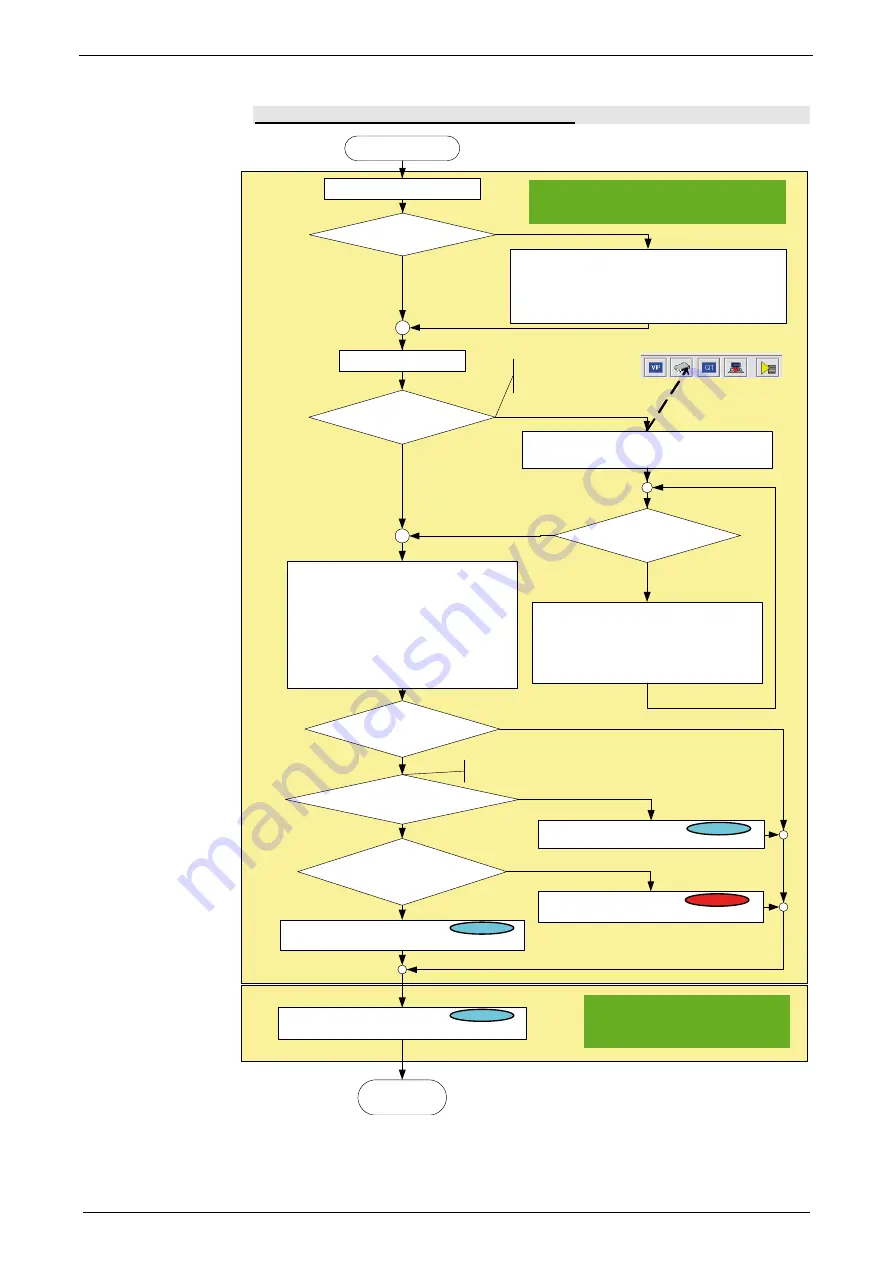
Setting
up Compax3
Positioning via digital I/Os
176
192-120101 N11 C3I11T11 November 2007
Main flow chart of the controller optimization
Is the controlled system oscillating ?
See chapter
“Controller optimization of toothed belt drive”
See chapter
“Controller optimization guiding behavior”
End
Start
Check consistency of the entire system :
•
Wiring
•
Acquisition of the feedback system
•
Configuration (motor type, mass inertia, path/
motor revolution)
•
...
no
Smooth, stable behavior?
Reduce stiffness (Obj. 2100.2) gradually by up to 80%.
Store into flash with Write Flash (WF)
yes
no
Optimization of the error and
setpoint behavior
Optimization of the
respon se behavior
See chapter
“Controller optimization direct drive”
yes
Is a LCB actuator used?
Energize
see chapter
“stability , attenuation”
Smooth, stable behavior
no
yes
yes
Optimizing the stiffness:
1. Standstill
•
Increase stiffness until drive hums, then reduce by
20%
2. Move slowly over the the positioning range
•
Increase stiffness until drive hums, then reduce by
10%
3. Move quickly (e.g. operating speed) over the
positioning range
•
Check behavior and reduce stiffness further if
necessary
Further optimization necessary?
See chapter “oscillating plants”
no
Is the controlled system a direct drive?
(Torque motor, linear motor, PowerRod)
yes
yes
no
no
See chapter
“Controller optimization standard”
Default:
1. Switch on advanced mode
2. Set
bandwidth of current control to30%
3. Set
stiffness to 70%
4. Set
control signal filter to3000µs
(only if no gear is present)
5. Activate VP and switch to standard
Standard
Standard
Advanced
Configuration of the application
Flash is a failure-save emory
Standard