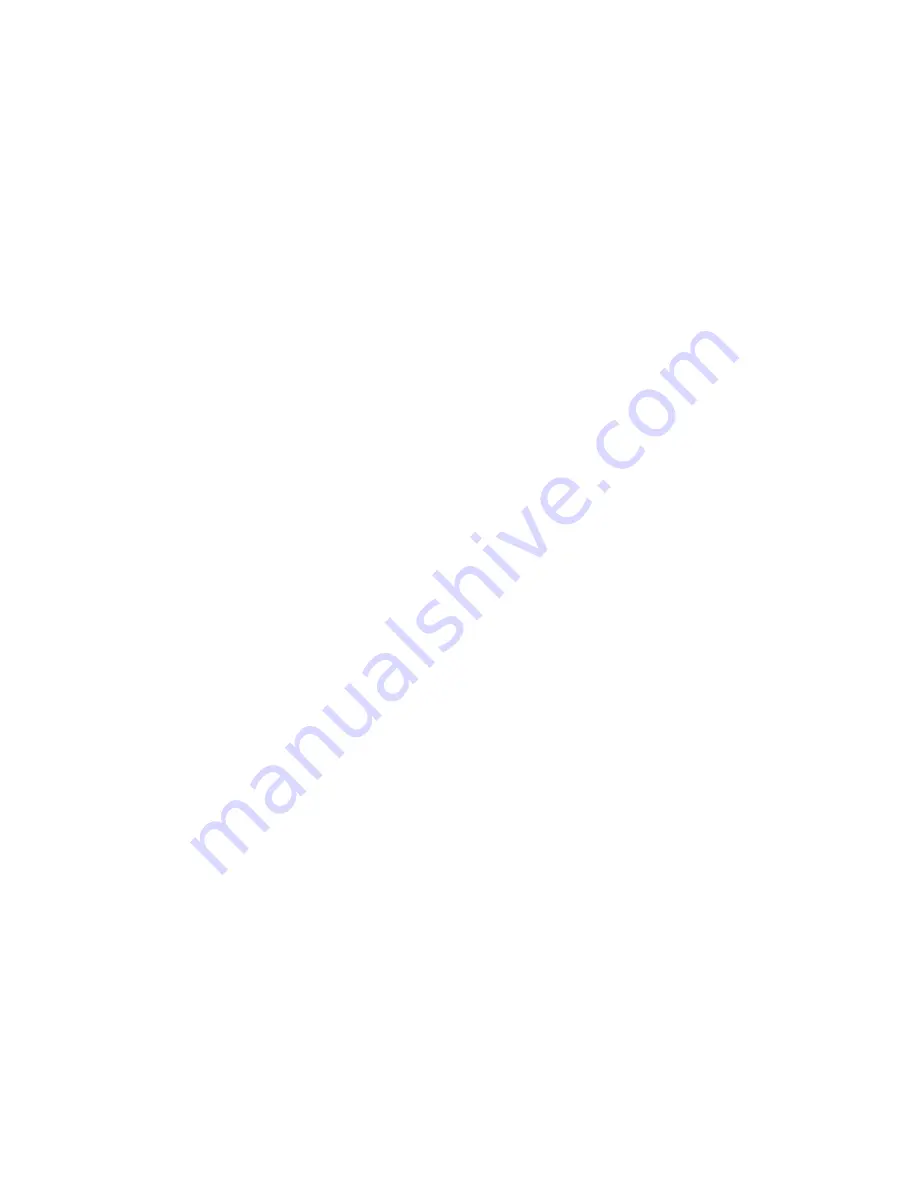
CHAPTER 3: MOTOR PR OTECTION
3.2
EP OS MOTOR MANAGEMENT SYSTEM – INSTRUCTION MANUAL
3.1.1 Unbalance and phase-loss biasing
Unbalanced phase currents (that is, negative-sequence currents) cause rotor heating in addition to the normal heating
caused by positive-sequence currents. When the motor is running, the rotor rotates in the direction of the positive-
sequence MMF wave at near synchronous speed. The induced rotor currents are at a frequency determined by the
difference between synchronous speed and rotor speed, typically 2 to 4 Hz. At these low frequencies, the current flows
equally in all parts of the rotor bars, right down to the inside portion of the bars at the bottom of the slots. On the
other hand, negative-sequence stator current causes an MMF wave with a rotation opposite to rotor rotation, which
induces a rotor current with a frequency approximately two times the line frequency (100 Hz for a 50 Hz system or 120
Hz for a 60 Hz system). The skin effect at this frequency restricts the rotor current to the outside portion of the bars at
the top of the slots, causing a significant increase in rotor resistance and therefore, significant additional rotor
heating. This extra heating is not accounted for in the thermal limit curves supplied by the motor manufacturer. These
curves assume only positive-sequence currents from a perfectly balanced supply and balanced motor construction.
To account for this additional heating, the EntelliPro ES allows the thermal model to be biased with negative-
sequence current . This biasing is accomplished by multiplying the average current by 1.43 in case of phase unbalance
and 1.85 in case of phase loss.
3.1.2 Hot/cold biasing
When the motor is running with a constant load below the overload level, the motor will eventually reach a steady-
state temperature that corresponds to a particular steady-state thermal capacity. As thermal capacity is used, the
thermal capacity left in the motor to cover transient overloads is less than what is available when the motor is cold.
The safe stall time (also known as locked-rotor time) is the time taken, with the rotor not turning, for the motor to heat
to a temperature beyond which motor damage occurs at an unacceptable rate. The term cold refers to the state
when the motor is at an ambient temperature, while hot refers to the state when the motor at the temperature
reached when running at the rated load. The method that the thermal model uses to account for the pre-overload
state is thus known as hot/cold biasing.
At power down, the thermal overload accumulator value, which defines the heating state of the motor, and the real
time clock time stamp, are stored in on-board EEPROM. On the subsequent application of power, the accumulator
value will be read and restored in the overload protection. The overload protection will use this value provided.
If a new time stamp is supplied by a Modbus or Profibus DP master, the time difference between the power down and
power up events is calculated and a new accumulator value is generated.