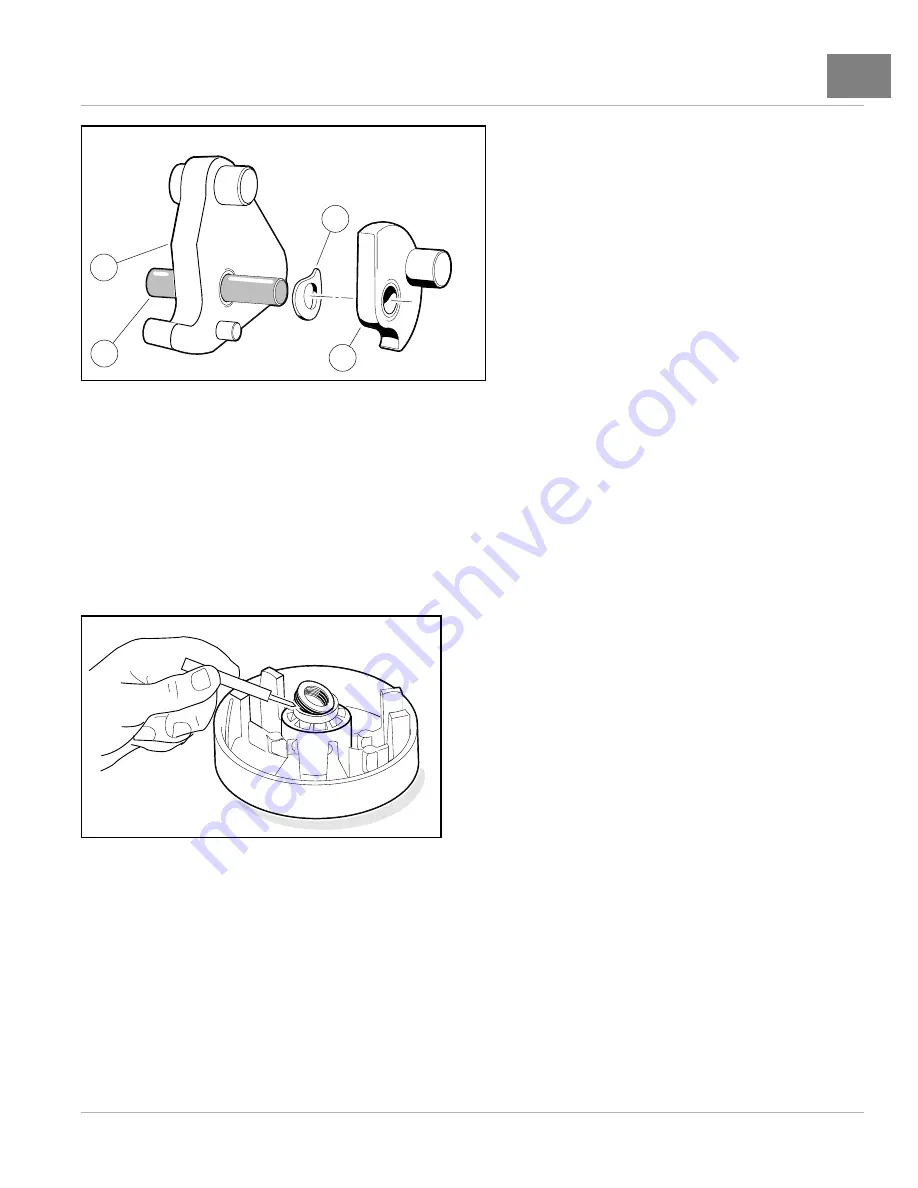
GASOLINE VEHICLE - CLUTCHES
Drive Clutch
23
2
3
4
1
602
Figure 23-9
Primary and Secondary Weights, Wave
Washer and Pin
6.
Remove the retaining ring (6) from the shaft of the fixed sheave (18) and slide the moveable sheave (13) off the
shaft
See following NOTE.
NOTE:
If the moveable sheave is removed from the hub of the fixed sheave, the spiral back-up rings (11) must be
replaced with new rings
.
7.
Remove the spacer (14) and spring (15)
.
8.
Use a scribe or small pick to remove the spiral backup rings (11) from each end of the bore in the fixed sheave
.
See also Figure 23-10, Page 23-9.
Discard the rings.
605
Figure 23-10
Spiral Back-up Rings
INSPECTION OF DRIVE CLUTCH PARTS
1.
Inspect the idler spacer (17) for smoothness
.
2.
Inspect the bore of the moveable sheave (13) for scarring or wear. The moveable sheave must be replaced if the
bore is worn to a diameter of 0.883 in. (22.4 mm) or larger
3.
Inspect the steel shaft on the fixed sheave (18). There should be no measurable wear anywhere on the shaft.
Replace the shaft if it is worn, scratched, or damaged.
4.
Inspect the thrust washer (9) for wear. If it is worn more than 0.030 in. (0.76 mm), turn it over or replace it with
a new one.
2020 Precedent,Villager 2 and 4 Maintenance and Service Manual
Page 23-9
Summary of Contents for DS Villager 4
Page 2: ......
Page 6: ......
Page 481: ...GASOLINE ENGINE HARNESS Wiring Diagrams Gasoline Engine Harness 26 ...
Page 482: ... Page intentionally left blank ...
Page 483: ...GASOLINE MAIN HARNESS Wiring Diagrams Gasoline Main Harness 26 ...
Page 484: ... Page intentionally left blank ...
Page 485: ...GASOLINE INSTRUMENT PANEL HARNESS Wiring Diagrams Gasoline Instrument Panel Harness 26 ...
Page 486: ... Page intentionally left blank ...
Page 488: ... Page intentionally left blank ...
Page 489: ...ELECTRIC MAIN HARNESS Wiring Diagrams Electric Main Harness 26 ...
Page 490: ... Page intentionally left blank ...
Page 492: ... Page intentionally left blank ...
Page 494: ... Page intentionally left blank ...
Page 495: ...ELECTRIC LIGHT HARNESS Wiring Diagrams Electric Light Harness 26 ...
Page 496: ... Page intentionally left blank ...
Page 497: ...ELECTRIC DC TO DC CONVERTER HARNESS Wiring Diagrams Electric DC to DC Converter Harness 26 ...
Page 498: ... Page intentionally left blank ...
Page 507: ...NOTES ...
Page 508: ...NOTES ...
Page 509: ......
Page 510: ......