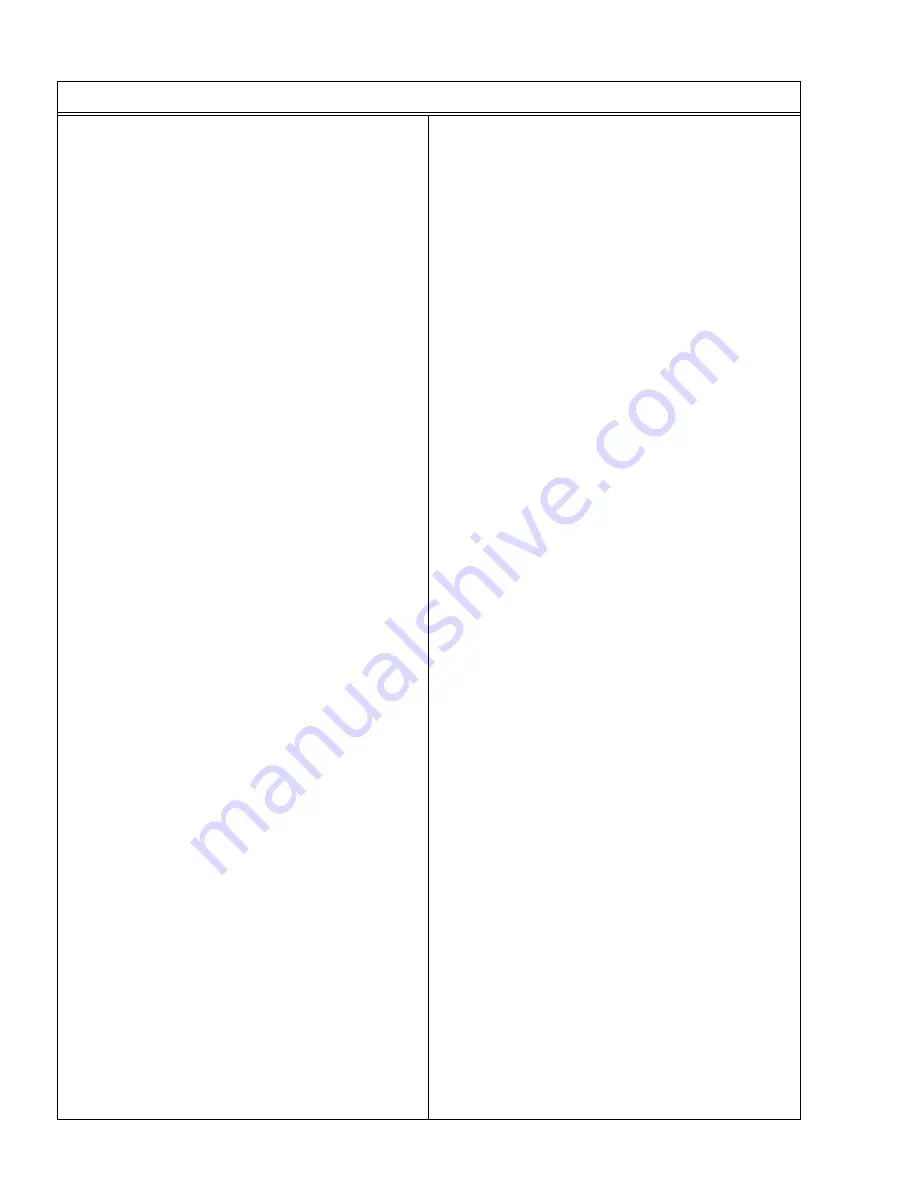
5-12
764333-675
5.2.13 Concentration Monitor Failed
Description
– Control checks concentration monitor
circuit and compares to calculated values, alarm occurs
if below set value.
Action:
1. Faulty CK1 – replace.
2. Scale buildup on CP1 and CP2 – clean.
3. Faulty control board – replace. (Refer to Figure 5-5.)
4. Other:
The concentration reading is monitored while the
unit is full and water is warm from the Heat Rate
Test. The control records the high reading at this
time. While the unit is draining during the drain
and HP pump tests, the control watches the
concentration and records the low reading. (The HP
pump is left on while draining to help blow out the
high pressure transition block.) If the difference
between the high and low reading is not at least
three counts, the test fails.
A failure of this test can be caused by low
conductivity water, failure of the unit to drain
properly, or defective component. Use the
following troubleshooting guide to determine
cause.
Look lat the printout for the following:
CONC
MONITOR FAILED
MINIMUM X
SHOULD READ X
The MINIMUM is the lowest reading that the unit
recorded during the test. Reading must be three
counts less than the high reading. The SHOULD
READ is the minimum reading control expected to
see HIGH READING – 3 COUNTS.
Example:
CONC. MONITOR FAILED
MINIMUM 56
SHOULD READ 55
This means that the high reading was 58 counts
(SHOULD READ +3 counts) and the lowest reading
that the unit saw was 56 counts. The test failed since
the low reading was not three counts less than the
high reading. To troubleshoot the problem, first
verify that the control is functioning properly as
follows:
Unplug CN9 from the interface board and enter the
service mode. Go to CALIB menu and select the
VIEW option. Under the VIEW menu, select CONC
to view the concentration counts. First, place a
jumper between TP1 and TP2 on the interface board.
The counts displayed should be approximately 170.
Next, place the jumper between TP1 and TP3 on the
interface board. The counts displayed should be
approximately 117.
5.2 DIAGNOSTIC CYCLE FAULTS (CONTINUED)
Summary of Contents for SYSTEM 1E
Page 1: ...MAINTENANCE MANUAL SYSTEM 1E Liquid Chemical Sterilant Processing System 12 09 10 P764333 674 ...
Page 3: ......
Page 71: ...5 19 764333 675 Figure 5 2 Analog Cable Assembly Pin Out Locations ...
Page 74: ...5 22 764333 675 Figure 5 7 DC Power Supply Harness Pin Out Locations PS P1 ...
Page 96: ...7 19 764333 675 Figure 7 17 Aquafine STERIUV5 Control Panel The Control Panel A B 3 2 1 ...
Page 108: ......
Page 110: ...ii 764333 676 Example 1 How To Use IPB Page Typical ...
Page 119: ...10 764333 676 Figure 1 SYSTEM 1E Piping Schematic ...
Page 121: ...12 764333 676 Figure 2 SYSTEM 1E Complete 4 3 2 ...
Page 128: ...19 764333 676 Figure 5 Fluid and Air Components 2 of 2 51 53 48 47 50 49 52 ...
Page 133: ...24 764333 676 Figure 7 Float Block Switch Assembly 1 5 8 7 5 4 10 4 2 6 9 9 3 CK2 CK3 LS3 CK1 ...
Page 137: ...28 764333 676 Figure 9 Drain Block Assembly 3 4 5 6 7 3 1 2 8 CK8 TC3 ...
Page 143: ...34 764333 676 Figure 12 Bulkhead Connector Assembly 1 2 2 2 3 1 1 3 5 4 4 6 ...
Page 155: ...46 764333 676 Figure 18 Harness Cable Assemblies 1 of 2 1 2 3 4 5 6 P10 PT1 P5B P11 P2 P5A ...
Page 166: ......
Page 167: ......
Page 168: ......
Page 169: ......
Page 170: ......