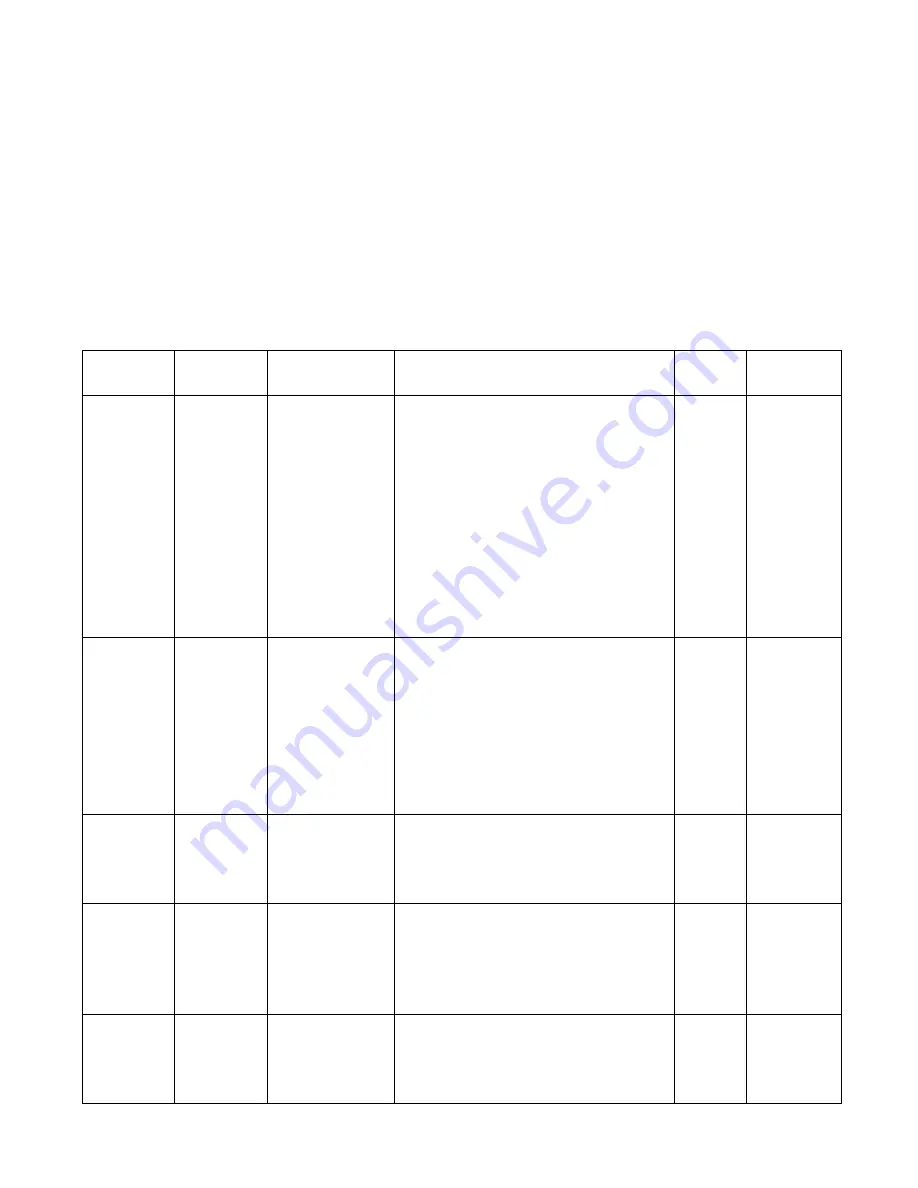
25
5.2 Description of Parameters
Group F000 represents an instruction group, and the parameters in this group cannot be saved.
The address d4.00 is used to save the motor parameters set for Group F004. Note that this group of
parameters must be set when customers choose third-party motors, but these parameters need not to be set for
the motors delivered and configured by our company. d2.00, d3.00 and d.5.00 represent the same address, and
are used to save all setup parameters except those of motors (Group F001/F002/F003/F004/F005). Three
numeric objects (d2.00/d3.00/d5.00) are developed to facilitate customers.
Parameter List: Group F000 (To Set Driver Instructions)
Numeric
Display
Internal
Address
Variable Name
Meaning
Default
Value
Range
d0.00
60600008
Operation_Mode 0.004 (-4): Pulse control mode, including
pulse direction (P/D) and double pulse
(CW/CCW)
modes.
0.003
(-3):
instantaneous speed mode
0001 (1): Internal position control mode
0003
(3):
Speed
mode
with
acceleration/deceleration
0004 (4): Torque mode
Note: Only applied in the working mode
where no external signals control the
driver.
-4
N/A
d0.01
2FF00508
Control_Word_E
asy
000.0: Releases the motor
000.1: Locks the motor
001.0: Clears errors
Note: Only applied in the situation where
enabling a driver or wrong resetting is
not controlled by external signals. After
the wrong reset of the driver, the motor
must be enabled again.
0
N/A
d0.02
2FF00910
SpeedDemand_
RPM
Sets the motor’s target rotation speed
when the driver works in the ―-3‖ or ―3‖
mode and the address d3.28 is set to 0
(without external analog control).
0
N/A
d0.03
60710010
CMD_q
Sets input torque instructions (current
instructions) when the driver works in
the ―4‖ mode and the address d3.30 is
set to 0 (without external analog
control).
0
-2047~2047
d0.04
2FF00A10
Vc_Loop_BW
Sets the velocity loop bandwidth. The
unit is Hz.
This variable can only be set after auto
tuning is performed properly; otherwise
0
0~600
Summary of Contents for CD420
Page 8: ...8 1 3 3 Power Brake and Encoder cable of Motors...
Page 22: ...22 Fig 4 3 Separate regulation of bits...
Page 78: ...78...
Page 99: ...99 Chapter 11 Specification 11 1 Servo Drivers and Motors Selection Table...
Page 100: ...100 11 2 Servo Driver 11 2 1 Technical Specification Table for Servo Driver...
Page 101: ...101 11 2 2 Mechanical Dimension Diagram for Servo Driver...
Page 103: ...103 11 3 2 SMH80 Servo Motor...
Page 104: ...104 11 3 3 SMH110 Servo Motor 1 Technical Specification Table...
Page 105: ...105 2 Dimension Torque Curve...
Page 106: ...106 11 4 Wiring Diagram for Servo Motor Cable 11 4 1 Wiring Diagram for the Power Cable...
Page 107: ...107 11 4 2 Wiring Diagram for the Encoder Cable...