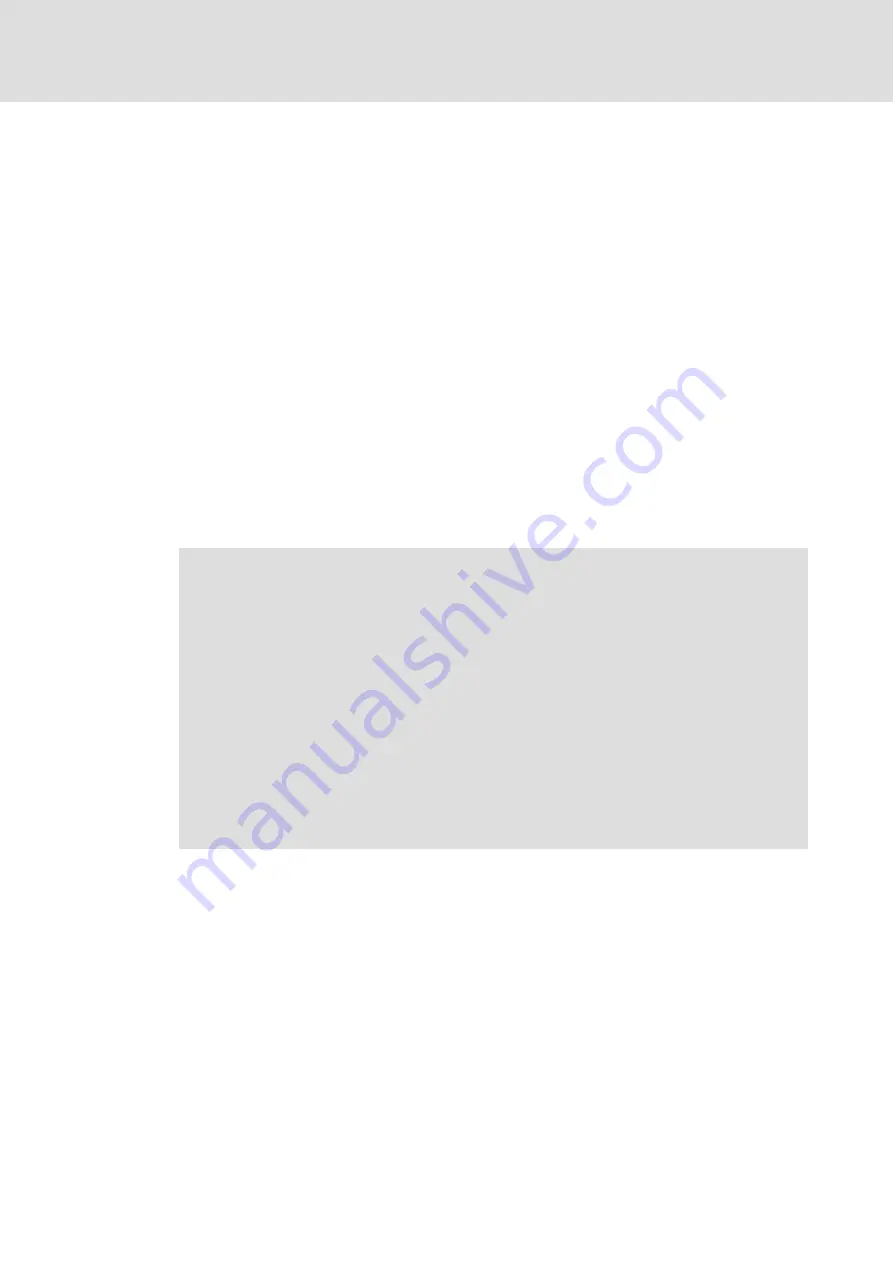
Commissioning
Operation with motors from other manufacturers
Effecting rotor position adjustment
152
EDBCSXS064 EN 4.0
Setting sequence
1. Inhibit controller. (
– Press the <F9> key in GDC.
– Green LED is blinking, red LED is off
2. Unload motor mechanically.
– Separate the motor from the gearbox or machine so that it can rotate freely.
3. Open holding brake (if available).
4. Activate rotor position adjustment with C0095 = 1.
5. Enable controller. (
– X6/SI1 = HIGH and X6/SI2 = HIGH and press the <F8> key in GDC.
The rotor position adjustment program of the controller is started:
– The rotor rotates half a revolution in 16 steps (for resolver with 1 pole pair:
180° electrically
¢
180° mechanically).
– After one revolution, C0095 is automatically reset to "0".
– The rotor zero phase is stored under C0058. (For absolute value encoders
(Hiperface®, single−turn/multi−turn) at X8, C0058 is always "0".)
Danger!
Uncontrolled drive movements after an Sd7 fault with absolute value
encoders
If absolute value encoders are used and the rotor position adjustment is
completed with the fault message "Sd7" (
238), the rotor position could not
be assigned to the feedback system. In this case, the drive may carry out
uncontrolled movements after controller enable.
Possible consequences:
ƒ
Death or severe injuries
ƒ
The machine/drive may be destroyed or damaged
Protective measures:
ƒ
Repeat rotor position adjustment (starting with step 1).
ƒ
Check wiring and interference immunity of the encoder at X8.
6. Inhibit controller. (
– Press the <F9> key in GDC.
– Green LED is blinking, red LED is off
7. Save the data determined by the controller with C0003 = 1.
Tip!
The values for C0058 and C0095 are only displayed in GDC if you place the bar
cursor on them and read back the code using function key <F6>.