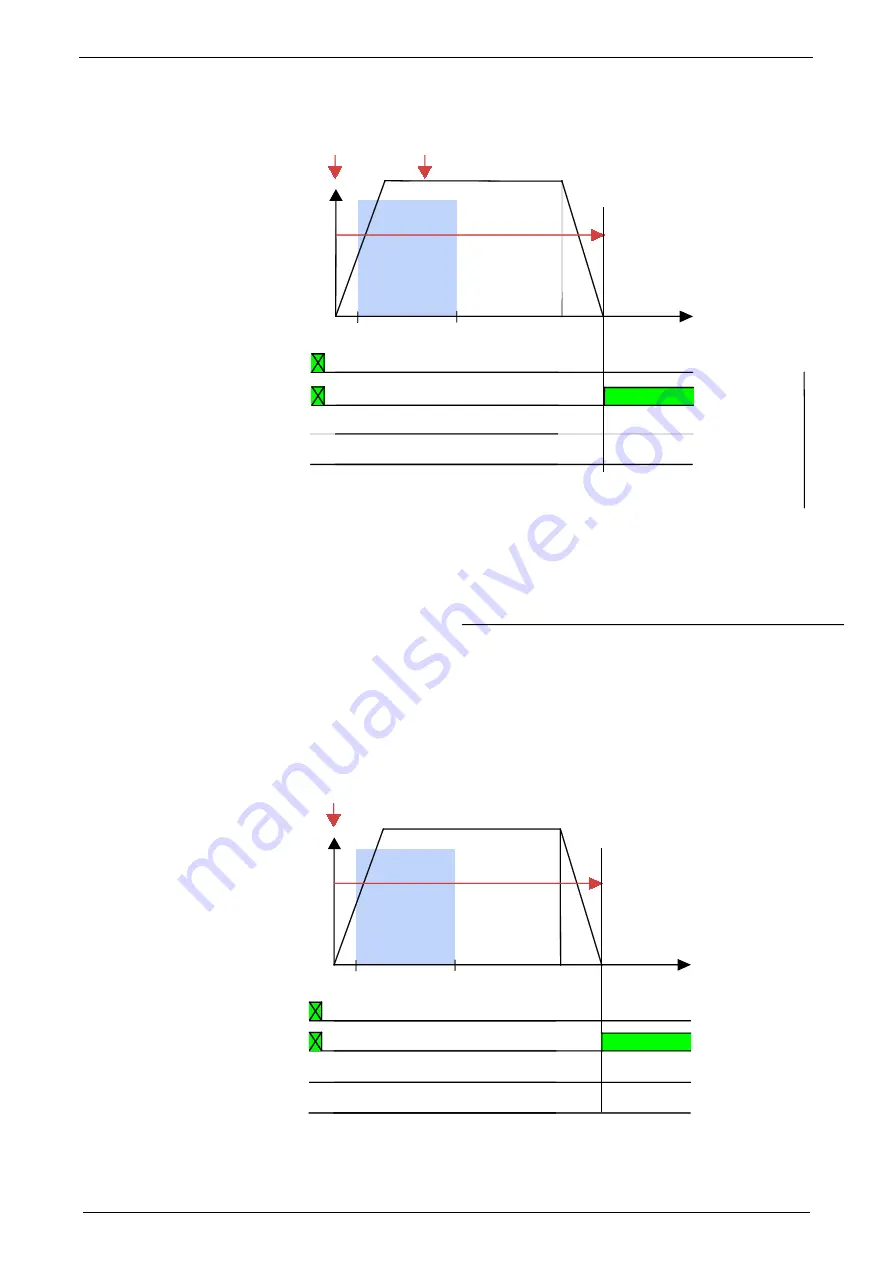
Parker EME
Setting up Compax3
192-120103 N13 C3I20T11 / C3I32T11 December 2010
145
Example 2: Reg within the reg restriction window
v
t
Reg
RegSearch
StartIgnore
StopIgnore
Start
1
2
Regf
POS
Start
Start signal for reg positioning (Control word 1 Bit 6)
RegSearch:
Positioning for reg search
RegMove:
Positioning according to reg
StartIgnore:
Reg ignore window:
(see on page 141) Beginning of the ignore zone
StopIgnore:
Reg ignore window: End of the ignore zone
Reg:
Reg signal (I4 on X12/10)
Regf:
Signal: Reg detected
(Status word 1 Bit 15)
POS:
Signal: Position reached
(Output O1: X12/3 or status word 1 Bit 10)
1
Programmable status bits of RegSearch (only for positioning with set selection)
2
Programmable status bits of RegMove (only for positioning with set selection)
The reg is ignored; the drive moves to the target position from the RegSearch
motion set.
Example 3: Reg is missing or comes after termination of the
RegSearch motion set
v
t
RegSearch
StartIgnore
StopIgnore
Start
1
2
Regf
POS