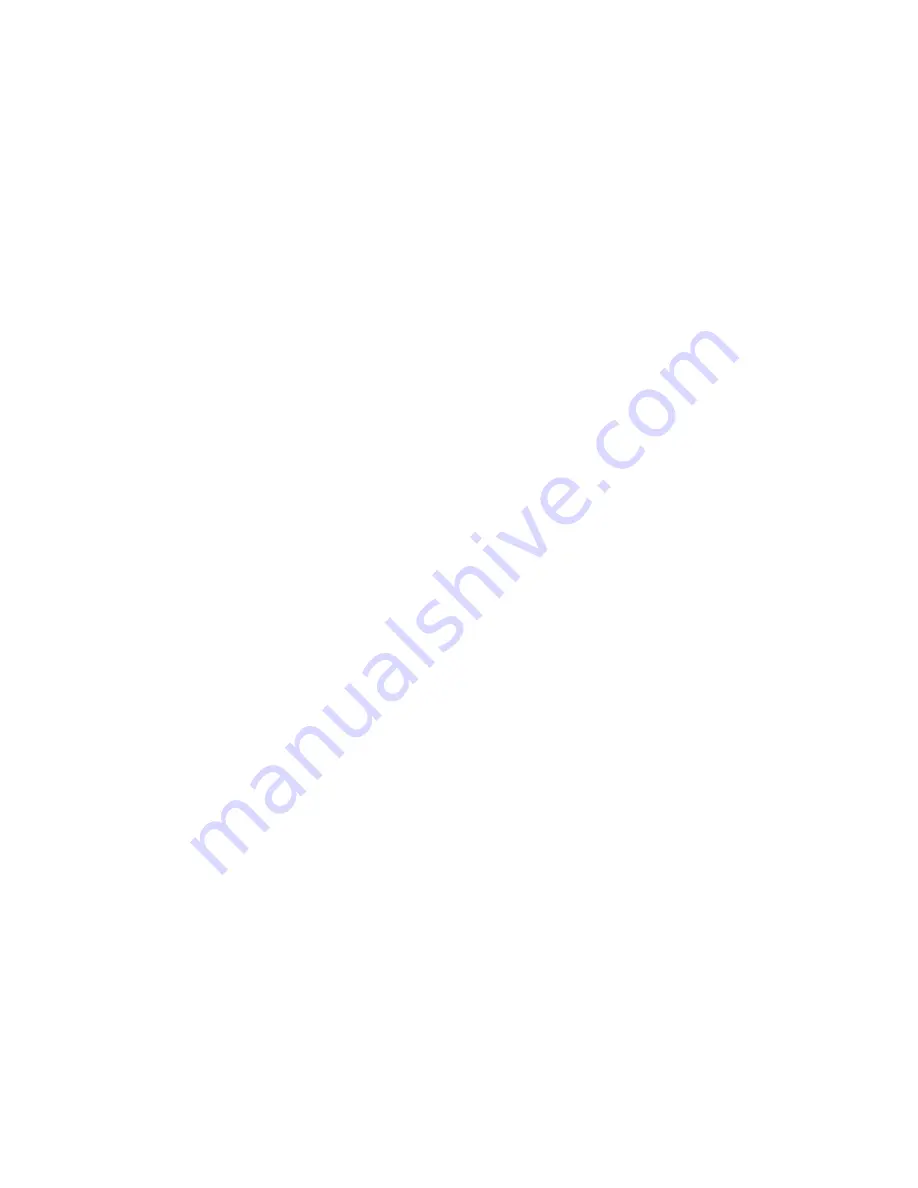
1-6
764333-675
1.5 INSTALLATION CHECKOUT
PROCEDURE
1.5.1 Purpose
This installation checkout procedure, when closely
adhered to, provides:
• Uniform procedures for all installations.
• Complete environmental data for future technical
assistance.
• Means to request Customer assistance in
environmental effects.
• Verification that SYSTEM 1E Processor is
functioning at maximum level.
• Data to track start-up reliability.
1.5.2 General Guidelines
An installation report is to be completed every time an
installation checkout is performed, a unit has been
moved to a new location or major change has been
made to the existing location.
NOTE: When installation checkouts are being
performed on more than one unit, a new installation
report must be completed for each SYSTEM 1E Liquid
Chemical Sterilant Processing System.
Refer to the applicable sections for definitions and use
of particular entries. If there is any confusion regarding
these instructions or completion of the installation
report, contact your supervisor for direction.
1.5.3 Distribution
There is only one copy to the installation report. The
installation report should be attached to the
corresponding field service report.
1.5.4 Procedure
The installation report form should be used to obtain
all information about the Customer and the
SYSTEM 1E Liquid Chemical Sterilant Processing
System at every installation checkout visit.
Complete the form in the following manner:
1.5.5 Electrical Utilities
1.5.6 Water Inlet
• CUST. NO:
Enter complete Customer
number.
• CUST:
Enter full name of Customer
facility
• MODEL NO:
Enter model number of
SYSTEM 1E Liquid Chemical
Sterilant Processing System
(current model number is:
P6500 [115V ac, 60Hz])
• ADDRESS:
Enter address of facility
where SYSTEM 1E Processor
is located.
• SERIAL NO:
Enter serial number of
SYSTEM 1E Processor.
• GFI OUTLET,
GFI BREAKER
OR ISOLATED
POWER:
Enter the type of electrical
outlet: standard, GROUND
FAULT INTERRUPTED
outlet, GFI breaker or
ISOLATED POWER.
• VERIFIED
TRIP:
Check if GFI or (LIM) had
been observed to trip by
using a test button or GFI
tester.
• DUAL/
SINGLE
RECEPTACLE:
Circle one that applies.
IMPORTANT:
Dual receptacle
required for UV light assembly.
• NEMA 5-20R/
OTHER:
Circle if NEMA series 5, 20
Amp, receptacle is provided
and is of hospital grade.
Describe any other
conditions.
• DEDICATED
LINE/OTHER:
Circle if the electrical outlet
is on a dedicated electrical
circuit and rated for 20 Amps
(115V ac). Describe any other
conditions.
• COMMENTS:
Note any unusual conditions
or additional useful
information.
• DUAL
PREFILTER:
Dual prefilter configuration
is standard. No optional
configurations available.
Summary of Contents for SYSTEM 1E
Page 1: ...MAINTENANCE MANUAL SYSTEM 1E Liquid Chemical Sterilant Processing System 12 09 10 P764333 674 ...
Page 3: ......
Page 71: ...5 19 764333 675 Figure 5 2 Analog Cable Assembly Pin Out Locations ...
Page 74: ...5 22 764333 675 Figure 5 7 DC Power Supply Harness Pin Out Locations PS P1 ...
Page 96: ...7 19 764333 675 Figure 7 17 Aquafine STERIUV5 Control Panel The Control Panel A B 3 2 1 ...
Page 108: ......
Page 110: ...ii 764333 676 Example 1 How To Use IPB Page Typical ...
Page 119: ...10 764333 676 Figure 1 SYSTEM 1E Piping Schematic ...
Page 121: ...12 764333 676 Figure 2 SYSTEM 1E Complete 4 3 2 ...
Page 128: ...19 764333 676 Figure 5 Fluid and Air Components 2 of 2 51 53 48 47 50 49 52 ...
Page 133: ...24 764333 676 Figure 7 Float Block Switch Assembly 1 5 8 7 5 4 10 4 2 6 9 9 3 CK2 CK3 LS3 CK1 ...
Page 137: ...28 764333 676 Figure 9 Drain Block Assembly 3 4 5 6 7 3 1 2 8 CK8 TC3 ...
Page 143: ...34 764333 676 Figure 12 Bulkhead Connector Assembly 1 2 2 2 3 1 1 3 5 4 4 6 ...
Page 155: ...46 764333 676 Figure 18 Harness Cable Assemblies 1 of 2 1 2 3 4 5 6 P10 PT1 P5B P11 P2 P5A ...
Page 166: ......
Page 167: ......
Page 168: ......
Page 169: ......
Page 170: ......