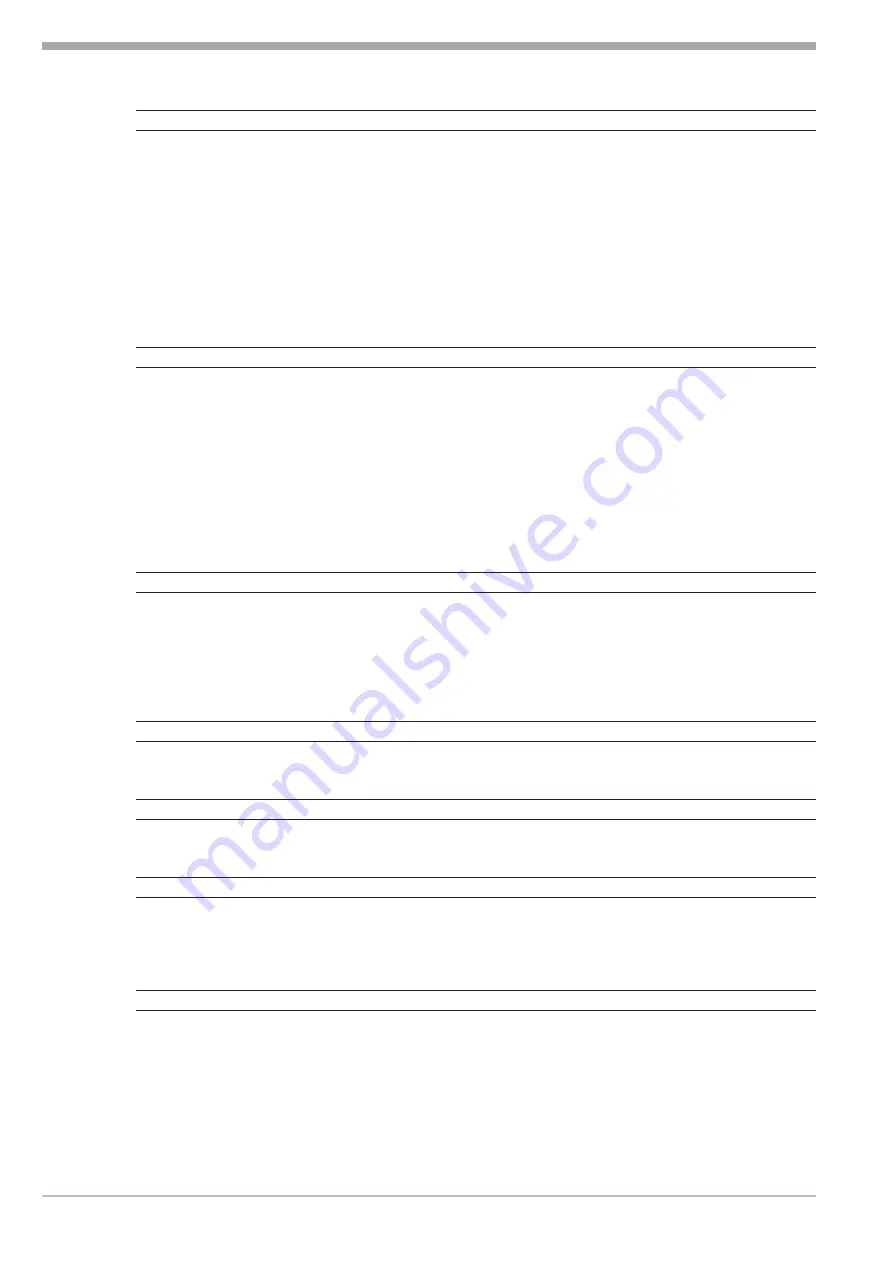
KS98+ CAN communication features
Every message on the bus activates the KS98 interrupt handler and loads the processor. The message is analyzed and
queued, if the destination of the message is the own address. This queue is handled in the idle task and during the cy-
clical system processing phase (at intervals of 100ms).
70% of the CPU capacity is reserved for the engineering. This time is considered as 100 % in the KS98 ET timing dia-
logue. I.e. Min. 30ms are available for general tasks and communication. Included are front and rear instrument inter-
face processing and Profibus handling. However, these loads are insignificant, because, for example, front and rear
interface can only receive one telegram per 100 ms. This means that the CAN communication causes the largest part of
the CPU load.
The PDO handling program is activated, as soon as the processing phase for the engineering within a cycle is finished
(idle-task). Hence, more than 30 % of the processor capacity may be available for CAN communication with small
engineerings. The user can decide freely and at his own responsibility how to use these reserves can.
Receive PDOs
The interrupt handler requires approx. 0,16ms for each PDO.
The event queues comprise 4 x 80 items. There is a queue for all send messages, another one for all PDO receive mes-
sages, still another one for the network receive messages and still another one for the SDO receive messages.
The queues are handled at intervals of 100 ms and during the idle task.
This means that no more than 80 PDOs per 100ms may be received.
The PDO handling is a processor load of approx. 1,2 ms for each individual PDO.
Blockwise handling of 50 receive PDOs takes KS98 18 ms (19 ms, if the same number of PDOs for other receivers are
rejected).
Although the load of the basic communication blocks (C_RM2X, CPREAD, ...) cannot be allocated to a time slot, it is as-
signed as a fixed value to the engineering portion automatically.
Send PDOs
The load for transmitted PDOs is nearly the same as for receive PDOs (18ms / 50 PDOs), however, sending is not cycli-
cal.
PDOs are sent only, when a value has changed (threshold adjustable with CSEND, otherwise, there will be a change of
accuracy of the transmitted data format). At the latest after 2 seconds, the values are sent again also if unchanged.
This reduces the output load by an unpredictable percentage. A filter can be used to reduce the transmission frequency
of instable data.
Estimation of CAN bus activities of various instruments
For reducing the data traffic between PMA instruments, PDOs are transmitted only in case of data changes.
The changes are read with the accuracy of the used data format (LSB).
KS800 communication
Both synchronous and asynchronous communication are used for KS800 communication. By configuration, one PDO is
defined as synchronous and one PDO is defined as asynchronous.
A Sync message is sent at intervals of 200ms.
This is followed by reception of a PDO containing the data of
one
controller channel by each KS800/816 . I.e. refresh-
ing of 8 channels takes 1,6 seconds.
The internal KS800/816 cycle for handling a controller channel is 63,5 ms. If a channel status or correcting variable
change occurs during this cycle time, KS800/81 sends 1 PDO asynchronously.
RM 200
Data transmission in both directions is asynchronous. Data are transmitted only if changed (only the related PDOs).
Checking, if changes were made is dependent on the accuracy of the data format (LSB). In both directions, the min. re-
fresh rate is 100 ms.
Max. 5 PDOs + 1status PDO are sent by the RM node dependent on the number of modules in the nodes.
Max. 5 PDOs are sent to the RM node by KS98.
Description of KS98 CAN bus extension
9499 040 50611
138
Summary of Contents for KS 98
Page 8: ...Description 9499 040 50611 Construction 8...
Page 10: ...Important technical data 9499 040 50611 Further external in and outputs 10...
Page 12: ...Versions 9499 040 50611 I O modules for units with modular option c basic card 12...
Page 14: ...Front view 9499 040 50611 14...
Page 16: ...Mounting 9499 040 50611 16...
Page 26: ...Maintenance 9499 040 50611 Further information 26...
Page 36: ...Scaling and calculating functions 9499 040 50611 LG10 10s logarithm 36...
Page 74: ...Signal converters 9499 040 50611 MEAN mean value formation 74...
Page 128: ...KS98 I O extensions with CANopen 9499 040 50611 RM_DMS strain gauge module 128...
Page 132: ...CSEND Send mod blockno s 21 23 25 27 No 57 132...
Page 140: ...Description of KS98 CAN bus extension 9499 040 50611 140...
Page 202: ...Controller 9499 040 50611 Process value calculation 202...