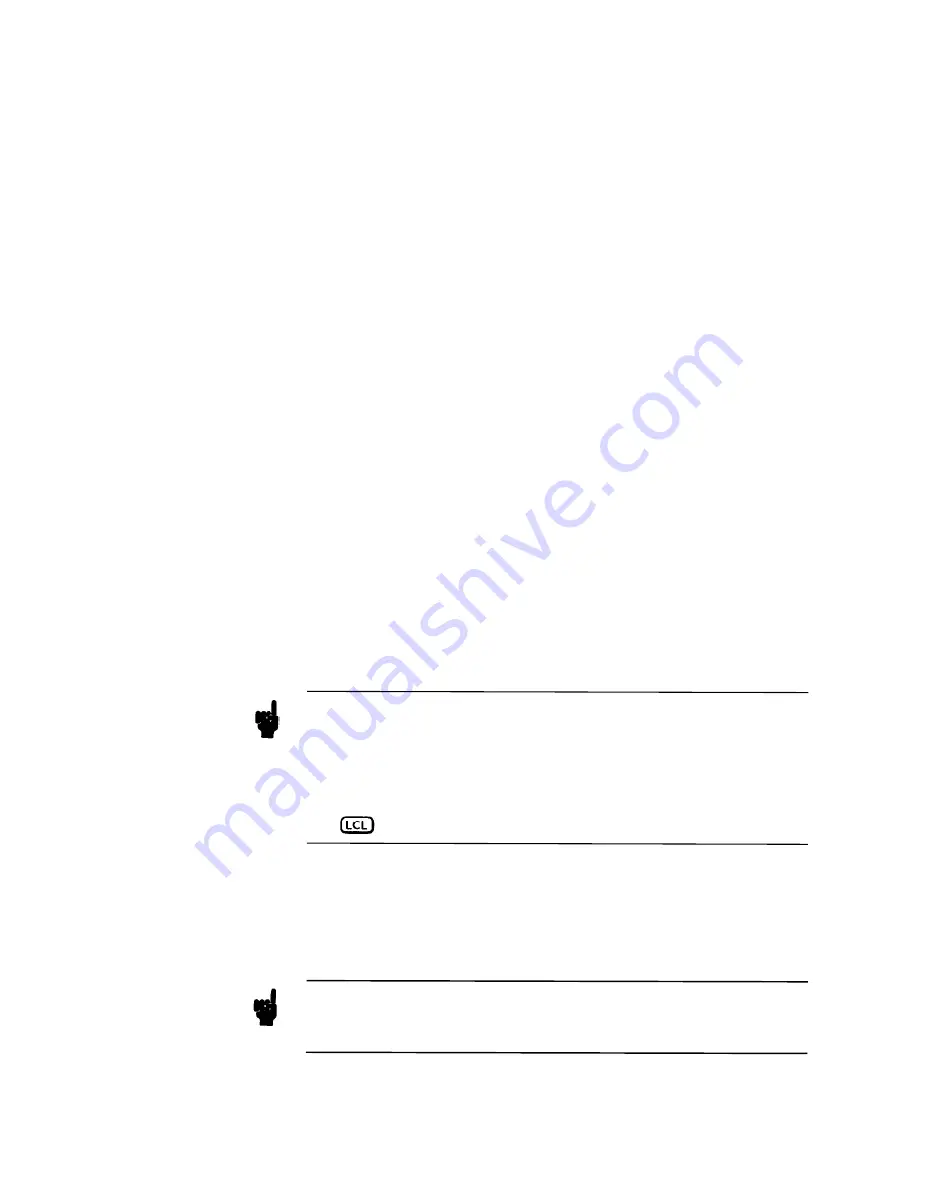
Note
Duty Cycle Error
(Bit 4)
Note
6-16
Programming
•
No valid waveform at the output:
a. LEE
>
WID x0.8 or
(PERx DTY /lOO) x0.8
b. TRE
>
(PER-WID) x0.8 or
PER-{PERxDTY /lOO)) x0.8
c. TRE
�
(DBL-WID) x0.8 or
DBL-{PERx DTY /200)) x 0.8
d. TRE
�
(PER-DBL-WID) x0.8 or
PER-DBL-{PERx DTY /200)) x 0.8
•
No calculation with "SRl"
The "EXCESSIVE SLOPE" error message and calculation can be
suppressed with the SRO command. This will reduce programming
time.
Example
OUTPUT 712 ; "SRO "
This is particularly useful for character strings where a multiple of
the same timing parameter is programmed such as
OUTPUT 712 ; 11SR0 11
FOR A
=
1 to 100
OUTPUT 712 ; "PER (CHR$ A) MS "
NEXT A
Immediately upon receiving the new PERIOD value, the HP 81 12A
would calculate the excessive slope error for each period time
interval. By suppressing "EXCESSIVE SLOPE" , new settings for
Period are accepted by the instrument without any calculation, and a
reduction in programming time of typically 30 ms may be achieved.
In the permanently stored Mode/Parameter settings in the
HP 81 12A ROMs, "SR" is set to "O" (zero). If these settings are
recalled
as
current settings, the Service Request function can be
re-activated by programming "SR" to "1".
OUTPUT 712 ; 11SR1 11
The
key re-activates the Excessive Slope Error.
There are three types of error which set the duty cycle error bit
in the status byte. The conditions which cause them and the
description used by the HP 81 12A when replying to an
IERR
command are listed below. The timing error bit is not latched,
therefore a transient error is only recorded by generating an SRQ.
More than one error condition can occur at one time. When using
the
IERR
command ensure that you allow for a reply containing
more than one error description.
Summary of Contents for 8112A
Page 6: ......
Page 24: ......
Page 36: ......
Page 44: ......
Page 70: ......
Page 92: ......
Page 144: ...8 32 Testing Performance ...
Page 176: ......
Page 190: ......
Page 194: ...10 2 4 Servicing the Power Supply ...
Page 196: ......
Page 197: ......
Page 216: ......
Page 240: ...10 4 16 Servicing the Shaper and Output Amplifier ...
Page 242: ...A R l BD RY MR I N 1 2 7 I I IJt 51 CR1 B e i 1 _ _ _ _ 20 ...
Page 244: ......
Page 251: ......
Page 262: ...A B A2 ED RY CONTROL ...
Page 270: ......
Page 290: ...R B c R3 BD RY M I CROPROCESSOR 1 2 3 FIGURE 1 0 7 8 ...
Page 294: ... 8 X2l 2 X2 Figure A 1 Mechanical Parts 1 A 2 Replaceable Parts ...
Page 295: ...MP MP3 MP MP2 MP4 MPS MP 1 2 MPS MP MP I B ElElElEl Replaceable Parts A 3 ...
Page 334: ......
Page 378: ...Figure B 14 Mechanical Parts 1 B 44 Backdating ...
Page 380: ......
Page 382: ......
Page 402: ......