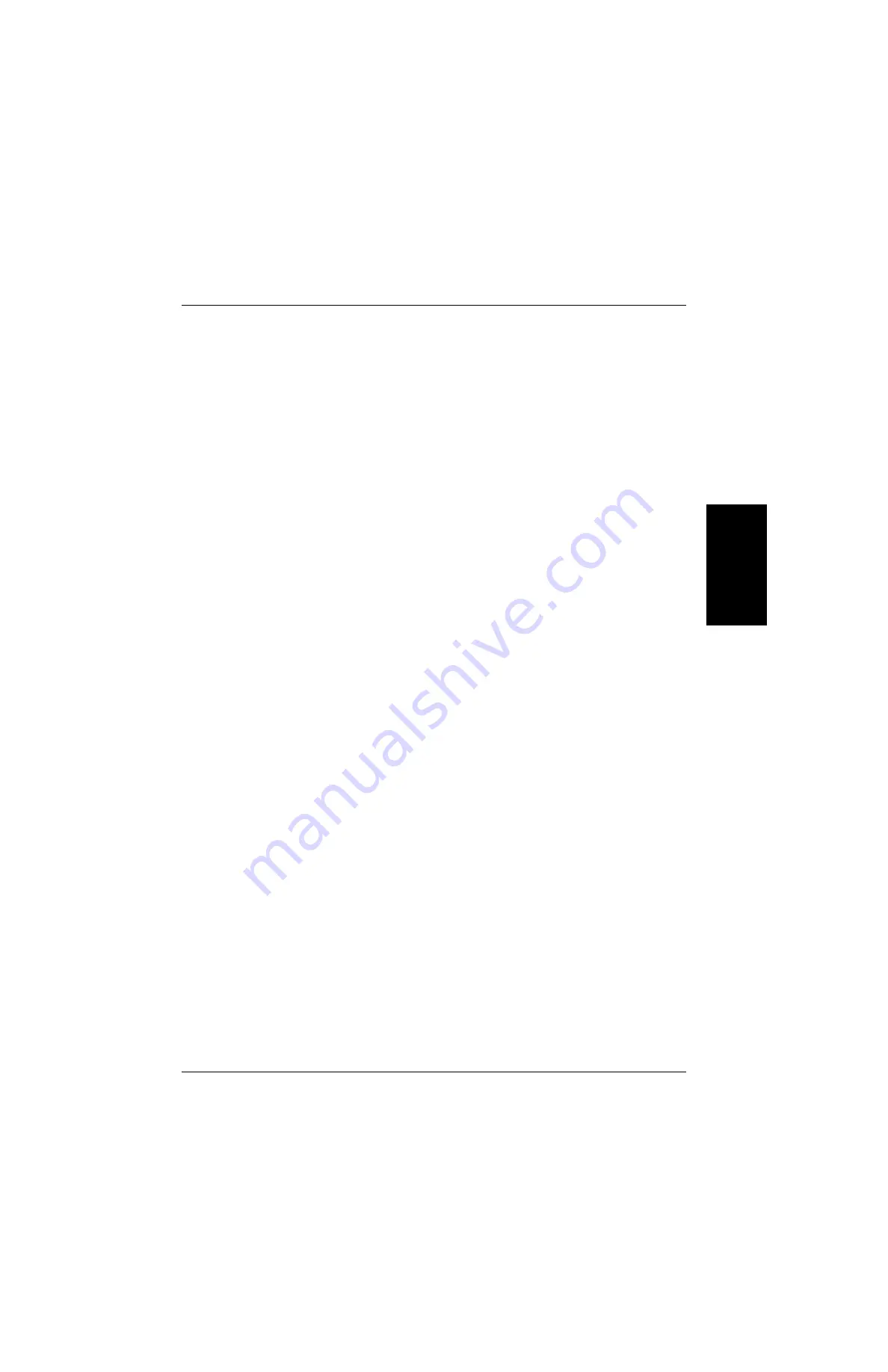
Electrical System
Chapter 3: Theory of Operation
The Controller Area Network (CAN) is a common Small Area Network
solution that supports distributed product and distributed system architectures.
The CAN bus is used to interconnect a network of electronic nodes or modules.
Typically, a two wire, twisted pair cable is used for the network
interconnection. The CAN protocol is a set of stringent rules, implemented in
silicon, that supports the serial transfer of information between two or more
nodes. CAN is implemented by a large number of industries including
automotive, truck, bus, agriculture, marine, construction, medical, factory
automation, textile, and many others. CAN is used as the basis for several
major "7-layer" protocol developments such as J1939, CANopen, ISO11783,
DeviceNet, and NMEA2000. Each of these large protocol architectures are
essentially complete industry-specific network solutions packaged to include
defined requirements for the physical layer, address structure, message
structure, conversation structure, data structure, and application/ network
interface. Pre-packaged "7-layer" protocols provide high value for vertically
integrated industries like heavy truck, marine, or factory automation. On the
other end of the spectrum, many other companies choose to develop a
proprietary distributed product strategy. For both business and technical
reasons, these companies internally create a customized "7-layer" CAN-based
protocol that is optimized to satisfy their own application-specific
requirements. The VersaCare™ Bed uses a proprietary CANopen solution,
similar to what is used in the automobile industry.
Power Supply
Power Source
The bed is powered by 100, 110, 115, 120, 127, 220, 230, or 240 V AC,
50/60 Hz, single phase power and 24 V DC internal battery power. When AC
power is available, the bed is powered by the transformer and the battery is
being charged. When AC power is removed, the bed will shut down (no
power). To use the battery backup, the user must press the battery enable
switch. In battery backup mode, only the motors will function and all nodes
will be powered up. After 10 minutes of no function switch activity, the bed
will shut down (no power). This is the method used to save battery power.
The two primary fuses are 5.0 A, 250 V, TD, UL, 5X20 for 100, 110, 115, 120,
and 127 V beds, and a 2.5 A, 250 V TD, IEC, 5 x 20 mm fuse for the 220, 230,
and 240 V beds. The toroidal transformer is designed to provide 24 VDC at
node VMOT_UR when the load at this node is 12 A DC. The transformer is
designed to provide 36 VDC at node VLOG_UR when the load at this node is
3.5 A DC. At peak load the primary current is 5.7 Arms which corresponds to
684 VA. There are two secondary windings. Secondary 1 is rated at 21Vrms @
20.4 Arms with regulation < 6%. Secondary 1 provides DC motor power, dc
3
VersaCare™ Bed Service Manual (MAN333 REV 2)
Page 3 - 5
Summary of Contents for VersaCare P3200
Page 2: ......
Page 6: ...Revisions NOTES Page iv VersaCare Bed Service Manual MAN333 REV 2 ...
Page 18: ...NOTES Page xvi VersaCare Bed Service Manual MAN333 REV 2 ...
Page 270: ...Exchange Policy Chapter 5 Parts List NOTES Page 5 4 VersaCare Bed Service Manual MAN333 REV 2 ...
Page 272: ...Warranty Chapter 5 Parts List NOTES Page 5 6 VersaCare Bed Service Manual MAN333 REV 2 ...
Page 279: ...Base Frame Chapter 5 Parts List NOTES 5 VersaCare Bed Service Manual MAN333 REV 2 Page 5 13 ...
Page 281: ...Casters Chapter 5 Parts List NOTES 5 VersaCare Bed Service Manual MAN333 REV 2 Page 5 15 ...
Page 340: ...CPR Cable Chapter 5 Parts List NOTES Page 5 74 VersaCare Bed Service Manual MAN333 REV 2 ...
Page 363: ......
Page 365: ...Electronics Schematic P3200 Sheet 1 of 3 Chapter 3 ...
Page 366: ...Electronics Schematic P3200 Sheet 2 of 3 Chapter 3 ...
Page 367: ...Electronics Schematic P3200 Sheet 3 of 3 Chapter 3 ...
Page 368: ...Motor Control P C Board Schematic PN 68717 Chapter 3 ...
Page 369: ...Logic Control P C Board Schematic PN 69378 Chapter 3 ...
Page 370: ...Siderail Controls Schematic Chapter 3 ...
Page 371: ...Optional Controls Schematic Chapter 3 ...
Page 372: ...Patient Controls Schematic Chapter 3 ...
Page 373: ...Patient Pendant Schematic Chapter 3 ...
Page 374: ...Power Supply PN 72289 Sheet 1 of 2 Chapter 3 ...
Page 375: ...Power Supply PN 72289 Sheet 2 of 2 Chapter 3 ...
Page 376: ...Motor Control P C Board PN 72273 Chapter 3 ...
Page 377: ...Power Supply P C Board PN 70786 Sheet 1 of 2 Chapter 3 ...
Page 378: ...Power Supply P C Board PN 70786 Sheet 2 of 2 Chapter 3 ...