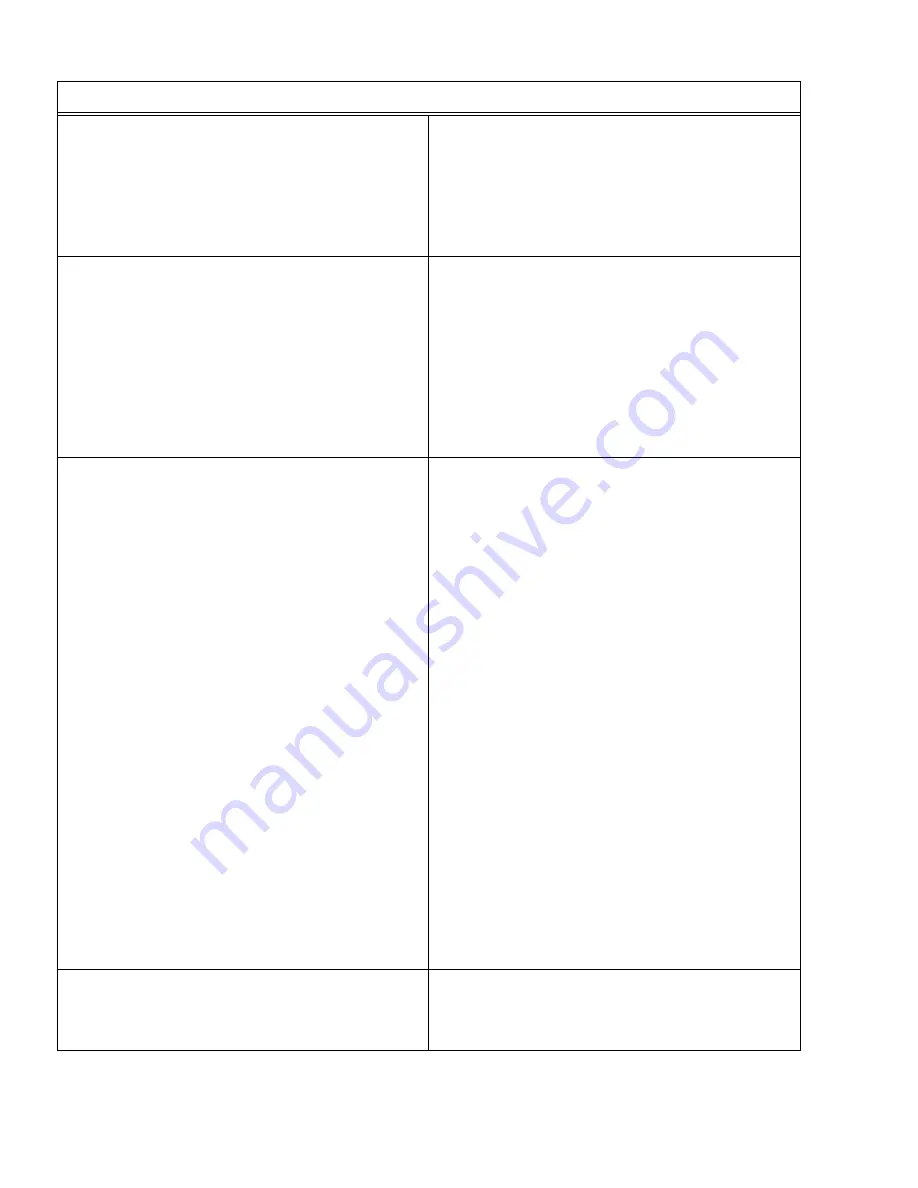
5-6
764333-675
5.1.11 Temperature Over 60°C
Description
– Control senses temperature over 60°C
anytime during cycle.
Action:
1. If during fill phase (including rinse fills) – facility
water supplied too hot, reduce temperature.
2. If after fill phase, faulty HTR or SSR1 – replace.
(Refer to Figure 5-5.)
3. Defective control board – replace.
5.1.12 UV Lamp Problem
Description
- SYSTEM 1E Processor detects a UV
intensity of less than 14.5mA.
Action:
1. Fouled (dirty) quartz sleeve – clean.
2. UV monitor harness not connected – plug into
connector on rear of processor.
3. Faulty UV monitor – replace.
4. Faulty UV lamp – replace.
5. Ballast circuit breaker tripped – reset.
6. Faulty UV lamp ballast – replace.
5.1.13 MaxPure™ Filter Test Failed (a. without
and b. with numbers)
Description
– a. (without numbers) The housing of the
MaxPure Filter is pressurized. The pressure must reach
>55 psi in three minutes or the alarm occurs. If this
portion passes, the housing pressure is maintained for
three minutes. After this three-minute stabilization
period, the pressure must be >52.83 psi or the alarm
occurs. If this portion passes the control waits
15 seconds and checks the housing of the MaxPure
Filter pressure again. The pressure must be >51.73 psi
and <58.75 psi or the alarm occurs.
Action:
1. Air leak – repair.
2. Faulty COMP1 – replace. (Refer to Figure 5-5.)
3. PT1 out of calibration – recalibrate.
4. PT1 – replace. (Refer to Figures 5-1 and 5-2.)
5. Faulty FLT1 – replace.
6. Faulty CK4 – replace.
7. Faulty CK6 – replace.
8. Faulty housing of the MaxPure Filter – repair or
replace.
9. Faulty CK11 – replace.
Description
– b. (with numbers) A two-minute hold
test is performed. The pressure in the housing of the
MaxPure Filter is monitored for two minutes. During
this two-minute hold period, if the pressure drop
exceeds 4.4 psi, an alarm occurs. Three numbers are
printed; start pressure, finish pressure and the elapsed
time of the failure (seconds). Pressure prints are in psi.
Action:
1. Faulty FLT1– replace and rerun test.
2. Air leak – repair.
3. Faulty SOL8 – replace. (Refer to Figure 5-5.)
4. Faulty housing of the MaxPure Filter – replace.
5. PT1 out of calibration – recalibrate.
6. Faulty PT1 – replace. (Refer to Figures 5-1 and 5-2.)
7. Faulty CK11 – replace.
5.1.14 Temperature Problem
Description
– Sensor on control board sees
temperature < 13°C or > 65°C.
Action:
1. Correct room temperature if out of specification.
2. Replace control board if room temperature OK.
5.1 LIQUID CHEMICAL STERILIZATION CYCLE FAULTS (CONTINUED)
Summary of Contents for SYSTEM 1E
Page 1: ...MAINTENANCE MANUAL SYSTEM 1E Liquid Chemical Sterilant Processing System 12 09 10 P764333 674 ...
Page 3: ......
Page 71: ...5 19 764333 675 Figure 5 2 Analog Cable Assembly Pin Out Locations ...
Page 74: ...5 22 764333 675 Figure 5 7 DC Power Supply Harness Pin Out Locations PS P1 ...
Page 96: ...7 19 764333 675 Figure 7 17 Aquafine STERIUV5 Control Panel The Control Panel A B 3 2 1 ...
Page 108: ......
Page 110: ...ii 764333 676 Example 1 How To Use IPB Page Typical ...
Page 119: ...10 764333 676 Figure 1 SYSTEM 1E Piping Schematic ...
Page 121: ...12 764333 676 Figure 2 SYSTEM 1E Complete 4 3 2 ...
Page 128: ...19 764333 676 Figure 5 Fluid and Air Components 2 of 2 51 53 48 47 50 49 52 ...
Page 133: ...24 764333 676 Figure 7 Float Block Switch Assembly 1 5 8 7 5 4 10 4 2 6 9 9 3 CK2 CK3 LS3 CK1 ...
Page 137: ...28 764333 676 Figure 9 Drain Block Assembly 3 4 5 6 7 3 1 2 8 CK8 TC3 ...
Page 143: ...34 764333 676 Figure 12 Bulkhead Connector Assembly 1 2 2 2 3 1 1 3 5 4 4 6 ...
Page 155: ...46 764333 676 Figure 18 Harness Cable Assemblies 1 of 2 1 2 3 4 5 6 P10 PT1 P5B P11 P2 P5A ...
Page 166: ......
Page 167: ......
Page 168: ......
Page 169: ......
Page 170: ......