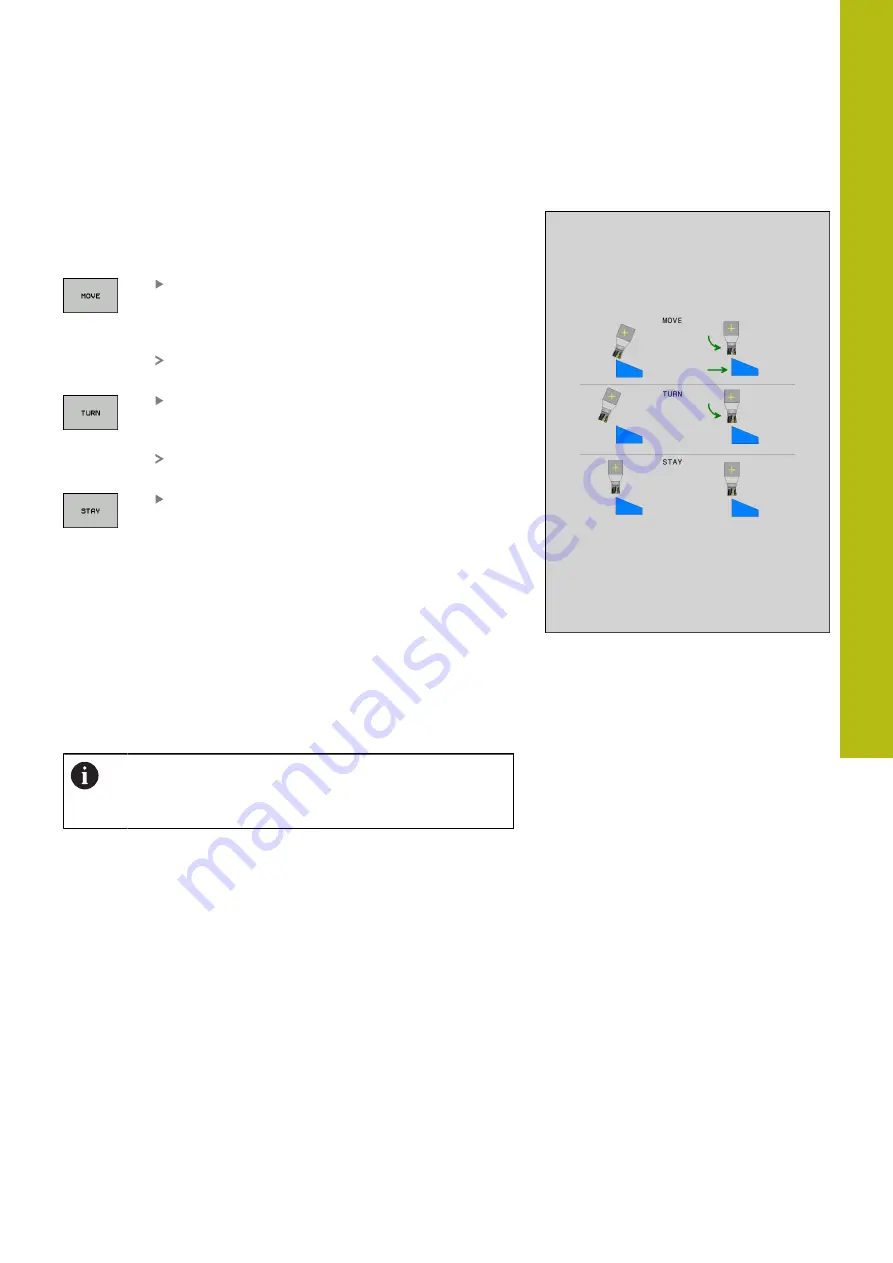
Multiple-Axis Machining | The PLANE function: Tilting the working plane (option 8)
13
HEIDENHAIN | TNC 640 | Conversational Programming User's Manual | 10/2017
607
Automatic positioning: MOVE/TURN/STAY (entry is
mandatory)
After you have entered all parameters for the plane definition,
you must specify how the rotary axes will be positioned to the
calculated axis values:
The PLANE function is to automatically position
the rotary axes to the calculated position values.
The position of the tool relative to the workpiece
remains the same.
The control carries out a compensation
movement in the linear axes.
The PLANE function is to automatically position
the rotary axes to the calculated position values,
but only the rotary axes are positioned.
The control does
not
carry out a compensation
movement for the linear axes.
You will position the rotary axes later in a
separate positioning block
If you selected the
MOVE
option (the
PLANE
function is used to
position the axes automatically), the following two parameters:
Dist. tool tip – center of rot.
and
Feed rate? F =
are still to be
defined.
If you selected the
TURN
option (the
PLANE
function is used to
position the axes automatically), the following parameter:
Feed
rate? F =
is still to be defined.
As an alternative to defining a feed rate
F
directly by entering a
numerical value, you can also position the axes with
FMAX
(rapid
traverse) or
FAUTO
(feed rate from the
TOOL CALL
block).
If you use
PLANE
together with
STAY,
you have to
position the rotary axes in a separate block after the
PLANE
function.
Summary of Contents for TNC 640
Page 4: ......
Page 5: ...Fundamentals ...
Page 36: ...Contents 36 HEIDENHAIN TNC 640 Conversational Programming User s Manual 10 2017 ...
Page 67: ...1 First Steps with the TNC 640 ...
Page 90: ......
Page 91: ...2 Introduction ...
Page 130: ......
Page 131: ...3 Operating the Touchscreen ...
Page 144: ......
Page 145: ...4 Fundamentals File Management ...
Page 206: ......
Page 207: ...5 Programming Aids ...
Page 236: ......
Page 237: ...6 Tools ...
Page 281: ...7 Programming Contours ...
Page 333: ...8 Data Transfer from CAD Files ...
Page 355: ...9 Subprograms and Program Section Repeats ...
Page 374: ......
Page 375: ...10 Programming Q Parameters ...
Page 478: ......
Page 479: ...11 Miscellaneous Functions ...
Page 501: ...12 Special Functions ...
Page 584: ......
Page 585: ...13 Multiple Axis Machining ...
Page 650: ......
Page 651: ...14 Pallet Management ...
Page 664: ......
Page 665: ...15 Batch Process Manager ...
Page 673: ...16 Turning ...
Page 713: ...17 Manual Operation and Setup ...
Page 797: ...18 Positioning with Manual Data Input ...
Page 803: ...19 Test Run and Program Run ...
Page 843: ...20 MOD Functions ...
Page 881: ...21 Tables and Overviews ...