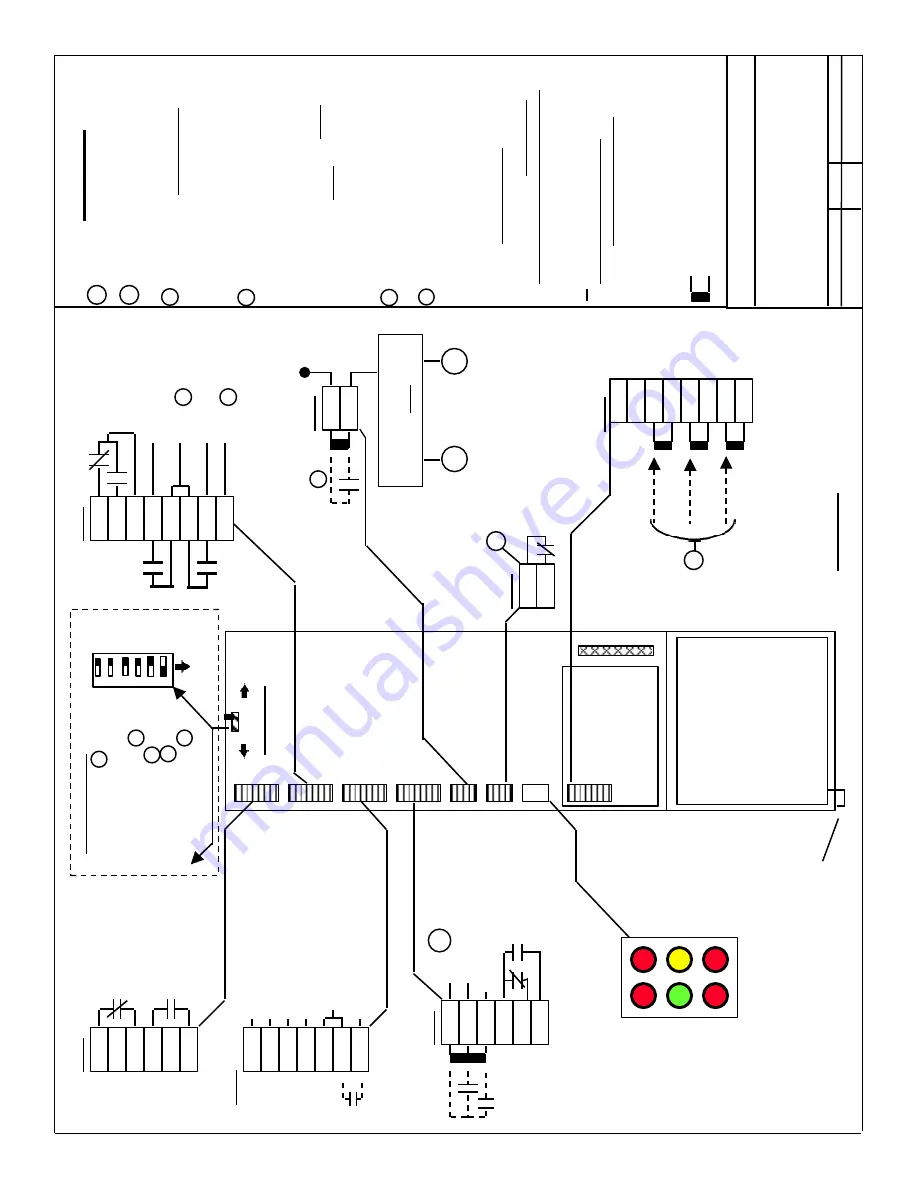
3
Siemens Energy & Automation
Machine Industry Business
Drawing for:
Interface connections
for Supply
Infeed
Modules
( 16, 36, & 55
KW
)
Date by Revision
8 / 13 / 98 de/
dk
Rev. A5
74
73.2
73.1
72
X111
(6SY9896
)
Ready / Fault
Status Relay
Output
(250VAC / 1 Amp.
30VDC / 1Amp.)
7
45
44
10
15
15
R
P(+)24
P(+)15
N(-) 15
N(-) 24
M
(P. S. Common )
Reset
Drive’s
Internal
Power
Supplies
Set-Up / Standard Operation
Internal Line
Contactor
Control
LED Status
Indications
5V(Red)
Ready(
Yel
.)
DC Link
Over Volt.(Red)
15V(Red)
63,64 or 48(
Grn
)
(not enabled)
Line(Red)
X161
9
112
48
111
113
Status of the Internal
Line
Contactor
FR+
X121
(6SY9897)
5.3
5.2
5.1
63
9
9
64
19
FR-
I
2
T & Motor
Over Temp.
Monitoring
(30 V / 1 Amp. )
Pulse Enable
Drive Enable
FR+
6SN1145-1B...
Supply
Infeed
Module
D C Link
Cover
NOTES:
1
These functions are not included on the
10,28
KW
Unregulated Modules.
2
X172
AS1
AS2
Set-up mode. Closed
with power
off, or terminal 112 open.
( 250 VAC / 50 VDC / 2A Max.
5 VDC / 10ma Min.)
X172
1
This Optional Input is used only when
line voltage is supplied separately to the
the L. V. Power Supply. (1 place)
For additional information on terminal
definition, use and operation see the
“Planning Guide” (Sect. 3.7...).
Indicates Factory supplied
“Jumper”
Items shown on the
left side of the
connectors are external connections
to be supplied by the installer.
#
Connections shown with a “ # “ and
not connected are Optional
- the one’s
shown
connected are Required
for
drive operation.
3
3
FR+ & FR- are
internal supplies
to be
used as a power source for the drive’s en-
ables
(3 Places). If using an ex24V
source for controlling enables, connect the
external source’s P. S. common to Term.-19
Internal Power Source for
the Drive’s Internal
Contactors
4 NS1 & NS2 are provided for non- electronic control of the drive’s internal power relays. They can be used in the E-Stop circuit or in a lock-out circuit to provide a direct interruption of the power supplied to the internal relays.
NOTE
:
Terminal X161- 48
MUST
be opened prior
to or at the same time as NS1 & NS2, to
provide internal shut down of the drive
circuits. ( 1 Place )
General Notes
#
#
M500
P500
2U1
1U1
2V1
1V1
2W1
1W1
X181
2
#
On - Off
Switch “S1”
located
on TOP of Module
Page 2 / 4
Front & top
of Module
S1
625 V 1 600 V
Fault
2 Ready
No
3 Yes
480V 4 400V
No
5 Yes
Sine 6 Trap
3
Internal Electronic Relay
Control (via
X161
- 48 )
Internal
Drive
Contactors
(Precharge
) ( Line)
X171
NS1
NS2
4
#
Section C
1
2
3
Regenerate to Lines 1
4
480 V operation 5
5
Controlled
Infeed
1
6
Current control mode 6
Ready / Fault Relay
DC Link Voltage 1
S1 Bit Definitions
5
Adapt to line voltage. Standard setting
is for 400 V operation.
Sets type of current control mode.
Standard setting is Sinusoidal.
213
X141
(6SY9898)
(6SY9896)
(6SY9433)
(6SY9433)
(6SY9900)
6
Overvoltage
Module
See Page 3/4
DC Link Cover Shield wire
connected to bottom of module
1-169
Summary of Contents for SIMODRIVE 611A
Page 2: ......
Page 6: ......
Page 7: ...SECTION 0 PRELIMINARY INFORMATION 0 7 ...
Page 8: ......
Page 17: ...Section 1 611A Analog Feed Drives 1 17 ...
Page 18: ...1 18 ...
Page 24: ...1 24 ...
Page 39: ...1 39 ...
Page 70: ...1 70 ...
Page 119: ...1 119 ...
Page 120: ......
Page 123: ......
Page 131: ......
Page 158: ...1 158 ...
Page 159: ...1 159 MOUNTING DIMENSIONS ...
Page 160: ...1 160 ...
Page 186: ......
Page 187: ...GENERAL INFORMATION REGARDING AC SERVO MOTORS AL S ...
Page 188: ......
Page 225: ...1FT5 AC SERVO MOTOR DESCRIPTIONS 1FT5 ...
Page 226: ......
Page 321: ...FEEDBACK DEVICES FOR 1FT5 GE ...
Page 322: ......