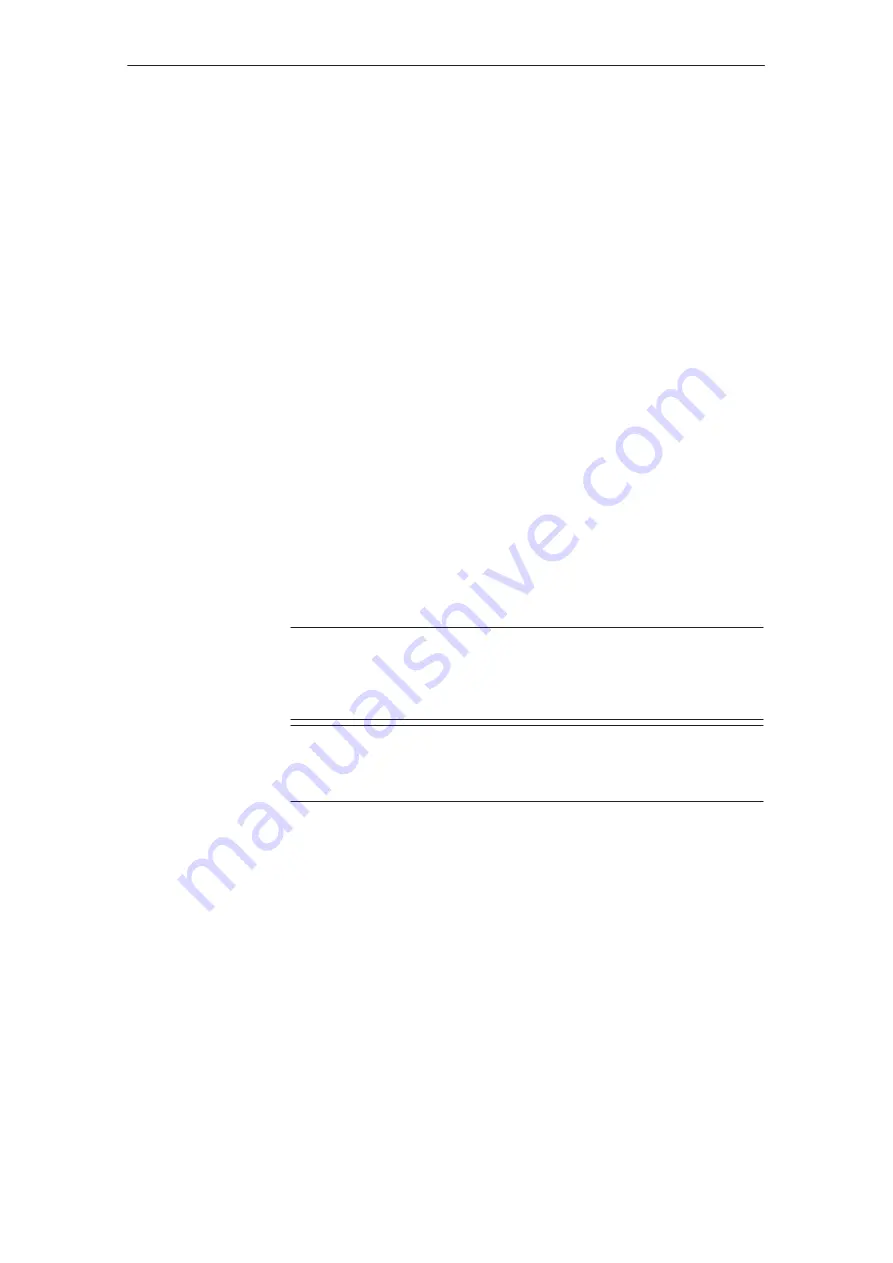
9
02.98
1-143
Siemens AG 1998 All Rights reserved 6SN1197–0AA00 02.98 Edition
SIMODRIVE 611 (PJ)
Mode of operation of the start inhibit
The inverter power section controls the current through the individual motor
windings. 1FT5 motors are fed with square–wave currents and 1FT6– and in-
duction motors with sinusoidal currents.
A pulse generating logic clocks the 6 power transistors in a three–phase ori-
ented pulse pattern. An optocoupler is provided in every transistor arm between
the gating logic and the power section gating amplifier. These optocouplers pro-
vide the electrical isolation.
The start inhibit acts, for each module. A positively–driven relay (permitted ac-
cording to ZH1/457 to TÜV) acts on the inverter gating on the particular drive
module at the input circuits of the optocouplers. A relay contact interrupts the
power supply for the optocoupler inputs. Thus, no signals can be transferred
through the optocoupler. The pulse generating logic is inhibited through an addi-
tional electrically isolated arm. These two active circuits are controlled in parallel
from the machine control via terminal 663 (motor start inhibit) for the drive mod-
ules, or via terminal 112 (step–up controller, start inhibit) for the supply infeed
modules. The status of the relay contact, located in the pulse power supply cir-
cuit, is signaled to the external adaptation circuit via a positively–driven NC con-
tact. The signaling contact is accessible at module terminals AS1 and AS2, and
the user can interlock it with the safety control. When the start inhibit fails, these
start–inhibit signaling contacts must isolate the supply infeed from the supply
via the power contactor (line contactor in the supply module).
If the start inhibit circuit is activated, it is no longer possible to control the power
transistors in a rotating field orientation. If two power transistors are destroyed
(short–circuit) in the most unfavorable constellation, then this results in residual
risk .
Note
When the start inhibit is activated, the motor can no longer generate a torque.
Drives which do not automatically lock when powered–down (e.g. hanging
axes), must be clamped using a mechanical brake.
Note
When a fault condition develops, linear motors can continue to rotate through
180
0
electrical (approx. 56 or 72 mm incl. overshoot) .
9.5.2 Mode of operation of the start inhibit
Summary of Contents for SIMODRIVE 611A
Page 2: ......
Page 6: ......
Page 7: ...SECTION 0 PRELIMINARY INFORMATION 0 7 ...
Page 8: ......
Page 17: ...Section 1 611A Analog Feed Drives 1 17 ...
Page 18: ...1 18 ...
Page 24: ...1 24 ...
Page 39: ...1 39 ...
Page 70: ...1 70 ...
Page 119: ...1 119 ...
Page 120: ......
Page 123: ......
Page 131: ......
Page 158: ...1 158 ...
Page 159: ...1 159 MOUNTING DIMENSIONS ...
Page 160: ...1 160 ...
Page 186: ......
Page 187: ...GENERAL INFORMATION REGARDING AC SERVO MOTORS AL S ...
Page 188: ......
Page 225: ...1FT5 AC SERVO MOTOR DESCRIPTIONS 1FT5 ...
Page 226: ......
Page 321: ...FEEDBACK DEVICES FOR 1FT5 GE ...
Page 322: ......