161-0104-05
CABLE ASSY.PWR:3,18 AWG,240V,98.0 L
86221
OBD
161-0104-06
(AUSTRALIAN)
CABLE ASSY.PWR:3 X 0.75MM SQ,220V,98.0L
80126
OBD
161-0104-07
(EUROPEAN)
CABLE ASSY.PWR:3 X 0.75MM SQ,240V,98.0 L
80126
OBD
159-0172-00
(UNITED KINGDOM)
. FUSE,CARTRIDGE:TYPE C,13 AMP
S3629
PCC-1089
161-0104-08
CABLE ASSY.PWR:3,18 AWG,240V,98.0 L
80126
OBD
2445 SER VIC E
Summary of Contents for 2445
Page 1: ...Tektronix 2445 OSCILLOSCOPE SERVICE INSTRUCTION MANUAL ...
Page 11: ...2445 Service 3829 01 The 2445 Oscilloscope ...
Page 44: ...Theory of Operation 2445 Service 3831 10A Figure 3 1 Block diagram ...
Page 45: ...Theory of Operation 2445 Service 3831 10B Figure 3 1 Block diagram cont 3 3 ...
Page 210: ...3829 58 Figure 9 4 2445 block diagram ...
Page 214: ......
Page 217: ......
Page 219: ...2445 382 72 ...
Page 222: ...2445 ...
Page 231: ...A 1 t C t t F t G t H t ...
Page 233: ......
Page 236: ......
Page 238: ...2445 392 1 75 ...
Page 244: ......
Page 247: ...A 1 C _____ D E F G H J 2445 3811 74 ...
Page 248: ...1 2 3 4 5 6 7 8 9 i o 2445 DISPLAY SEQUENCER TRIG GERING A4B SWEEPS ...
Page 253: ......
Page 263: ... 0 2445 J8 i S ...
Page 264: ...1 2 3 4 5 6 7 i 8 I i 9 10 2445 READOUT ...
Page 275: ......
Page 278: ......
Page 281: ......
Page 283: ... 8VJNR EG 3S 5 fROM P232 5 10 A 15VUNREG 8S F R O Mn i 2445 3 0 2 S 8 I ...
Page 286: ...2445 3823 82 ...
Page 290: ...B H le w o q 87V T S o I R v n i U1 R1873 PARTIAL A9 HIGH VOLTAGE BOARD 2445 ...
Page 299: ...2445 Service DAC REF A5 CONTROL ADJUSTMENT LOCATIONS 3 ...
Page 300: ......
Page 304: ...2 R E TU R N T O 1 ...
Page 305: ...ERROR MESSAGE DIAGNOSTICS ...
Page 306: ...ERROR MESSAGE DIAGNOSTICS ...
Page 307: ...O A A C t rnra g i tiw c t 3829 89 ...
Page 308: ...RETURN TO ...
Page 309: ...FRONT PANEL TROUBLESHOOTING ...
Page 310: ...FRONT PANEL TROUBLESHOOTING ...
Page 311: ...2445 Service 3829 90 ...
Page 316: ...R E TU R N T O v 1 y ...
Page 317: ...SWEEP TROUBLESHOOTING PROCEDURE ...
Page 323: ......
Page 324: ...2445 Service 3829 85 ...
Page 325: ......
Page 326: ... KERNEL NOP DIAGNOSTIC PROCEDURE ...
Page 327: ...10 POWER SUPPLY TROUBLESHOOTING PROCEDURE 3829 94 ...
Page 330: ......
Page 334: ...2445 Service REGULATOR TROUBLESHOOTING PROCEDURE 3829 93 ...
Page 338: ......
Page 346: ...12 2445 SERVICE ...
Page 347: ...2445 SERVICE ...
Page 348: ...2445 SERVICE ...