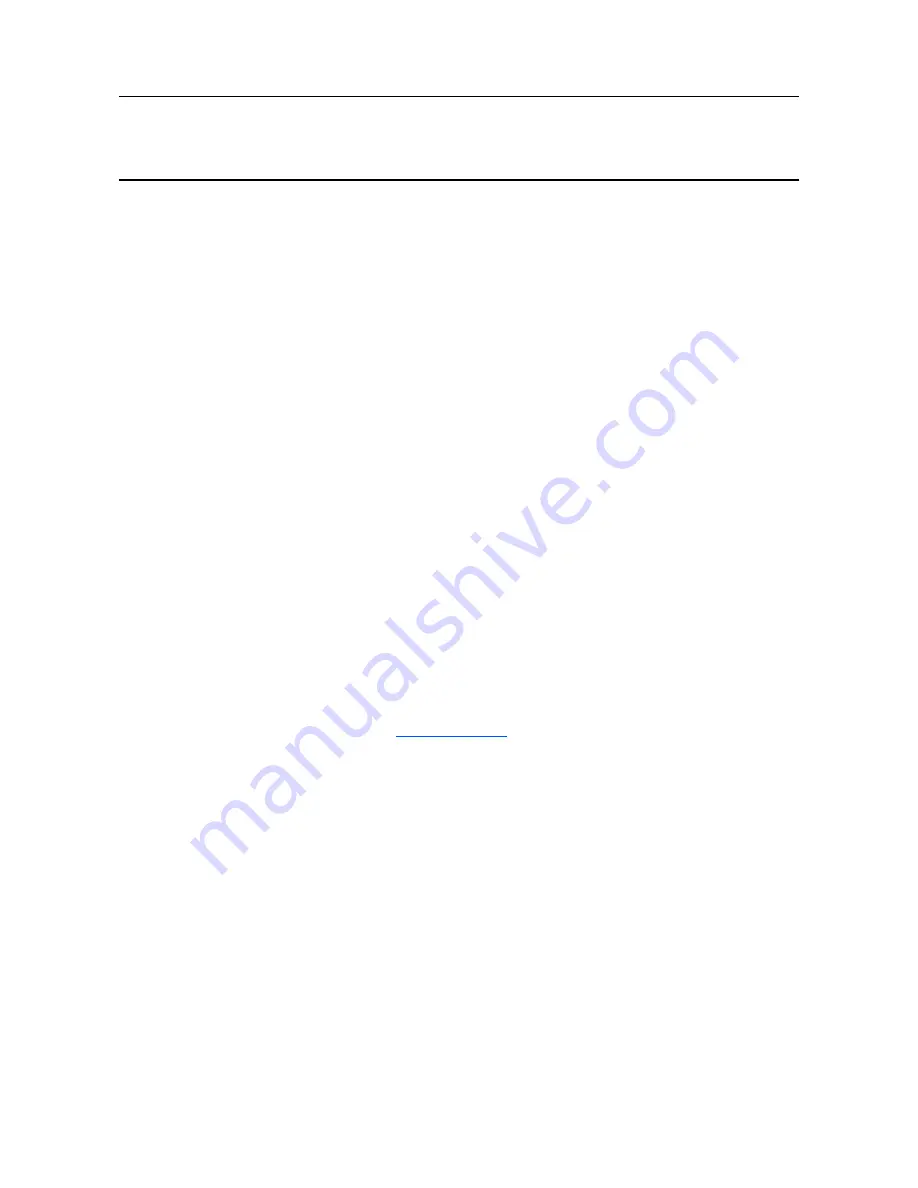
MAN0923_Issue 3_04/15
Touchpoint Pro
Operating Instructions
177
14.1 Introduction
The Touchpoint Pro Modbus Interface provides a facility for digital communication between the
Touchpoint Pro and an external computer system. Modbus is a well supported digital data communication
protocol which provides a set of standard commands by which system data can be communicated.
The principal features of the Modbus Interface are:
•
Operates as a Modbus Remote Terminal Unit (RTU) slave device node
•
Supports functions 02, 03, 04, 06 and 16 of the Modbus protocol
•
Provides sensor gas readings and alarm status for Fault, Inhibit, Warning, A1, A2, A3, STEL, LTEL and
Rate alarms from all input channels in the system
•
Supports commands to Inhibit, Reset and Acknowledge for all channels in the system, as well
as Global Reset and Global Acknowledge
•
Dual RS485 half duplex communication with multi-drop capability
•
Asynchronous serial link configurable for baud rate and parity
Note: The Modbus broadcast commands are not supported and will be ignored
There are no standard Modbus function formats defined for the communication of data from a gas
detection system. The host computer system will therefore require programming in order to interpret the
signal and status data made available by the Touchpoint Pro. It is recommended that the host computer
system should, as a minimum, be programmed to use Function 02 to collect alarm and status data from all
channels of the Touchpoint Pro Control System.
Full details of the Modbus protocol can be found in the latest revision of the Modicon Modbus Protocol
Reference Guide PI-MBUS-300 available at
www.modbus.org
.
Note. Some transceiver manufacturers incorrectly use RS-485 pin A as data positive and pin B as data
negative. You may have to swap over TDA and TDB (A in and B in) if your Modbus does not work as
expected.
The addressing conventions and register values used follow those set by Modicon. The first digit of the
on-board memory address refers to the data type stored in the register and therefore defines the Modbus
function command that should be used when polling it.
1
xxxx
– The Input Status Register addresses record the individual channels’ status. They are read using
Modbus Function 02
3
xxxx
– The Input Register addresses record the current input values of the individual channels. They are
read using Modbus Function 04
4
xxxx
– The Holding Register addresses have two purposes. One range of addresses is used to send
commands and receive the results of those commands. The other address range is used to send queries
and store the results of those queries. They can be written singly using Modbus Function 06, written as a
block using Modbus Function 16 and read using Modbus Function 03.
14. Appendix 1 - Modbus Option