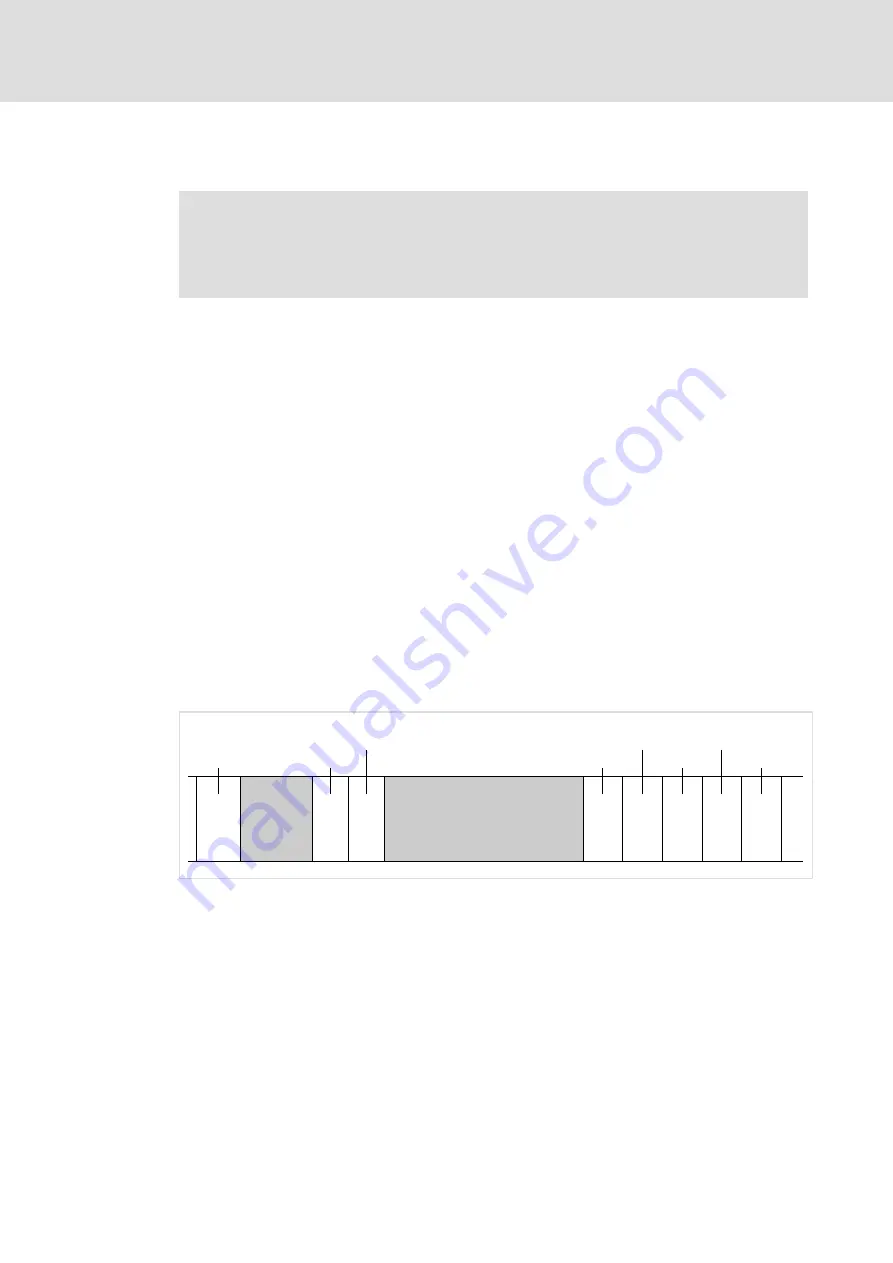
Appendix
Communication with MotionBus/system bus (CAN)
Structure of the CAN data telegram
442
EDBCSXS064 EN 4.0
13.4
Communication with MotionBus/system bus (CAN)
Note!
In case of ECSxS... axis modules
only the parameter data channels (SDO) are supported for the system bus
(CAN) ˘ interface X14 (CAN−AUX).
For communication between the components of the drive system the axis modules
ECSxS... have two CAN interfaces:
ƒ
Interface X4 ("CAN")
– MotionBus (CAN)
– For communication with a higher−level host system (PLC) or further controllers
– The data is exchanged via process data channels and parameter data channels.
– Parameter setting/diagnostics via code range
C03xx
ƒ
Interface X14 ("CAN−AUX")
– System bus (CAN)
– PC interface/HMI for parameter setting and diagnostics
– Interface to a decentralised I/O system
– The data is exchanged via parameter data channels only.
– Parameter setting/diagnostics via code range
C24xx
The communication is effected via data telegrams.
13.4.1
Structure of the CAN data telegram
Control field
CRC delimit.
ACK delimit.
Start
RTR bit
CRC sequence
ACK slot
End
Identifier
User data
(0 ... 8 bytes)
l
Network management
l
Process data
l
Parameter data
1 bit
11 bits
1 bit
6 bits
15 bits
1 bit
1 bit
1 bit
7 bits
Fig. 13−1
Basic structure of the CAN telegram
Identifier
The identifier determines the priority of the message. Moreover, the following is coded:
ƒ
The CAN node address (device address in the CAN network) of the node which is to
receive the CAN telegram.
See also chapter "Addressing of the parameter and process data objects" (
ƒ
The type of user data to be transferred