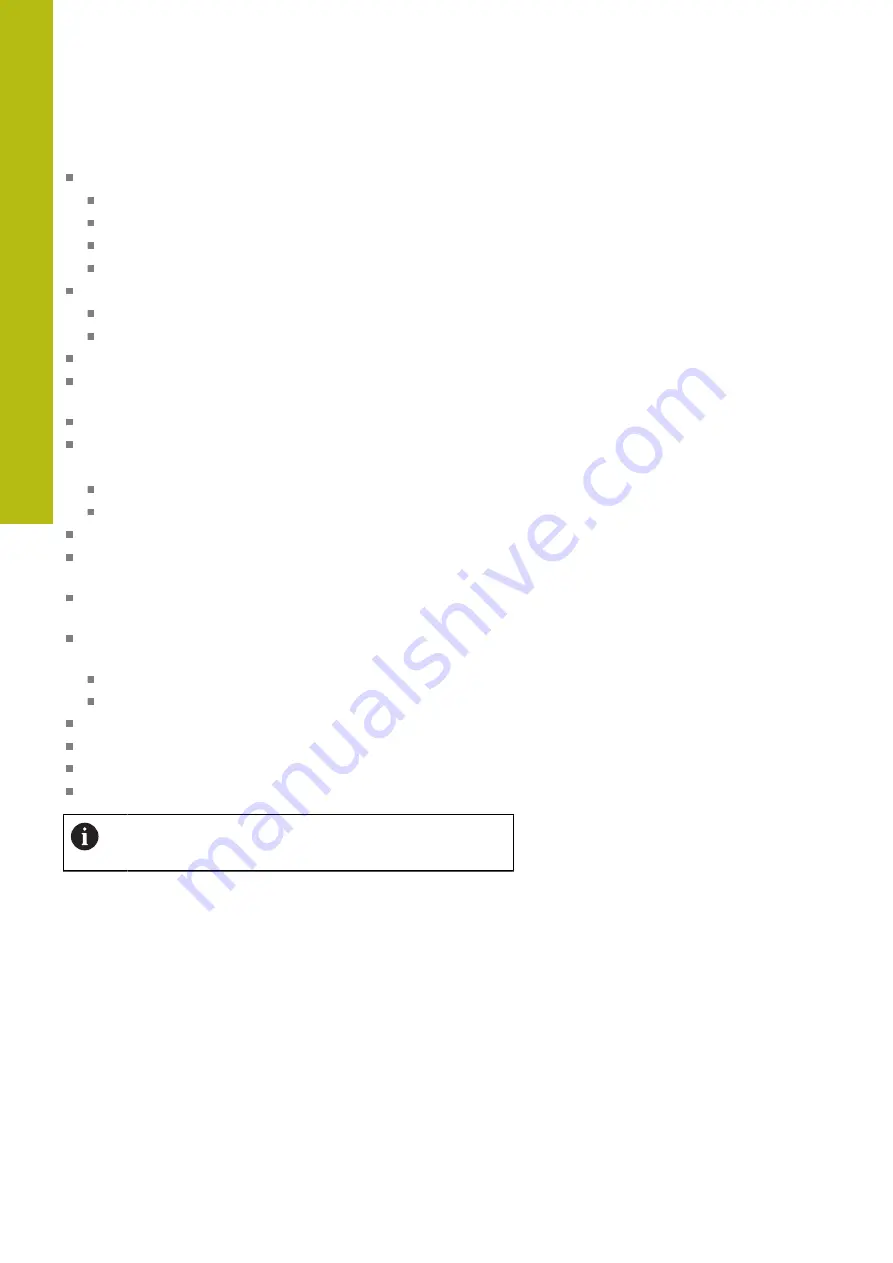
Teach-in | Thread and undercut cycles
5
320
HEIDENHAIN | MANUALplus 620 | User's Manual | 12/2017
GH
:
Type of offset
0: Without offset
1: From left
2: From right
3: Alternating left/right
A
:
Approach ang.
(range: –60° <
A
< 60°; default: 30°)
A
< 0: Infeed on left thread flank
A
> 0: Infeed on right thread flank
R
:
Rem. cut depth
(only with
GV
= 4; default: 1/100 mm)
E
:
Incremental gradient
– Variable thread pitch (e.g. for
manufacturing spiral conveyors or extrusion shafts)
Q
:
Number no-load.
IC
:
Number of cuts
– the infeed is calculated from
IC
and
U
Usable with:
GV
= 0: Constant chip cross section
GV
= 1: Constant infeed
MT
:
M after T
:
M
function that is executed after the tool call
T
MFS
:
M at beginning
:
M
function that is executed at the
beginning of the machining step
MFE
:
M at end
:
M
function that is executed at the end of the
machining step
WP
:
No. of spindle
– Displays which workpiece spindle is used
to execute the cycle (machine-dependent)
Main drive
Opposing spindle for rear-face machining
BW
:
Angle in the B axis
(machine-dependent)
CW
:
Reverse the tool
(machine-dependent)
HC
:
Shoe brake
(machine-dependent)
DF
:
Miscellaneous function
(machine-dependent)
Type of machining for technology database access:
Thread cutting
Cycle run:
1 Calculate the proportioning of cuts
2 Start the first thread groove at the
Start point
Z
3 Move to the
End point thread
Z2
at the programmed feed rate
4 Return on a paraxial path and approach for the next thread
groove
5 Repeat 3 to 4 for all thread grooves
6 Approach for the next pass, taking the
reduced cutting depth
and the
Approach ang.
A
into account
7 Repeat 3 to 6 until
No.gears
D
and
Thread depth
U
are reached
8 Move to the
Tool change point
according to the setting in
G14
Summary of Contents for 548431-05
Page 1: ...MANUALplus 620 User s Manual NC Software 548431 05 English en 12 2017...
Page 2: ......
Page 3: ...Overview of keys...
Page 7: ...Fundamentals...
Page 22: ...22 HEIDENHAIN...
Page 24: ...Contents 24 HEIDENHAIN MANUALplus 620 User s Manual 12 2017...
Page 41: ...1 Introduction and fundamentals...
Page 58: ......
Page 59: ...2 Basics of operation...
Page 83: ...3 Operating the Touchscreen...
Page 90: ......
Page 91: ...4 Machine mode of operation...
Page 170: ......
Page 171: ...5 Teach in...
Page 415: ...6 ICP programming...
Page 529: ...7 Graphic simulation...
Page 556: ......
Page 557: ...8 Tool and technology database...
Page 602: ......
Page 603: ...9 Organization mode of operation...
Page 677: ...10 Tables and overviews...
Page 711: ...11 Overview of cycles...