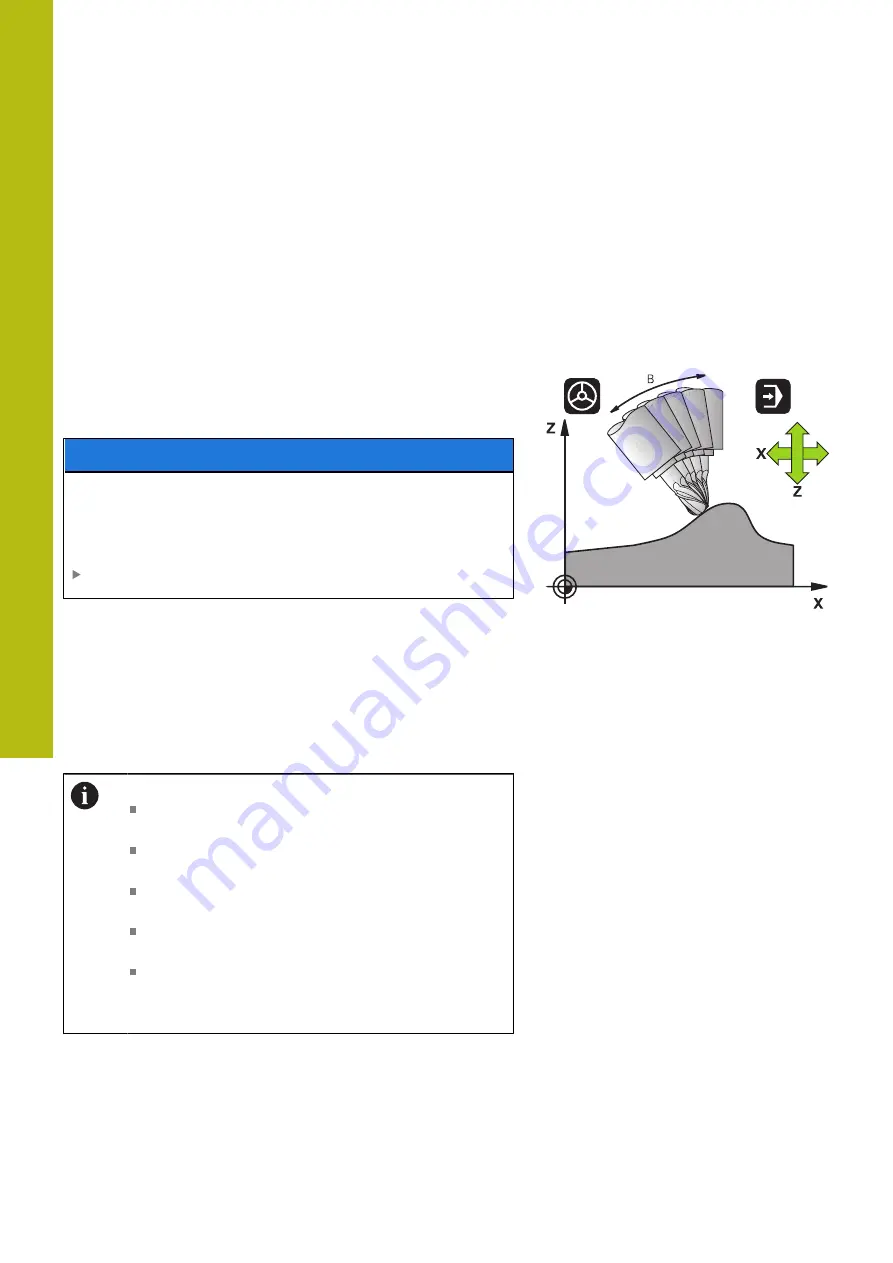
Multiple-Axis Machining | Miscellaneous functions for rotary axes
13
620
HEIDENHAIN | TNC 640 | Conversational Programming User's Manual | 10/2017
Maintaining the position of the tool tip when
positioning with tilted axes (TCPM): M128 (option 9)
Standard behavior
If the inclination angle of the tool changes this results in an offset
of the tool tip compared to the nominal position. The control does
not compensate this offset. If the operator does not take this
deviation into account in the NC program, offset machining is
executed.
Behavior with M128 (TCPM: Tool Center Point Management)
If the position of a controlled tilted axis changes in the program,
the position of the tool tip in relation to the workpiece remains the
same during the tilting process.
NOTICE
Danger of collision!
Rotary axes with Hirth coupling must move out of the coupling
to enable tilting. There is a danger of collision while the axis
moves out of the coupling and during the tilting operation.
Tool retracted before the position of the tilting axis is changed
After
M128
, you can program a feed rate at which the control will
carry out the compensation movements in the linear axes.
If you want to change the position of the tilting axis with the
handwheel during the program run, use
M128
along with
M118
.
Superimposing handwheel positioning is implemented with active
M128
, depending on the setting in the 3D-ROT menu of the
Manual
operation
operating mode, in the active coordinate system or in
the non-tilted coordinate system.
Programming notes:
Before positioning axes with
M91
or
M92
and before
a
TOOL CALL
block, reset the
M128
function
To avoid contour damage, you must use only
spherical cutters with
M128
.
The tool length must refer to the spherical center of
the tool tip.
If
M128
is active, the control shows the
TCPM
symbol in the status display
The
TCPM
or
M128
function cannot be used in
conjunction with the
Dynamic Collision Monitoring
(DCM)
function and the additional
M118
function
Summary of Contents for TNC 640
Page 4: ......
Page 5: ...Fundamentals ...
Page 36: ...Contents 36 HEIDENHAIN TNC 640 Conversational Programming User s Manual 10 2017 ...
Page 67: ...1 First Steps with the TNC 640 ...
Page 90: ......
Page 91: ...2 Introduction ...
Page 130: ......
Page 131: ...3 Operating the Touchscreen ...
Page 144: ......
Page 145: ...4 Fundamentals File Management ...
Page 206: ......
Page 207: ...5 Programming Aids ...
Page 236: ......
Page 237: ...6 Tools ...
Page 281: ...7 Programming Contours ...
Page 333: ...8 Data Transfer from CAD Files ...
Page 355: ...9 Subprograms and Program Section Repeats ...
Page 374: ......
Page 375: ...10 Programming Q Parameters ...
Page 478: ......
Page 479: ...11 Miscellaneous Functions ...
Page 501: ...12 Special Functions ...
Page 584: ......
Page 585: ...13 Multiple Axis Machining ...
Page 650: ......
Page 651: ...14 Pallet Management ...
Page 664: ......
Page 665: ...15 Batch Process Manager ...
Page 673: ...16 Turning ...
Page 713: ...17 Manual Operation and Setup ...
Page 797: ...18 Positioning with Manual Data Input ...
Page 803: ...19 Test Run and Program Run ...
Page 843: ...20 MOD Functions ...
Page 881: ...21 Tables and Overviews ...