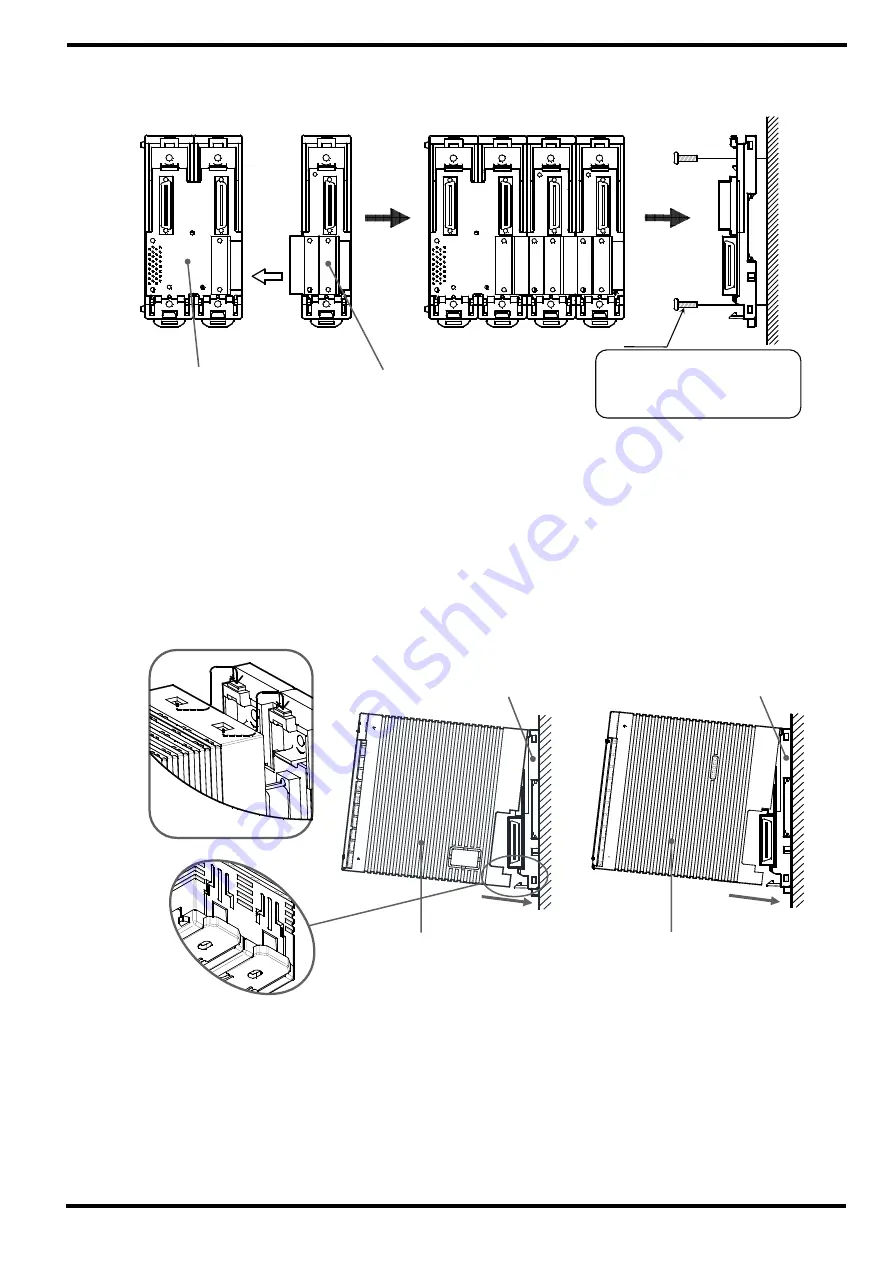
SAMWONTECH
2nd Edition of TEMP2000M_Series IM : April. 8. 2014 Page 13 / 176
3) Assemble back cover and fix on the wall with screw.
▪ Be cautious for the foreign material not to be put into the connector in case of fixing the back
cover on the wall. (Possibility of communication connection fault)
▪ Be cautious for the exposed board surface not to be scratched or damaged.
4) Insert the upper part of the main and sub body on the main/sub back cover and assemble for hook
to be locked fully by pushing the lower part.
▪
Check whether the hook is fully assembly after assembling the product main body to the back
cover assembly.
- There is a big possibility of communication/function disorder when it is incompletely assembled.
Main unit
BACK COVER
Sub unit
BACK COVER
Fastening torque
recommended for screw
0.3 N∙m(3㎏f∙㎝)
M3X12
Main unit
Sub unit
PUSH
PUSH
Sub body
Main body
Main BACK COVER ASSY
Sub BACK COVER ASSY
Summary of Contents for Temp 2000 M
Page 1: ...Instruction Manual...