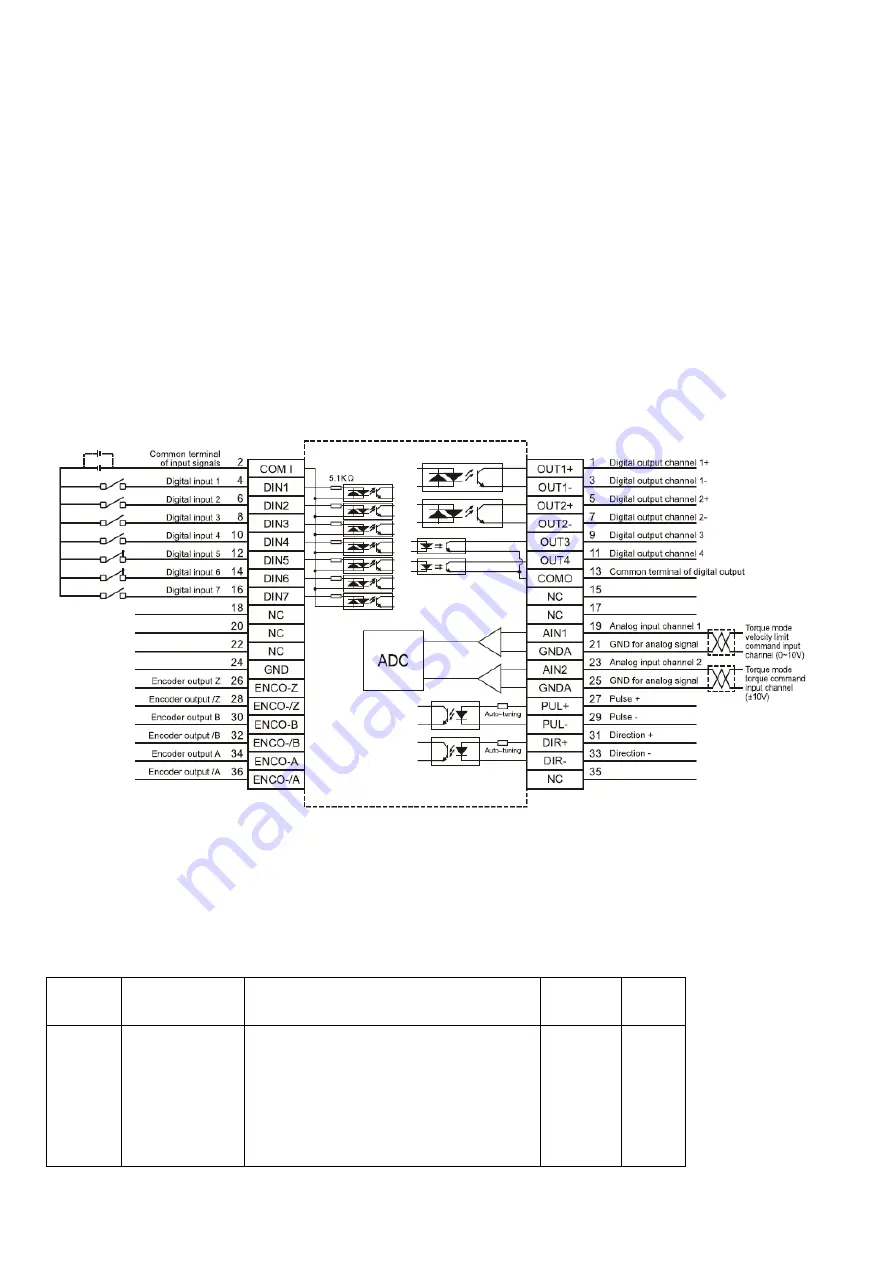
68
being powered on. In this case, the numeric display has limit status display. If limit switches are unavailable,
please disable the function of limit switches by referring to Example 6-4.
Step 3: Confirm the mode switching positions and operation modes by referring to the settings in Example 6-5.
The factory default settings are as follows: When no signal is inputted to DIN3, the dri
ver operates in the ―-4‖
mode (d3.16 = -
4); when signal is inputted to DIN3, the driver operates in the ―-3‖ mode (d3.17 = -3). If the
driver is required to operate in the speed mode after being powered on, set d3.16 to -3 or 3.
Step 4: After configuring functions on digital input ports, select the analog
– speed channel, and set
parameters such as analog
– speed factors, dead zone, offset and filtering.
Step 5: Save parameters.
7.3 Torque Mode (“4” Mode)
7.3.1 Wiring in Analog
– Torque Mode
Fig. 7-13 Wiring diagram of
CD2S
Servo in analog
– torque mode
7.3.2 Parameters for Analog
– Torque Mode
Table 7-16 Parameters for analog
– torque mode
Numeric
Display
Variable Name
Meaning
Default
Value
Range
d3.22
Analog1_Filter
Used to smooth the input analog
signals.
Filter frequency: f=4000/(2π*
Analog1_Filter)
Time Constant: τ = Analog1_Filter/4000
(S)
5
1~127
Summary of Contents for CD2S Series
Page 7: ...7...
Page 8: ...8 1 3 3 Power Brake and Encoder cable of Motors...
Page 12: ...12 Fig 2 3 Installation direction...
Page 15: ...15 3 1 2 Wiring Diagram Fig 3 1 Wiring diagram of CD2S driver...
Page 23: ...23 Fig 4 3 Separate regulation of bits...
Page 82: ...82...
Page 96: ...96 8 4 Debugging example 8 4 1 Oscilloscope 1 Enter oscilloscope 2 Parameters for Oscilloscope...
Page 98: ...98 In Auto Reverse mode Kvp 110...
Page 100: ...100 The oscilloscope is as following max following error is 69 inc Fig 2 Kpp 30 Vff 100...
Page 101: ...101 The oscilloscope is as following max following error is 53 inc Fig 3 Kpp 30 Vff 50...
Page 102: ...102 The oscilloscope is as following max following error is 230 inc...