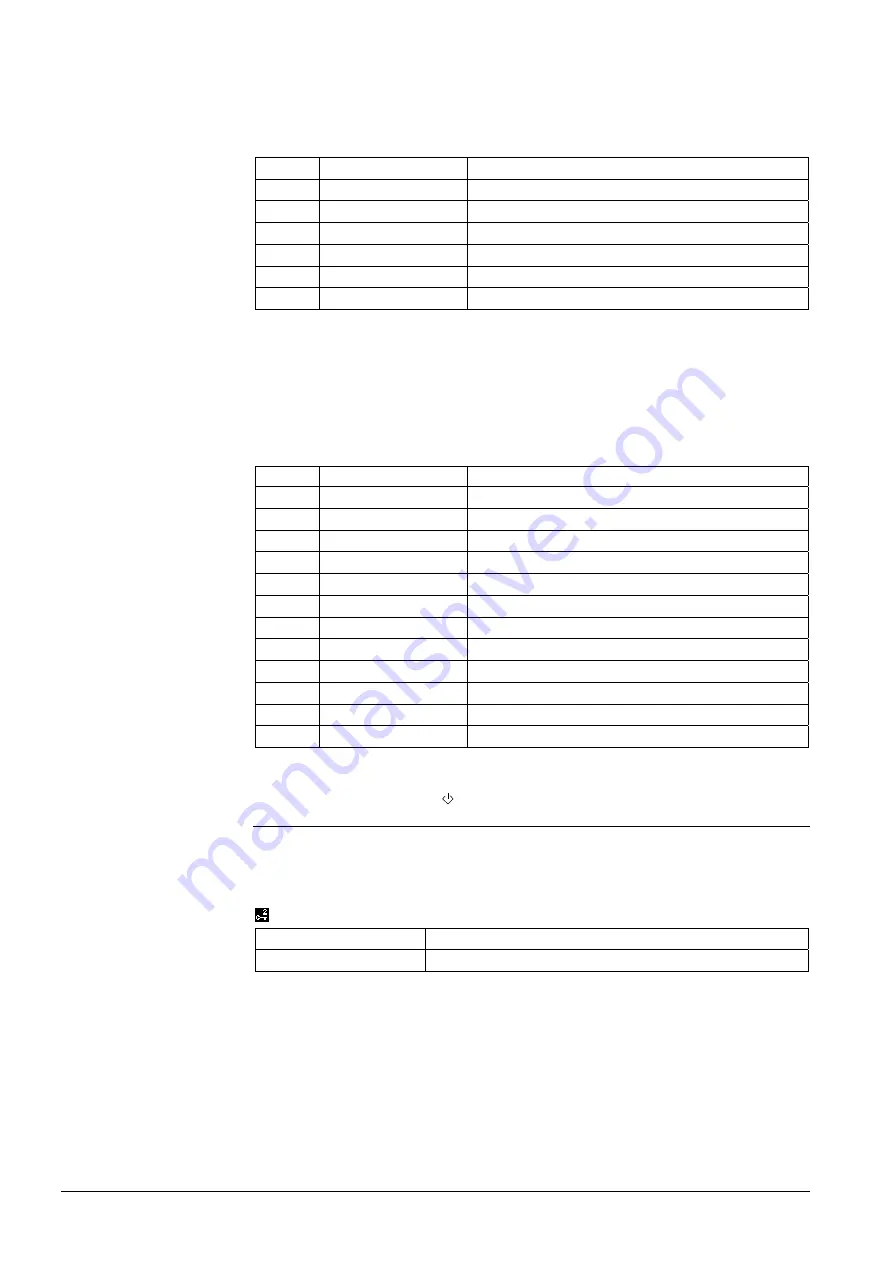
A fault message is displayed and output "Motor fault" is enabled if there is an
overload fault.
You can change the following texts ex-works texts in the RMS705B at the
password level.
No.
Text
Effect with factory setting
1311
[Motor 1] overload
Urgent message; must be acknowledged.
1321
[Motor 2] overload
Urgent message; must be acknowledged.
1331
[Motor 3] overload
Urgent message; must be acknowledged.
1341
[Motor 4] overload
Urgent message; must be acknowledged.
1351
[Motor 5] overload
Urgent message; must be acknowledged.
1361
[Motor 6] overload
Urgent message; must be acknowledged.
Overload messages
1
or
2-speed motor
If only one pump is faulty during twin motor operation, run priority changes to the
non-faulty motor output. The fault acknowledgement setting has no effect on
changeover. The corresponding overload signal is issued. If both motors are faulty,
a fault message is displayed as per Section "8.4.4".
Overload messages
twin motor
You can change the following texts ex-works texts in the RMS705B at the
password level.
No.
Text
Effect with factory setting
1314
[Motor 1A] overload Non-urgent message; must be acknowledged.
1315
[Motor 1B] overload Non-urgent message; must be acknowledged.
1324
[Motor 2A] overload Non-urgent message; must be acknowledged.
1325
[Motor 2B] overload Non-urgent message; must be acknowledged.
1334
[Motor 3A] overload Non-urgent message; must be acknowledged.
1335
[Motor 3B] overload Non-urgent message; must be acknowledged.
1344
[Motor 4A] overload Non-urgent message; must be acknowledged.
1345
[Motor 4B] overload Non-urgent message; must be acknowledged.
1354
[Motor 5A] overload Non-urgent message; must be acknowledged.
1355
[Motor 5B] overload Non-urgent message; must be acknowledged.
1364
[Motor 6A] overload Non-urgent message; must be acknowledged.
1365
[Motor 6B] overload Non-urgent message; must be acknowledged.
8.4.8
Precommand
You can configure a corresponding precommand for each motor. This allows e.g. to
open a damper
or
valve prior to actual motor start as well as shut off the damper
delayed following motor switch-off.
Main menu > Commissioning > Extra configuration > Aggregates > Motor > Motor 1...6 >
Configuration
Operating line
Adjustable values / Comment
Precommand
---, N.Q1, N.Q2, ... (free outputs only)
The precommand switches on if switch-on takes place via start condition 1
or
2.
The motors can be started or stopped with the "Precommand" simultaneously
or
delayed. Set delayed switch-on/off via "Precommand runup time" and
"Precommand rundown time".
116 / 216
Siemens
Switching and monitoring device RMS705B
CE1P3124en
Building Technologies
Aggregates
01.04.2010