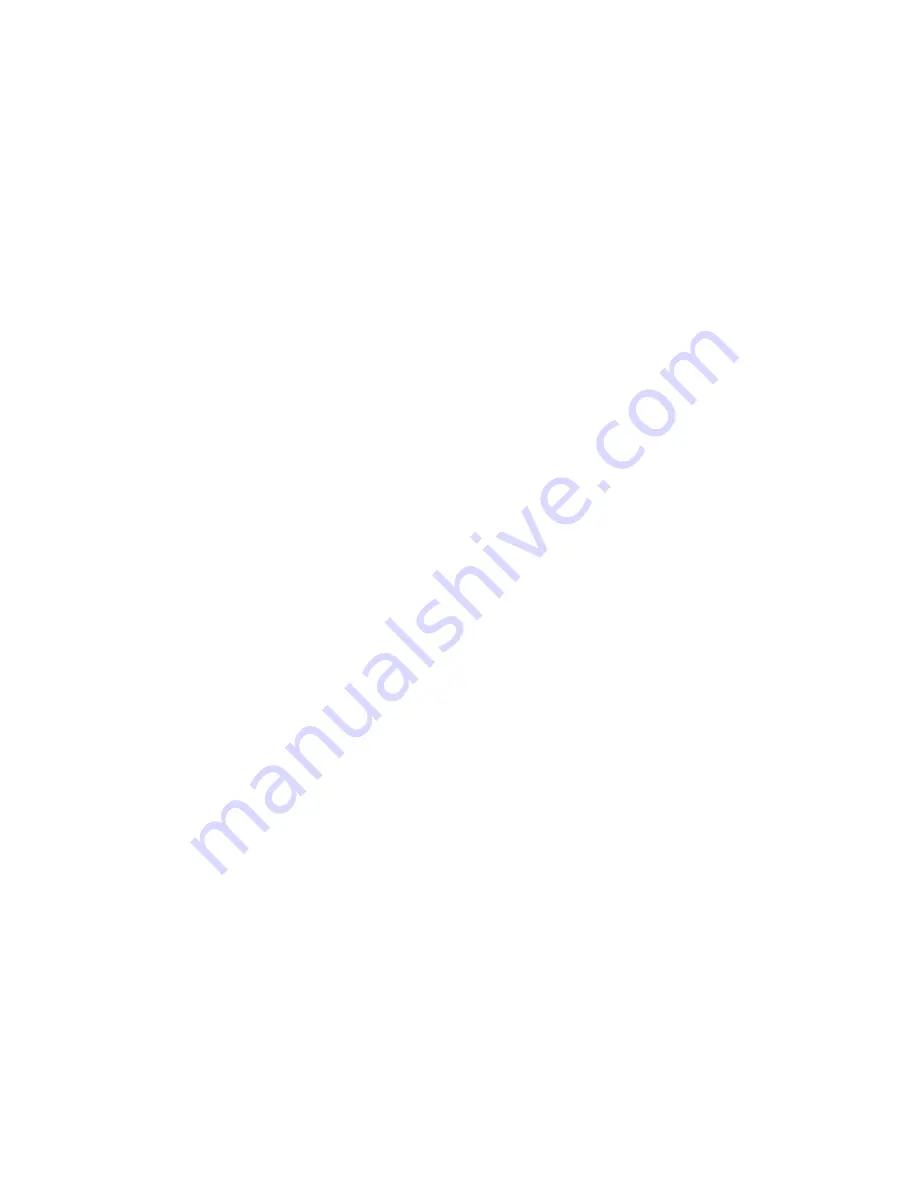
92
feedback filter parameter) values of the velocity loop to prevent visible oscillations when the system
works in the speed mode. If necessary, adjust the data of d2.03 notch filter to inhibit resonance.
4. The time for different load tuning varies, and generally a few seconds is required. The auto tuning time
can be reduced by presetting the K_Load value to a predicted value that is close to the actual value.
5. Vc_Loop_BW can be written only after successful auto tuning, otherwise the driver may work improperly.
After you write the desired bandwidth of the velocity loop in Vc_Loop_BW, the driver automatically
calculates the corresponding values of Kvp, Kvi and Speed_Fb_N. If you are dissatisfied with low-speed
smoothness, you can manually adjust Kvi. Note that auto tuning does not automatically adjust the data of
a notch filter.
In the following circumstances, auto tuning parameters should be adjusted:
1. When the friction in a rotation circle of the motor is uneven, it is required to increase the amplitude of
d2.21 sine wave to reduce the impacts caused by uneven friction. Note that d2.21 increases when
the oscillation amplitude of the loadings increase.
2. If auto tuning lasts for a long time, initial evaluation of the total inertia is available. It is recommended
to set K_Load to an evaluation value before auto tuning.
3. If auto tuning is unstable, the stability of auto tuning increases when d2.22 increases properly, but
the time for auto tuning slightly increases.
In the following conditions, auto adjustment goes wrong. In this case, you can only set parameters manually:
1. The load inertia is featured by great fluctuation.
2. Mechanical connection rigidity is low.
3. Clearances exist in the connection between mechanical elements.
4. The load inertia is too great, while Kvp values are set too low.
5. If the load inertia is too great, K_Load data will be less than 20; if the load inertia is too little, K_Load
data will be greater than 15000.
Operational steps:
1. Step 1: Press
MODE
to enter Group F002. Select the object addresses ―d2.01‖, ―d2.02‖ and ―d2.05‖
respectively for initial settings, so that no obvious oscillation occurs when the system works in the speed
mode.
2. Step 2: Press
MODE
to enter Group F000. Select the object address ―d0.06‖, set the address to 11, and
auto tuning starts.
3. Step 3: Press
MODE
to enter the parameter display status. During auto tuning, the content of numeric
display is K_Load data in real time. Step 4: When K_Load data becomes stable, auto tuning is completed,
and the value of ―d0.06‖ is automatically changed to 0.
4. Step 5: You need to customize the required bandwidth of the velocity loop Vc_Loop_BW. In this case, it is
recommended to increase the bandwidth gradually, until the machine works in the optimum state. Finally,
run the test system in the actual environment and save the parameters.
8.2 Oscillation Inhibition
If resonance occurs during machine operation, you can adjust a notch filter to inhibit resonance. If
resonance frequency is known, you can directly set Notch_N to (BW-100)/10. Note that you need to set
Notch_On to 1 to enable the notch filter. If you do not know exactly the resonance frequency, you can firstly
set the max value of d2.14 current instruction to a low one, so that the oscillation amplitude is within the
acceptable range; then try to adjust Notch_N to check whether resonance disappears.
If machine resonance occurs, you can calculate the resonance frequency by observing the waveform of
the target current with the oscilloscope function of the driver.
Summary of Contents for CD420
Page 8: ...8 1 3 3 Power Brake and Encoder cable of Motors...
Page 22: ...22 Fig 4 3 Separate regulation of bits...
Page 78: ...78...
Page 99: ...99 Chapter 11 Specification 11 1 Servo Drivers and Motors Selection Table...
Page 100: ...100 11 2 Servo Driver 11 2 1 Technical Specification Table for Servo Driver...
Page 101: ...101 11 2 2 Mechanical Dimension Diagram for Servo Driver...
Page 103: ...103 11 3 2 SMH80 Servo Motor...
Page 104: ...104 11 3 3 SMH110 Servo Motor 1 Technical Specification Table...
Page 105: ...105 2 Dimension Torque Curve...
Page 106: ...106 11 4 Wiring Diagram for Servo Motor Cable 11 4 1 Wiring Diagram for the Power Cable...
Page 107: ...107 11 4 2 Wiring Diagram for the Encoder Cable...