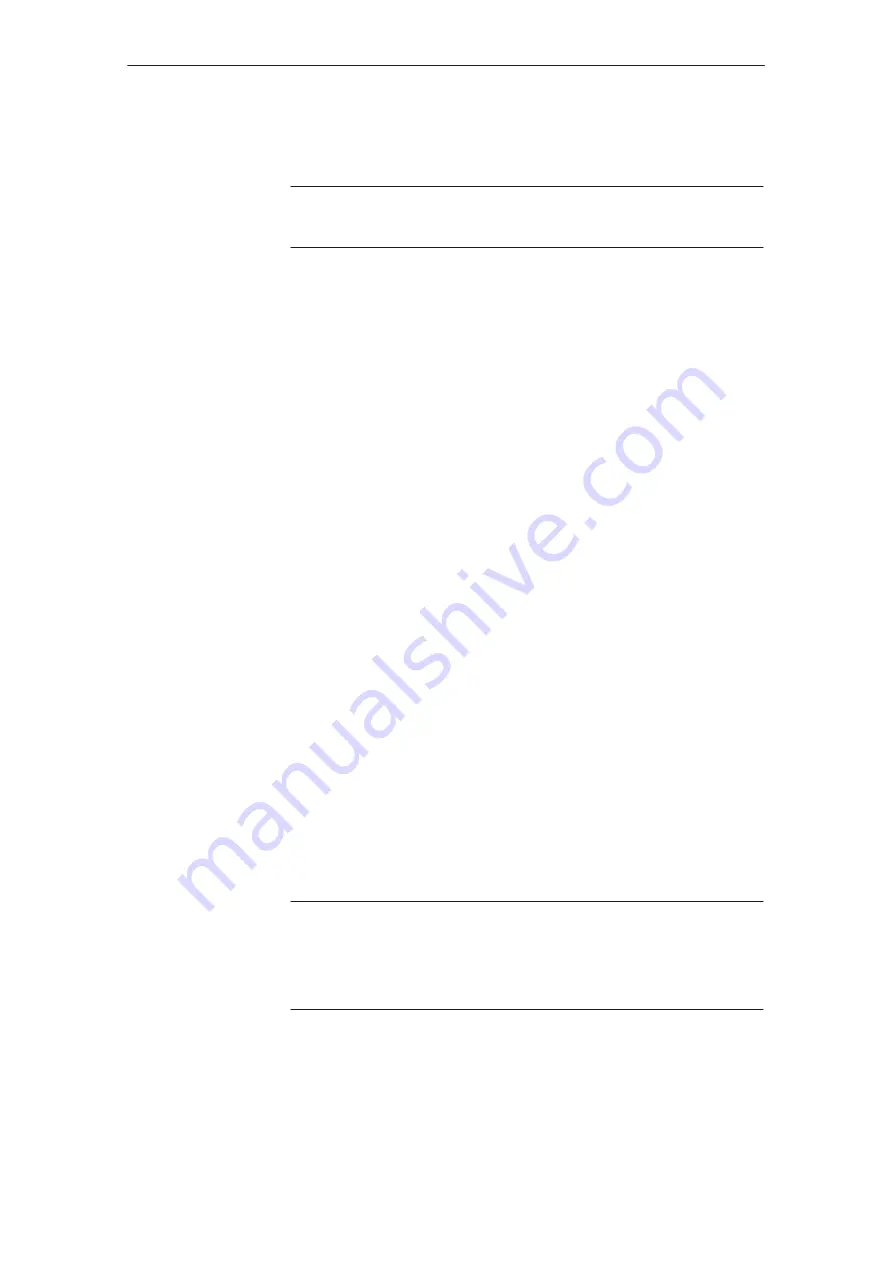
9
02.98
1-151
Siemens AG 1998 All Rights reserved 6SN1197–0AA00 02.98 Edition
SIMODRIVE 611 (PJ)
The following explanations are valid for both application example 1 (Fig. 9-6) as
well as for application example 2 (Fig. 9-7).
Note
1) The safety relay drop–out time is 40 ms.
2) The contactor drop–out time for braking the FD can be up to 200 ms. Lon-
ger times can occur using a common braking time for feed drives and main
spindle/induction motors.
3) K8 and K9 must be additionally used for separate braking times for main
spindle drive/induction motor and feed drives.
4) The contactor contact combination must be looped–in if there are different
braking times for the main spindle drives/induction motor– and feed drive
modules, which includes the longest braking time. This means, that when
using K8, K9 with longer drop–out times than for K6, K7, then instead of
K6, K7 – K8, K9 must be looped–into the circuit.
5) The emergency trip is signaled to the PLC.
6) If the machine may only be entered in the setting–up mode, contact S1
(key–actuated switch) must be additionally incorporated.
7) When using a main spindle drive/induction motor module with ramp–func-
tion generator – fast stop
8) No commands may be issued which could initiate or result in a hazardous
status (VDI 2854 3.3.6).
9) Key–actuated switch S1 is only required for setting–up operation with redu-
ced DC link voltage.
10) Redundancy according to a machine manufacturers fault analysis. Fault
analyses must always be made.
11) Power–up frequency of the machine is limited according to the Configuring
Guide, Section 9.4.2
12) The individual drives must be switched via terminal 663.
13) Can be used to reduce the contactor deadtimes.
All contacts are illustrated in the quiescent setting.
– in this case, the protective barriers are closed, TK1; TK2
– the start inhibit is activated AS1/AS2
– key–activated switch S1 has been used to select setting–up operation
Note
The safety–related monitoring contacts for the start inhibit (AS1; AS2), door
contacts (TK) of the machining zone protective device and the safety switch
must be cyclically monitored by the machine control to ensure that they are
functioning correctly.
9.5.9 Application examples
Summary of Contents for SIMODRIVE 611A
Page 2: ......
Page 6: ......
Page 7: ...SECTION 0 PRELIMINARY INFORMATION 0 7 ...
Page 8: ......
Page 17: ...Section 1 611A Analog Feed Drives 1 17 ...
Page 18: ...1 18 ...
Page 24: ...1 24 ...
Page 39: ...1 39 ...
Page 70: ...1 70 ...
Page 119: ...1 119 ...
Page 120: ......
Page 123: ......
Page 131: ......
Page 158: ...1 158 ...
Page 159: ...1 159 MOUNTING DIMENSIONS ...
Page 160: ...1 160 ...
Page 186: ......
Page 187: ...GENERAL INFORMATION REGARDING AC SERVO MOTORS AL S ...
Page 188: ......
Page 225: ...1FT5 AC SERVO MOTOR DESCRIPTIONS 1FT5 ...
Page 226: ......
Page 321: ...FEEDBACK DEVICES FOR 1FT5 GE ...
Page 322: ......