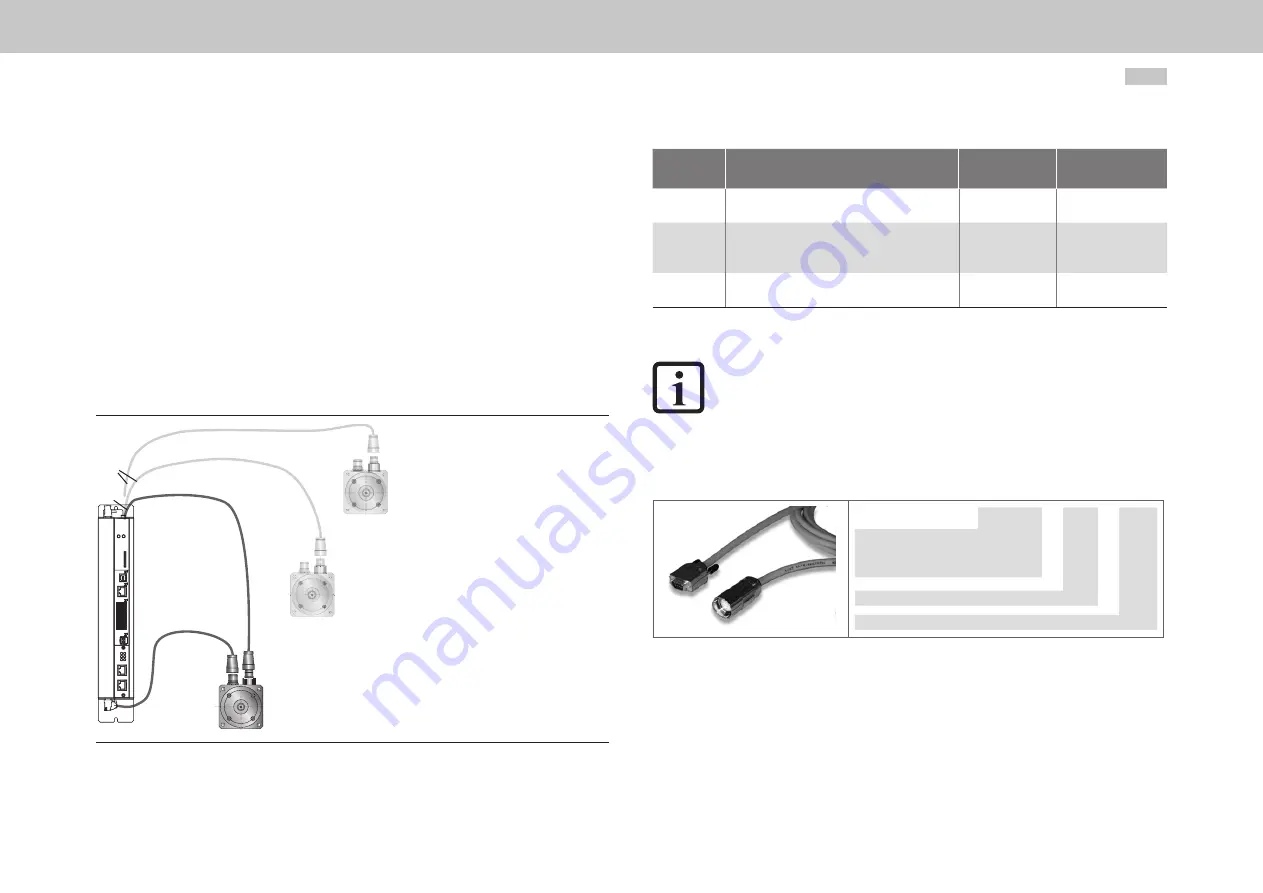
46
MSD Multi-Axis System Operation Manual DC-AC Servo Drive
Motor (with encoder installed)
Encoder cable
Connection on the
DC-AC Servo Drive
Variant A
With resolver
without further options
C08335-013-yyy
X6
Variant B
Sin/Cos multi-turn encoder
with SSI/EnDat interface
CA58876-002-yyy
X7
Variant C
Sin/Cos multi-turn encoder
with HIPERFACE® interface
CA58877-002-yyy
X7
Table 4.10 Variants of motors, encoder type and encoder cable
NOTE:
Do not cut the encoder cable, for example to route the signals via terminals in
the switch cabinet. The knurled screws on the D-Sub connector housing must
be tightly locked!
4.13.3 Ready made encoder cables
The speci
fi
cations can only be assured when using the Moog system cables.
CO8335
-
013
-
yyy
Encoder cable
Ready made-up cable
Resolver cable
Encoder cable SSI, EnDat
CA58876
Encoder cable Hiperface
®
CA58877
002
002
Encoder system
Version
Cable length (m)
1) yyy stands for length in meters; standard length: 1 m (3.28 ft), 5 m (16.40 ft), 10 m (32.80 ft), 15 m (49 ft), 20 m (65 ft), 50 m
(164 ft). Further length on request
Encoder cable CO8335-013-yyy
1)
Order code
4.13 Encoder connection
All encoder connections are located on the top of the unit.
4.13.1 Encoder connection for synchonous motors
Please use the ready made motor and encoder cables from Moog to connect the
synchronous motors.
4.13.2 Allocation of motor/encoder cable to the DC-AC Servo
Drive
Compare the rating plates of the components. Make absolutely sure you are using the
correct components according to variant A, B or C!
Resolver
high-resolution encoder with HIPERFACE® interface
high-resolution encoder with SSI-/EnDat interface
Variant
A
Variante
B
Variant
C
X7 (optional X8 )
X6
Figure 4.18 Motor/encoder cable assignment
moog
Id. no.: CA97554-001 0
5
/2017
4 Electrical installation