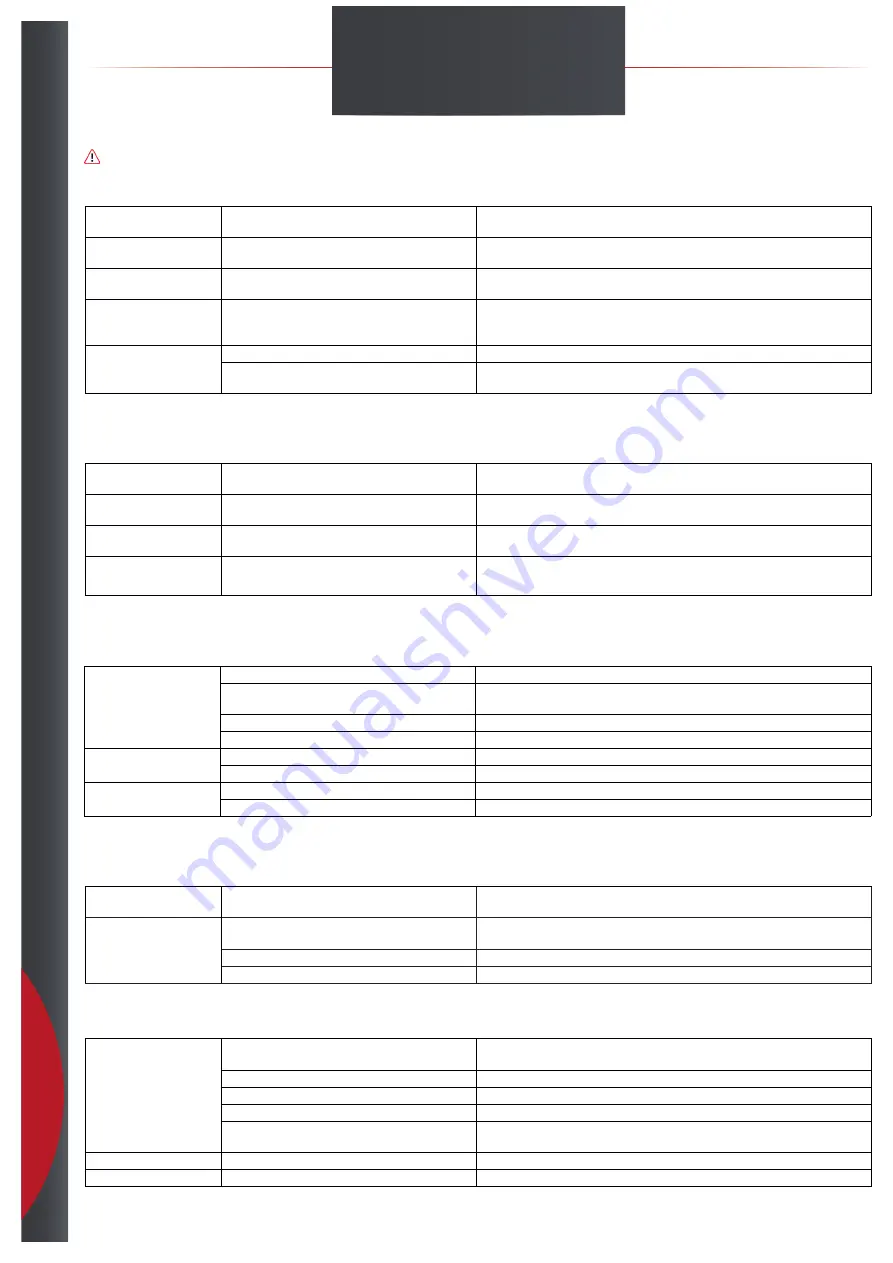
86
Softening - water running to drain
Problem
Cause
Solution
1. The balance piston O-ring is
not seated properly.
Water will leak past an improperly seated balance piston O-ring
and out the drain.
Depress the actuator several times to seat the O-ring. Replace worn or nonconforming O-ring.
2. Bad control disc.
A scored control disc will allow a fast drip to a pencil sized stream
to flow through the drain.
Replace the control disc.
3. The drain or control valve
seals are not seating properly.
Foreign matter under the seals will not allow them to seat
properly.
Disassemble and remove the foreign matter from seals.
4. Low water pressure.
If the water pressure is less than 1 bar / 15 psi at the brine fitting
the system may not operate properly. Test backwashing filters
with the unit in backwash and 1 faucet (cold) running water.
Increase water pressure.
5. The main valve piston quad
rings or level 4 internal quad
rings are not sealing.
The quad rings may be rolled, pinched, torn or just dirty.
Replace and re-silicone the quad rings.
The quad rings may be chloramine or chlorine damaged if on a
chlorine treated water supply.
Replace quad rings with silicone seals. Order chlorine seal kit
Kits available for all models must use MED 420 lubricant.
With softeners and filter/softeners, start by testing the drain water. If the drain water is hard, the tank currently in service has a problem with its drain valve. If the drain water is soft, start with number 1 below.
Softening - taste, color & odor
Problem
Cause
Solution
1. Treated water has a metallic
or iron taste.
See the section entitled ”Softening - iron bleedthrough”.
See the section entitled ”Softening - iron bleedthrough”.
2. Treated water has chlorine
odor and/or taste.
This is due to heavily chlorinated raw city water.
Install a carbon filter.
3. Treated water has a salty
taste.
In high TDS (1000+) applications, salt taste may be present due
to the ion exchange process or sodium chloride in the raw water.
See the section entitled ”Softening - salty treated water”.
4. Treated water has a yellow
tint.
The raw water may have traces of tannins present.
See the section entitled ”Softening - iron bleedthrough”.
If tannins are present, use tannin softener.
Softening - leaks
Problem
Cause
Solution
1. Water leaks from any of the
assembly levels.
Main valve screws are not tightened.
Depressurize the unit and tighten the Main Valve screws
One of the seals between assembly levels (L-1 through L-4) is
pinched or missing.
Replace the non-conforming seal.
One of the screw holes is stripped or cracked.
Replace the base.
There is a crack on the seal area near a screw hole.
Replace the level.
2. Water feed pressure is too
high (max. 8,6 bar / 125 psi).
No pressure regulator installed.
Install pressure regulator.
The pressure regulator is broken.
Replace pressure regulator.
3. Water leaks at the main base
or remote base.
The base is not tightened properly.
Tighten base.
The O-ring on the base is pinched or missing.
Replace base O-ring.
Softening - equipment noise
Problem
Cause
Solution
1. The unit makes a squealing
noise.
The control disc is not flat on the ceramic, causing the drain valve
to flutter.
Replace the control disc, balance piston spring and the balance piston O-ring. You may also want to
change the drain valves and seals.
2. The unit makes a gurgling,
hissing or bubbling sound.
On new installations, there may be some air trapped in the unit
initially.
Run through an entire cycle to allow the air to escape.
Air is being drawn into the plumbing.
Identify air leaks in the plumbing and fix them.
The brine line and/or the brine valve are not air checking
Identify and replace the faulty part(s).
Softening - unit sticks in cycle
Problem
Cause
Solution
1. The unit sticks in regeneration
or backwash cycle.
The regeneration flow path is plugged at the regeneration nozzle
or flow control.
Clean the regeneration flow path.
The regeneration drive pawl and/or spring is weak or broken.
Replace the regeneration drive pawl.
There is a damaged tooth on the control disc.
Replace the control disc.
The eccentric pinion is worn.
Replace the eccentric pinion (snap fit).
On backwashing filters, low pressure or poor backwashing may
cause a plugged bed.
Increase inlet pressure or the frequency of backwash. Unit may need re-bedding.
2. The unit sticks in service cycle. The regeneration start pawl is broken or missing.
Replace or install regeneration start pawl.
The control disc has a worn or missing a tooth.
Replace control disc.
201218