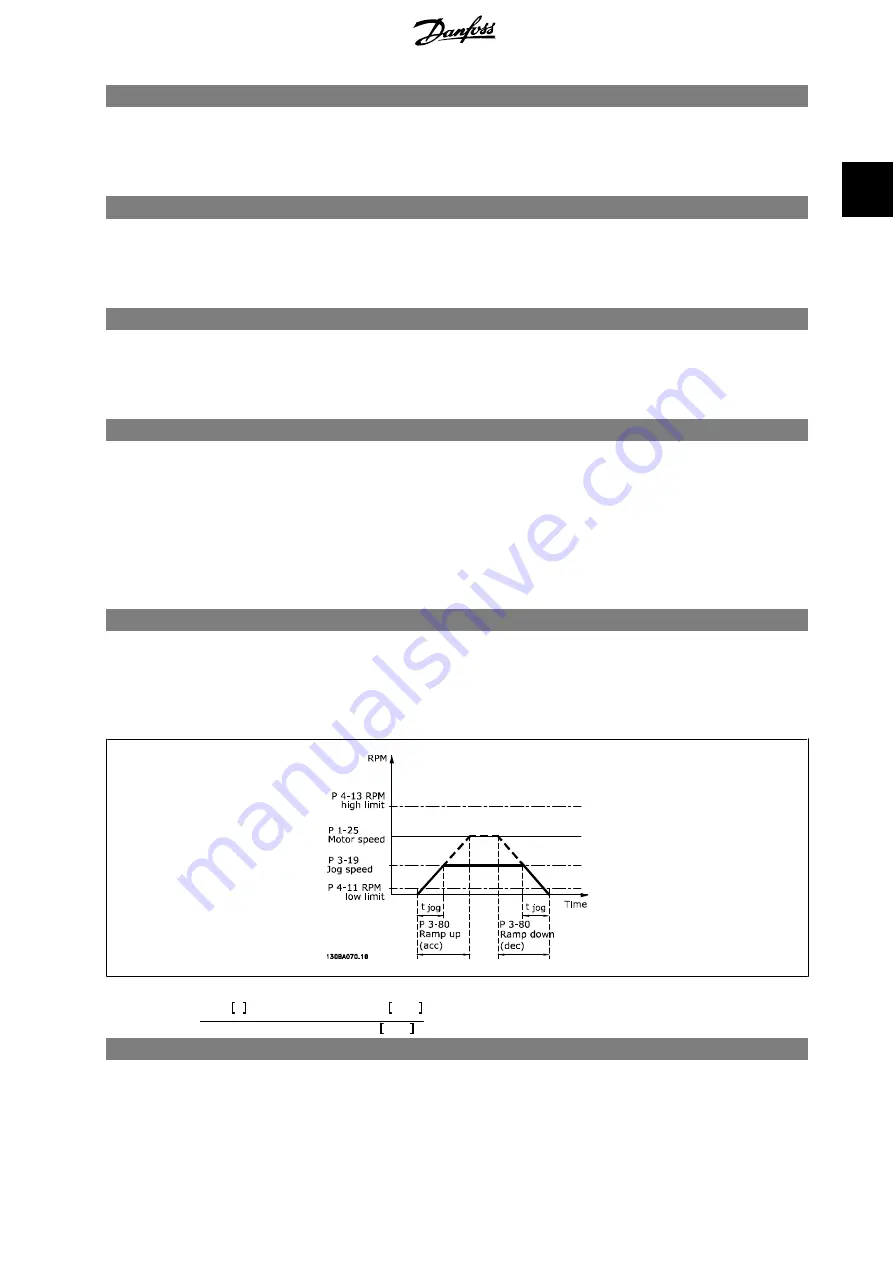
3-75 Ramp 4 S-ramp Ratio at Accel. Start
Range:
Function:
50%
*
[1 - 99%]
Enter the proportion of the total ramp-up time (par. 3-71) in which the acceleration torque increases. The larger
the percentage value, the greater the jerk compensation achieved, and thus the lower the torque jerks in the
application.
3-76 Ramp 4 S-ramp Ratio at Accel. End
Range:
Function:
50%
*
[1 - 99%]
Enter the proportion of the total ramp-up time (par. 3-71) in which the acceleration torque decreases. The larger
the percentage value, the greater the jerk compensation achieved, and thus the lower the torque jerks in the
application.
3-77 Ramp 4 S-ramp Ratio at Decel. Start
Range:
Function:
50%
*
[1 - 99%]
Enter the proportion of the total ramp-down time (par. 3-72) where the deceleration torque increases. The larger
the percentage value, the greater the jerk compensation achieved, and thus the lower the torque jerks in the
application.
3-78 Ramp 4 S-ramp Ratio at Decel. End
Range:
Function:
50%
*
[1 - 99%]
Enter the proportion of the total ramp-down time (par. 3-72) where the deceleration torque decreases. The larger
the percentage value, the greater the jerk compensation achieved, and thus the lower the torque jerks in the
application.
2.6.8. 3-8* Other Ramps
Configure parameters for special ramps e.g. Jog or Quick Stop.
3-80 Jog Ramp Time
Range:
Function:
Size related [0.01 - 3600.00 s]
Enter the jog ramp time, i.e. the acceleration/deceleration time between 0 RPM and the rated motor frequency
n
M,N
(set in par. 1-25
Motor Nominal Speed
). Ensure that the resultant output current required for the given jog
ramp time does not exceed the current limit in par. 4-18. The jog ramp time starts upon activation of a jog signal
via the control panel, a selected digital input, or the serial communication port.
Par. 3
−
80 =
tjog s x nM, N (par. 1
−
25)
RPM
Δ
log speed (par. 3
−
19)
RPM
3-81 Quick Stop Ramp Time
Range:
Function:
3 s
*
[0.01 - 3600.00 s]
Enter the quick–stop ramp-down time, i.e. the deceleration time from the rated motor speed to 0 RPM. Ensure
that no resultant over-voltage will arise in the inverter due to regenerative operation of the motor required to
achieve the given ramp-down time. Ensure also that the generated current required to achieve the given ramp-
FC 300 Programming Guide
2. How to Programme
MG.33.M3.02 - VLT
®
is a registered Danfoss trademark
71
2