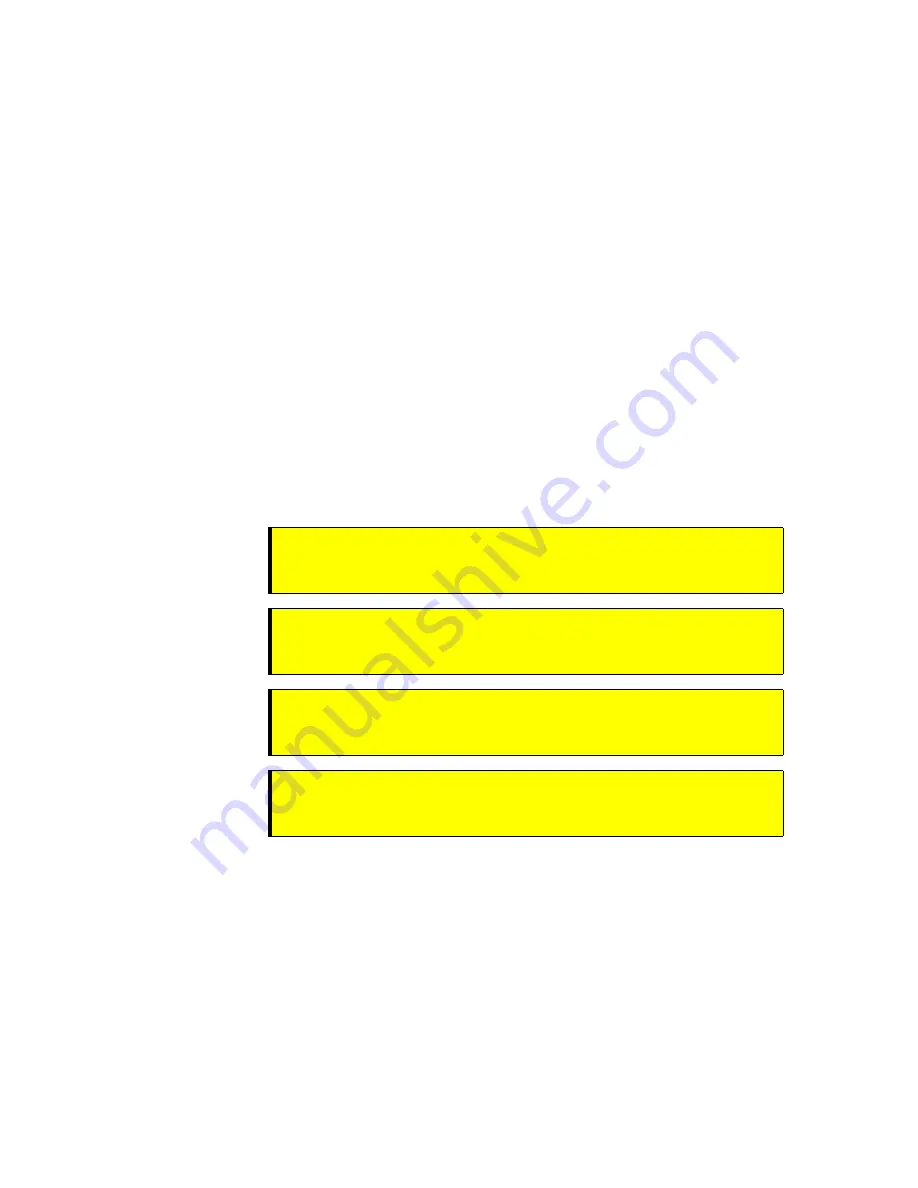
Troubleshooting
147
•
•
•
•
•
•
Chapter 9
• • • • • •
Troubleshooting
Chapter 9 provides procedures for troubleshooting the electrical, mechanical and firmware
elements of the HI 6500 series instrument and for using Hardy’s Integrated Technician
(IT®) software utility to isolate problems. Flow charts provide troubleshooting procedures
for the ontroller, load cells, and cabling.
NOTE
Never run Hardy’s Integrated Technician testing while in a production mode. The
reported weight readings will not be correct and can cause equipment to start or stop
unpredictably.
Disassembly and Reassembly Notes, Warnings & Cautions
Always disconnect the power cord before disassembling.
•
Always replace broken or damaged modules or hardware immediately.
•
Always check to be sure that no loose parts are sitting on printed circuit boards or
electrical connectors or wires when disassembling or reassembling.
•
Always protect printed circuit boards from electrostatic discharge (ESD). Always use
approved ESD wrist straps and anti-static pads.
WARNING - EXPLOSION HAZARD - DO NOT REPLACE COMPONENTS
UNLESS POWER HAS BEEN SWITCHED OFF OR AREA IS KNOWN TO BE NON-
HAZARDOUS.
AVERTISSEMENT – Risque d’explosion- Ne pas remplacer les composants à
moins que la source d’alimentation soit éteinte ou que la zone est classifiée non
dangereuse.
WARNING - EXPLOSION HAZARD - DO NOT DISCONNECT EQUIPMENT
UNLESS POWER HAS BEEN SWITCHED OFF OR THE AREA IS KNOWN TO BE
NON-HAZARDOUS
AVERTISSEMENT – Risque d’explosion – Ne pas déconnecter l’équipement à
moins que la source d’alimentation ait été mise en position « éteint » ou que la
zone soit classifiée non dangereuse.
Summary of Contents for HI 6500 Series
Page 10: ...viii Contents ...
Page 20: ...10 Chapter 2 ...
Page 72: ...62 Chapter 4 ...
Page 96: ...86 Chapter 5 Profibus DP Commands and Parameters ...
Page 97: ...Instrument Configuration 87 Serial Option Termination ...
Page 126: ...116 Chapter 5 ...
Page 156: ...146 Chapter 8 ...
Page 163: ...Troubleshooting 153 General Troubleshooting Flow Chart Index ...
Page 164: ...154 Chapter 9 A Guideline Instability Electrical and Mechanical review ...
Page 165: ...Troubleshooting 155 A1 Checking for Unstable Components in a Weighing System ...
Page 166: ...156 Chapter 9 B Guidelines for Electrical Mechanical or Configuration Issues ...
Page 167: ...Troubleshooting 157 B1 Guidelines to Verify Electrical Installation ...
Page 168: ...158 Chapter 9 B2 Guidelines to Verify Mechanical Installation ...
Page 170: ...160 Chapter 9 C Integrated Technician and Stability Test Overview ...
Page 171: ...Troubleshooting 161 E Testing for Non Return to Zero System with IT Summing Card ...
Page 173: ...Troubleshooting 163 G Calibration Errors When Performing the Calibration ...
Page 174: ...164 Chapter 9 H Mechanical Installation ...
Page 175: ...Troubleshooting 165 J Electrical Inspection ...
Page 176: ...166 Chapter 9 K Installation Check Points ...
Page 177: ...Troubleshooting 167 M Weight Processor s Front Display is Blank or Locked ...
Page 178: ...168 Chapter 9 N Analog Out HI 6510 Only ...
Page 194: ...184 Appendix A Figure D1 Assembling the Swivel Mount Enclosure on the instrument pedestal ...
Page 196: ...186 Appendix A Dimensions ...
Page 200: ...4 HI 6500 Series USER GUIDE Index ...
Page 201: ......