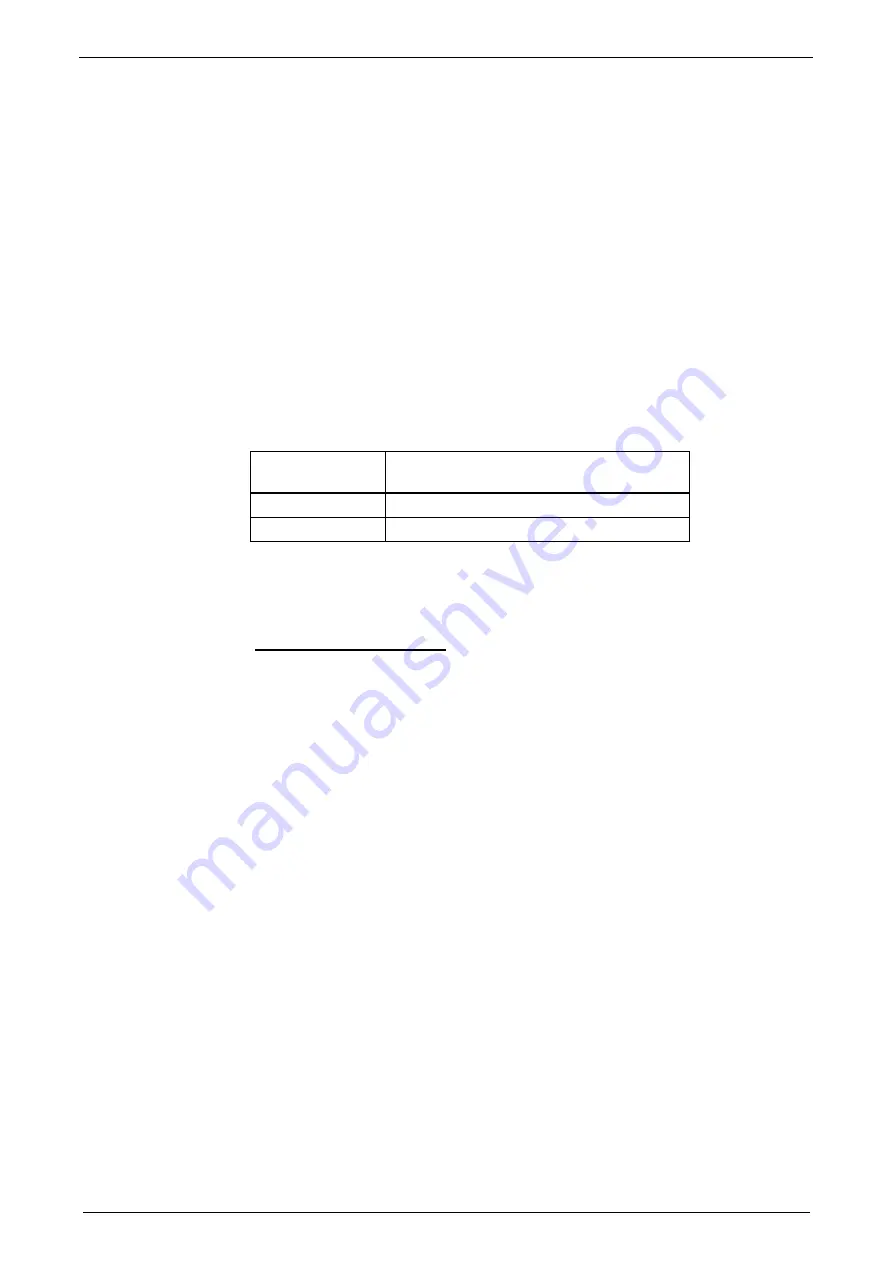
Parker EME
Compax3 device description
192-120103 N13 C3I20T11 / C3I32T11 December 2010
91
Instead of the safety switching device manufactured by Sick mentioned above, you
may use other safety switching devices.
The safety switching device must however provide the following features:
1 normally open contact is required for switching off channel 1
(as an alternative, a safe semiconductor output is possible)
1 off-delayed normally open safety contact is required for switching off channel 2
(as an alternative, a safe semiconductor output with adjustable delay time for the
high_to_low_edge is possible).
1 one-channel monitoring circuit where the feedback contacts of channels 1 and
2 can be integrated for simultaneous monitoring, is required.
At the same time it must be possible to integrate a one-channel start button for
activation of the safety switching device into the circuit.
A new start may only be successful, if it is ensured, that channels 1 and 2 are
switched off.
1 two-channel connection for emergency power off and/or safety door contacts
with cross fault monitoring is required.
The safety switching device must feature performance PL e. The I/Os must at
least correspond to category 3.
Switches and buttons:
1 N/C (S4, S5) per
device:
Guide Device to a currentless state
S6:
closed when the safety door is closed
S2:
Activate safety switching device
Module UET410-MU3T5 modulates regularly test switching signals (OSSD) on
outputs Q3 and Q4.
We recommend to use a filter > 3 ms for signal Q3 in the PLC.
Safe torque off description
Basic functions:
Compax3 devices disabled by:
Channel 1: Energize deactivated by PLC and safety switching device output Q3.
Channel 2: Enable input to “0” by safety switching device output Q4.
Activate safety switching device
Before the Compax3 can be placed into operation, the safety switching device
must be activated by a pulse to Input S2.
Prerequisite:
S2 closed
Safety door closed: only then the safety door monitor will enable the safety
switching device on two channels
Feedback activated via PLC (Controller feedback channel 1: motor not energized)
The feedback contact of all Compax3 devices must be closed (channel 2).
Energize Compax3 (Motor and power output stage)
The PLC enables the Compax3 devices by means of the control word and the
safety switching device enables the Compax3 devices by means of the Enable
input. (If an error is still present on the Compax3, it must be acknowledged
before)
The motors are energized with current.
Summary: Compax3 is only energized if the feedback functions are capable of
functioning via two channels.
Caution!