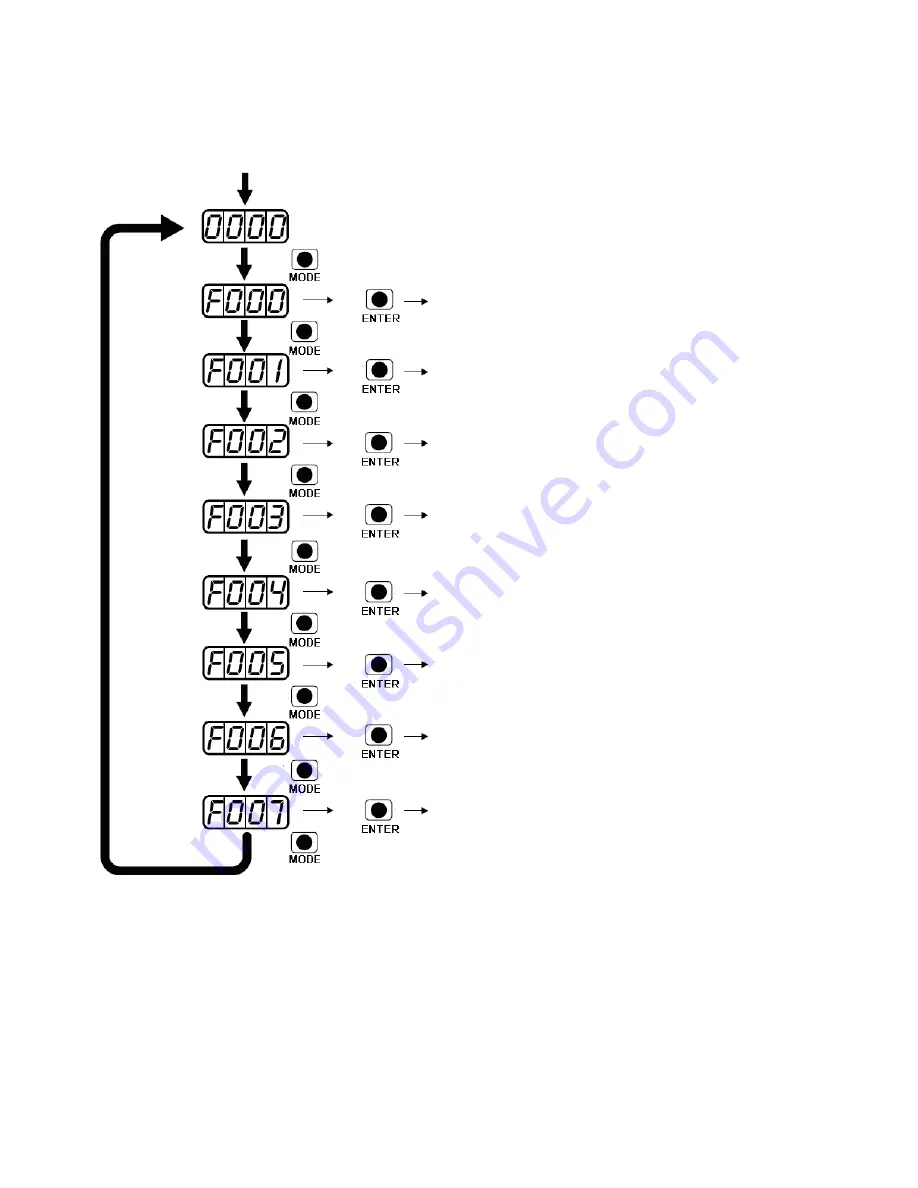
20
4.2 Operation on Digital Operation Panel
Power ON
Press
MODE
Switching of basic menus
Parameter display (current speed is
displayed by default)
Press
Press
Press
Press
Press
Press
Press
Press
Press
Press
Press
Press
Press
Press
Press
Press
Press
Set driver instructions
Set real-time display of data
Set control loop parameters
Settings
I/O parameters
Mode operation parameters
Set motor parameters
Set driver parameters
Trial operation
Check wrong history records
L
o
o
p
Fig. 4-1 Operation on a digital operation panel
Note:
If a non real-time display interface is displayed for the control panel, and no key operation occurs, the
real-time display interface is automatically skipped after 20 seconds to avoid misoperation.
Example 4-1: Set the denominator of electronic gear ratio to 10000 with
number system switching
1.
Press
MODE
. The main menu is displayed. Choose
F003
.
Summary of Contents for CD420
Page 8: ...8 1 3 3 Power Brake and Encoder cable of Motors...
Page 22: ...22 Fig 4 3 Separate regulation of bits...
Page 78: ...78...
Page 99: ...99 Chapter 11 Specification 11 1 Servo Drivers and Motors Selection Table...
Page 100: ...100 11 2 Servo Driver 11 2 1 Technical Specification Table for Servo Driver...
Page 101: ...101 11 2 2 Mechanical Dimension Diagram for Servo Driver...
Page 103: ...103 11 3 2 SMH80 Servo Motor...
Page 104: ...104 11 3 3 SMH110 Servo Motor 1 Technical Specification Table...
Page 105: ...105 2 Dimension Torque Curve...
Page 106: ...106 11 4 Wiring Diagram for Servo Motor Cable 11 4 1 Wiring Diagram for the Power Cable...
Page 107: ...107 11 4 2 Wiring Diagram for the Encoder Cable...