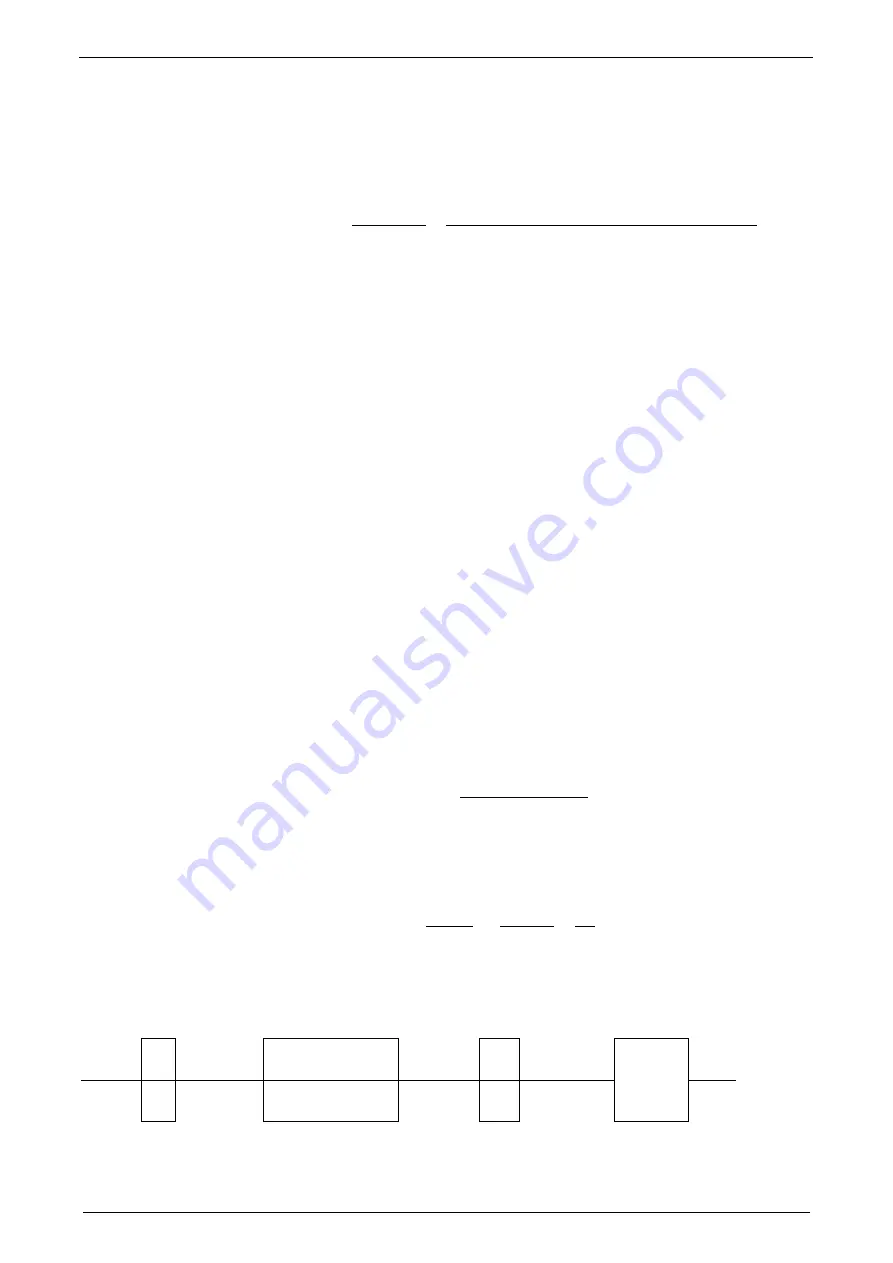
Parker EME
Setting up Compax3
192-120103 N13 C3I20T11 / C3I32T11 December 2010
153
The reference to the master axis is established via the increments per revolution
and the travel path per revolution of the master axis (corresponds to the
circumference of the measuring wheel).
That is:
MasterPos =
Master_I
*
Travel Distance per Master Axis revolution
(M_Units/rev)
(1)
I_M
Travel Distance per Master Axis revolution -
Denominator
MasterPos: Master Position
Master_I: master increments read in
I_M: Increments per revolution of the master axis
Encoder with 1024 increments per master revolution and a circumference of the
measuring wheel of 40mm.
Travel path per revolution of the master axis numerator = 40
Travel path per revolution of the master axis denominator = 1
Increments per revolution of the master axis = 1024
Reference system of Slave axis: Unit of measure [mm]
Travel path per revolution numerator = 1
Travel path per revolution denominator = 1
Gearing numerator = 2
Gearing denominator = 1
This results in the following interrelations:
If the measuring wheel moves by 40mm (1 master revolution), the slave axis will
move by 80mm.
Slave unit = MasterPos *
Gearing
numerator
(2)
Gearing
denominator
(1) set into (2) and with numerical values results with 1024 increments read in (=1
Master revolution):
Slave unit = 1024 *
1
*
40mm
*
2
= 80mm
1024
1
1
Master - Position = +40mm => Slave - Position = +80mm
Structure:
Master Z1 MasterPos Gearing
numerator
Slave -
N2
Slave_U
Gearbox
Load
N1
Gearing
denominator
Units
Z2
to motor
Reference to master
axis
External signal
source
Settings:
Configuration
wizard:
Gearing: