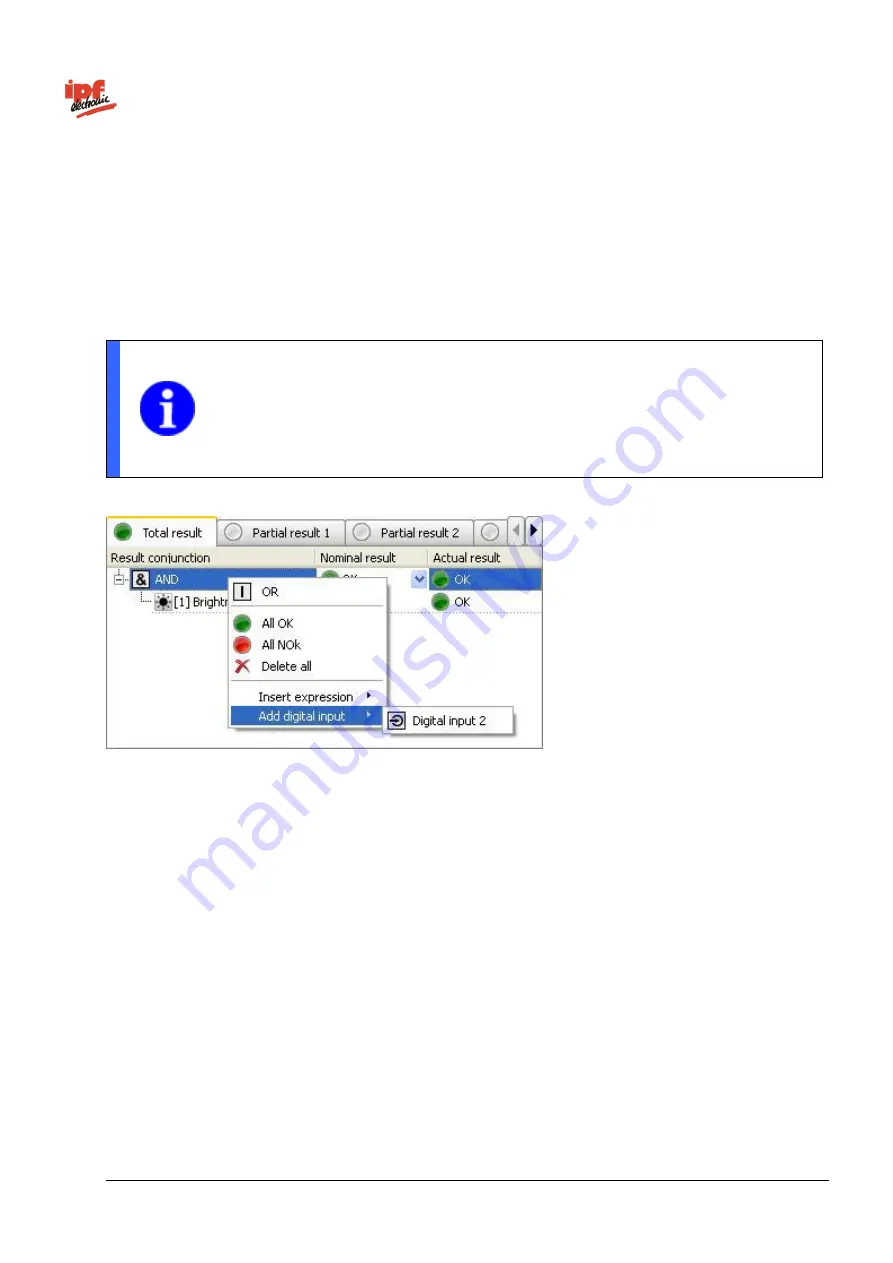
Technical Documentation
opti-check
v2.8.2-K11
58/332
ipf electronic GmbH
Lüdenscheid, Germany
Digital inputs in results conjunction
(device dependant)
You can also include the states of the digital inputs in the total result. They can be nested just like the other
feature checks.
The states of the digital inputs are captured at the trigger point or at the start of image acquisition.
The states of the digital inputs alone cannot be linked; there must be at least one feature check!
NOTE
To use the digital inputs in the result conjunction, you must select the relevant
External
Sensor
input in the device settings.
Device → Device Settings → Digital I/Os