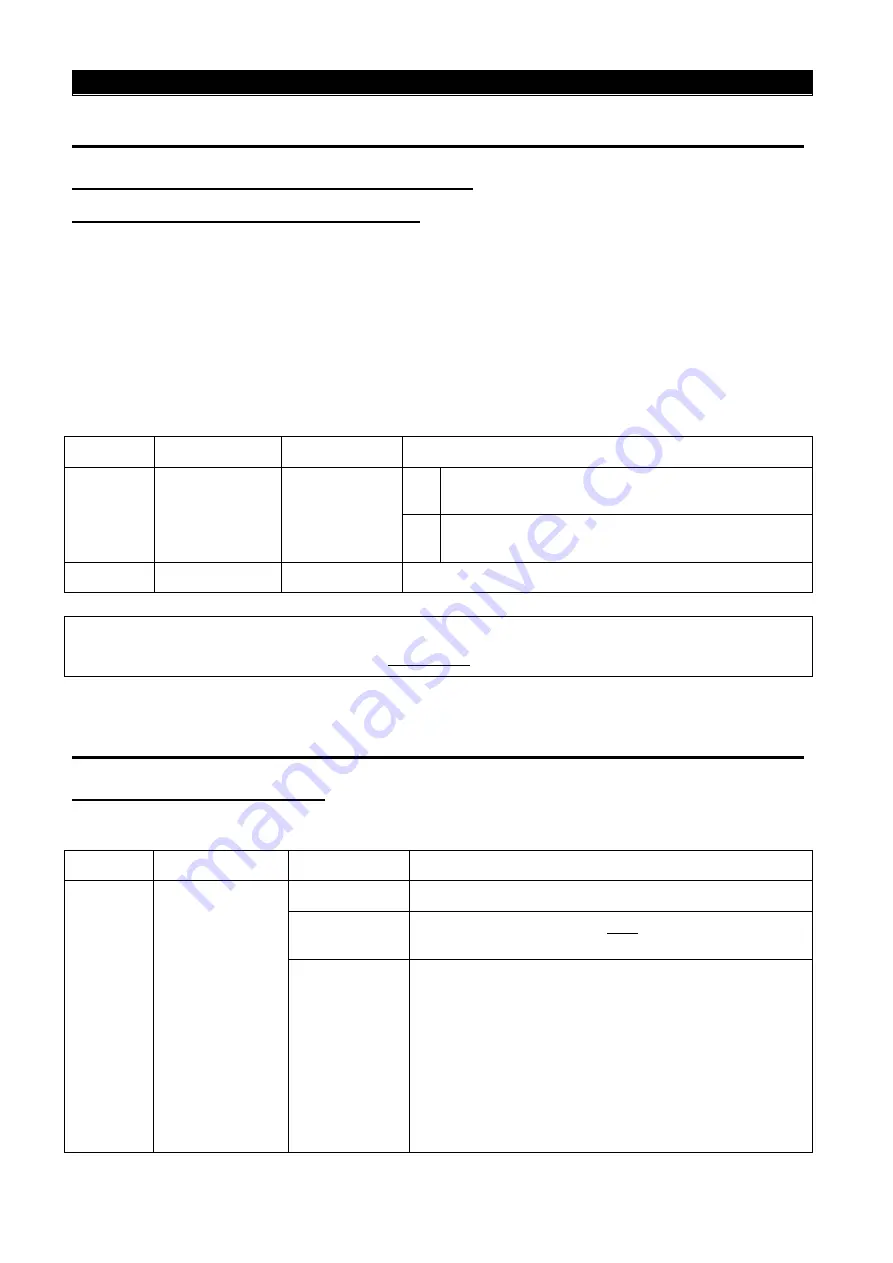
Parameter Description
Parameter Description
61
5.14 Regenerative Brake (P.30, P.70)
P.30 “Regenerative brake function selection”
P.70 “Special regenerative brake duty”
● Changing the output frequency from high to low will cause the motor speed to be greater than the
output frequency of the inverter due to load inertia and thereby inducing the generator effect. In
this case, a high voltage will exist between the main-circuit ter/P and -/N and damage the
inverter. Therefore, a proper brake resistor shall be mounted between terminals +/P and PR to
dissipate the feedback energy.
● There is a built-in transistor in the inverter. The conducting time ratio of the transistor is referred to
as the regenerative brake duty. The higher the regenerative brake duty is, the more energy the
brake resistor consumes, and the stronger the brake capability is.
Parameter Factory Setting Setting Range
Remarks
30
0
0~1
0
If regenerative brake duty is 3% fixed, the value
of parameter 70 is invalid.
1
The regenerative brake duty is the value of
parameter 70 setting.
70
0
0~30%
---
Note: 1. In occasions where frequent start/stop occurs, a high capacity brake resistor is required.
2. For brake resistor options, please refer to Section 3.6.3.
5.15 Soft-PWM Selection (P.31)
P.31 “Soft-PWM selection”
●
Soft-PWM
is a method for eliminating motor noises.
Parameter Factory Setting
Setting Range
Remarks
31
0
0
No action
1
Soft-PWM selected when P.72
<
5, this function is
only valid under the V/F mode.
2
The rated current is kept, and actual carrier is
reduced according to the module temperature.
When P.72
>
9, if inverter module temperature is
higher than 60
℃
, carriers frequency will
automatically reduce to 9K, after the module
temperature falling to lower than 40
℃
, carrier
frequency will automatically restore the P.72 setting
value.