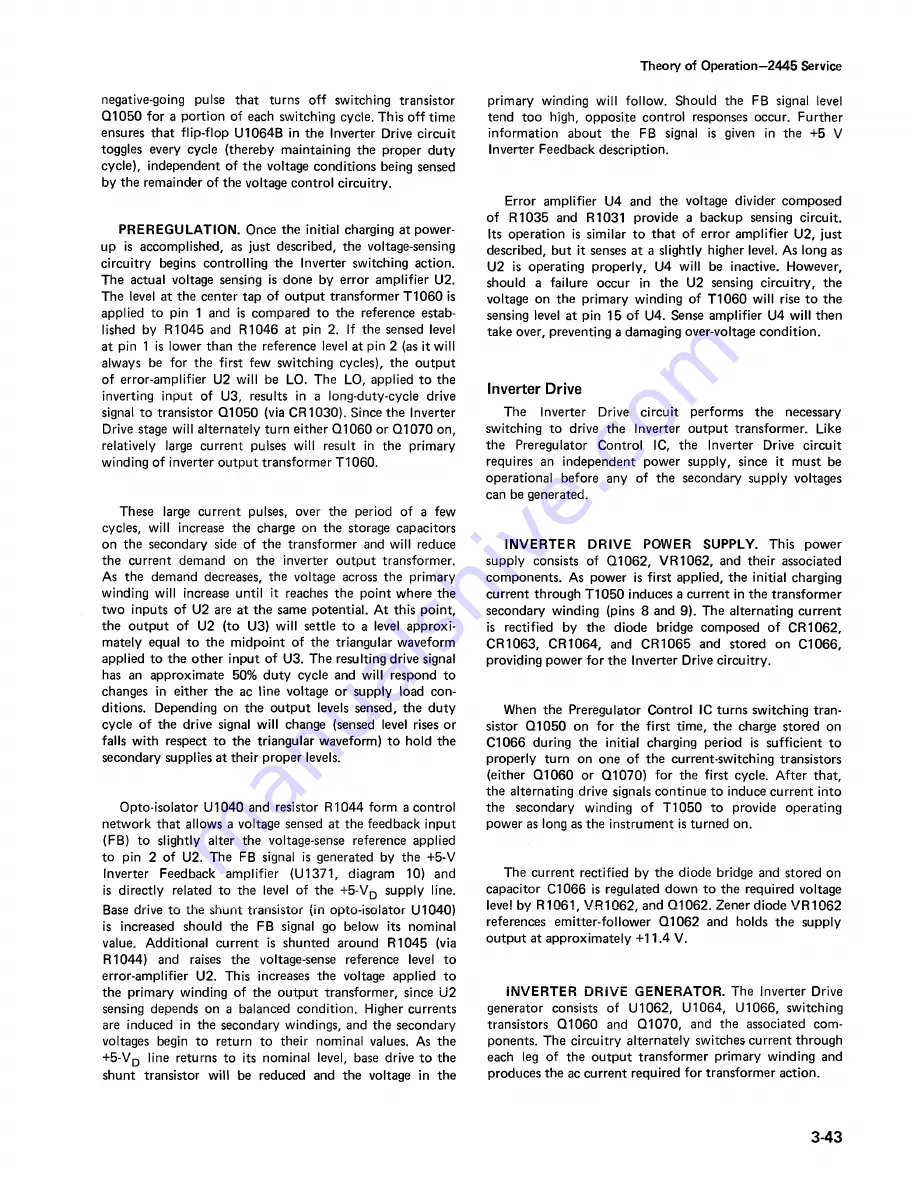
Theory of Operation—2445 Service
negative-going pulse that turns o ff switching transistor
Q1050 fo r a portion of each switching cycle. This o ff time
ensures that flip-flop U1064B in the Inverter Drive circuit
toggles every cycle (thereby maintaining the proper duty
cycle), independent of the voltage conditions being sensed
by the remainder of the voltage control circuitry.
PREREGULATION. Once the initial charging at power-
up is accomplished, as just described, the voltage-sensing
circuitry begins controlling the Inverter switching action.
The actual voltage sensing is done by error amplifier U2.
The level at the center tap of output transformer T1060 is
applied to pin 1 and is compared to the reference estab
lished by R1045 and R1046 at pin 2. If the sensed level
at pin 1 is lower than the reference level at pin 2 (as it w ill
always be for the first few switching cycles), the output
of error-amplifier U2 w ill be LO. The LO, applied to the
inverting input of U3, results in a long-duty-cycle drive
signal to transistor Q1050 (via CR1030). Since the Inverter
Drive stage w ill alternately turn either Q1060 or Q1070 on,
relatively large current pulses w ill result in the primary
winding o f inverter output transformer T1060.
These large current pulses, over the period of a few
cycles, w ill increase the charge on the storage capacitors
on the secondary side of the transformer and w ill reduce
the current demand on the inverter output transformer.
As the demand decreases, the voltage across the primary
winding w ill increase until it reaches the point where the
tw o inputs of U2 are at the same potential. A t this point,
the output of U2 (to U3) w ill settle to a level approxi
mately equal to the m idpoint o f the triangular waveform
applied to the other input o f U3. The resulting drive signal
has an approximate 50% duty cycle and w ill respond to
changes in either the ac line voltage or supply load con
ditions. Depending on the output levels sensed, the duty
cycle o f the drive signal w ill change (sensed level rises or
falls w ith respect to the triangular waveform) to hold the
secondary supplies at their proper levels.
Opto-isolator U1040 and resistor R1044 form a control
network that allows a voltage sensed at the feedback input
(FB) to slightly alter the voltage-sense reference applied
to pin 2 of U2. The FB signal is generated by the +5-V
Inverter Feedback amplifier (U1371, diagram 10) and
is directly related to the level of the +5-VD supply line.
Base drive to the shunt transistor (in opto-isoiator U1040)
is increased should the FB signal go below its nominal
value. Additional current is shunted around R1045 (via
R1044) and raises the voltage-sense reference level to
error-amplifier U2. This increases the voltage applied to
the primary winding of the output transformer, since U2
sensing depends on a balanced condition. Higher currents
are induced in the secondary windings, and the secondary
voltages begin to return to their nominal values. As the
+5-V
d
line returns to its nominal level, base drive to the
shunt transistor w ill be reduced and the voltage in the
primary winding w ill follow . Should the FB signal level
tend too high, opposite control responses occur. Further
information about the FB signal is given in the +5 V
Inverter Feedback description.
Error amplifier U4 and the voltage divider composed
of R1035 and R1031 provide a backup sensing circuit.
Its operation is similar to that o f error amplifier U2, just
described, but it senses at a slightly higher level. As long as
U2 is operating properly, U4 w ill be inactive. However,
should a failure occur in the U2 sensing circuitry, the
voltage on the primary winding of T1060 w ill rise to the
sensing level at pin 15 o f U4. Sense amplifier U4 w ill then
take over, preventing a damaging over-voltage condition.
Inverter Drive
The Inverter Drive circuit performs the necessary
switching to drive the Inverter output transformer. Like
the Preregulator Control 1C, the Inverter Drive circuit
requires an independent power supply, since it must be
operational before any of the secondary supply voltages
can be generated.
INVERTER DRIVE POWER SUPPLY. This power
supply consists of Q1062, VR1062, and their associated
components. As power is first applied, the initial charging
current through T1050 induces a current in the transformer
secondary winding (pins 8 and 9). The alternating current
is rectified by the diode bridge composed o f CR1062,
CR1063, CR1064, and CR1065 and stored on C l 066,
providing power fo r the Inverter Drive circuitry.
When the Preregulator Control 1C turns switching tran
sistor Q1050 on fo r the first time, the charge stored on
C l066 during the initial charging period is sufficient to
properly turn on one o f the current-switching transistors
(either Q1060 or Q1070) for the first cycle. A fter that,
the alternating drive signals continue to induce current into
the secondary winding o f T1050 to provide operating
power as long as the instrument is turned on.
The current rectified by the diode bridge and stored on
capacitor Cl 066 is regulated down to the required voltage
level by R1061, VR1Q62 and Q1Q62. Zener diode VR1Q62
references emitter-follower Q1062 and holds the supply
output at approxi11.4 V.
INVERTER DRiv'E GENERATOR. The inverter Drive
generator consists of U1062, U1064, U1066, switching
transistors Q1060 and Q1070, and the associated com
ponents. The circuitry alternately switches current through
each leg of the output transformer primary winding and
produces the ac current required fo r transformer action.
3-43
Summary of Contents for 2445
Page 1: ...Tektronix 2445 OSCILLOSCOPE SERVICE INSTRUCTION MANUAL ...
Page 11: ...2445 Service 3829 01 The 2445 Oscilloscope ...
Page 44: ...Theory of Operation 2445 Service 3831 10A Figure 3 1 Block diagram ...
Page 45: ...Theory of Operation 2445 Service 3831 10B Figure 3 1 Block diagram cont 3 3 ...
Page 210: ...3829 58 Figure 9 4 2445 block diagram ...
Page 214: ......
Page 217: ......
Page 219: ...2445 382 72 ...
Page 222: ...2445 ...
Page 231: ...A 1 t C t t F t G t H t ...
Page 233: ......
Page 236: ......
Page 238: ...2445 392 1 75 ...
Page 244: ......
Page 247: ...A 1 C _____ D E F G H J 2445 3811 74 ...
Page 248: ...1 2 3 4 5 6 7 8 9 i o 2445 DISPLAY SEQUENCER TRIG GERING A4B SWEEPS ...
Page 253: ......
Page 263: ... 0 2445 J8 i S ...
Page 264: ...1 2 3 4 5 6 7 i 8 I i 9 10 2445 READOUT ...
Page 275: ......
Page 278: ......
Page 281: ......
Page 283: ... 8VJNR EG 3S 5 fROM P232 5 10 A 15VUNREG 8S F R O Mn i 2445 3 0 2 S 8 I ...
Page 286: ...2445 3823 82 ...
Page 290: ...B H le w o q 87V T S o I R v n i U1 R1873 PARTIAL A9 HIGH VOLTAGE BOARD 2445 ...
Page 299: ...2445 Service DAC REF A5 CONTROL ADJUSTMENT LOCATIONS 3 ...
Page 300: ......
Page 304: ...2 R E TU R N T O 1 ...
Page 305: ...ERROR MESSAGE DIAGNOSTICS ...
Page 306: ...ERROR MESSAGE DIAGNOSTICS ...
Page 307: ...O A A C t rnra g i tiw c t 3829 89 ...
Page 308: ...RETURN TO ...
Page 309: ...FRONT PANEL TROUBLESHOOTING ...
Page 310: ...FRONT PANEL TROUBLESHOOTING ...
Page 311: ...2445 Service 3829 90 ...
Page 316: ...R E TU R N T O v 1 y ...
Page 317: ...SWEEP TROUBLESHOOTING PROCEDURE ...
Page 323: ......
Page 324: ...2445 Service 3829 85 ...
Page 325: ......
Page 326: ... KERNEL NOP DIAGNOSTIC PROCEDURE ...
Page 327: ...10 POWER SUPPLY TROUBLESHOOTING PROCEDURE 3829 94 ...
Page 330: ......
Page 334: ...2445 Service REGULATOR TROUBLESHOOTING PROCEDURE 3829 93 ...
Page 338: ......
Page 346: ...12 2445 SERVICE ...
Page 347: ...2445 SERVICE ...
Page 348: ...2445 SERVICE ...