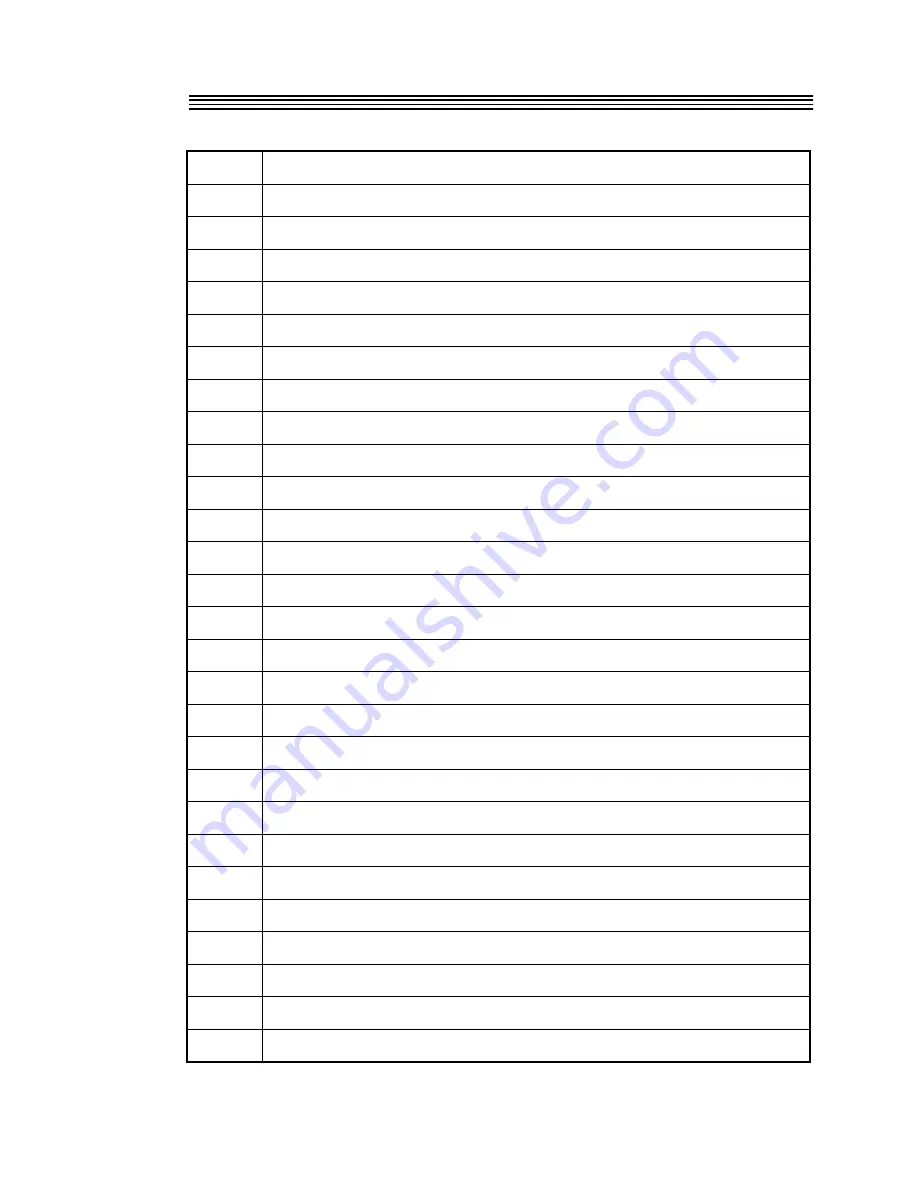
Checklists and Logs
Appendix D
Check movement of center tube (so it doesn’t rub).
Remove cable tie and foam or rubber shim.
Recheck center tube for free movement.
Make sure test mass is centered in cage and wires do not rub.
Replace spring assembly in service ring (don’t tighten screws).
Replace travel lock assembly.
Rotate main spring assembly to equalize travel lock fork clearance.
Tighten screws holding spring assembly to service ring.
Install electrical feedthrough.
Connect all wires (match color coding).
Place Superspring on leveling table.
Adjust table to center test mass in cage.
Make sure top of test mass is about 1.5 mm below cage assembly.
Connect Superspring controller to Superspring.
Drive zero-positioning motor (ZPM) until sphere voltage is zero.
9-23
Summary of Contents for Micro-g LaCoste FG5
Page 7: ...Table of Figures This Page is Intentionally Blank vii ...
Page 8: ......
Page 13: ...Design Components and Function 2 Figure 2 3 Side view of the dropping chamber 2 3 ...
Page 23: ...Design Components and Function 2 Figure 2 9 The Superspring 2 13 ...
Page 31: ...Design Components and Function 2 Figure 2 12 Rotation Monitor 2 21 ...
Page 32: ...Design Components and Function 2 This Page is Intentionally Blank 2 22 ...
Page 36: ...How to Set Up and Run the FG5 3 Figure 3 1 Superspring Interferometer Setup 3 4 ...
Page 56: ......
Page 59: ...Adjustment and Maintenance 4 4 3 ...
Page 78: ...Adjustment and Maintenance 4 4 22 ...
Page 106: ......
Page 138: ...Checklists and Logs Appendix D Measure gap between two levers near ZPM 9 24 ...
Page 143: ...Checklists and Logs Appendix D This Page is Intentionally Blank 9 29 ...
Page 144: ......