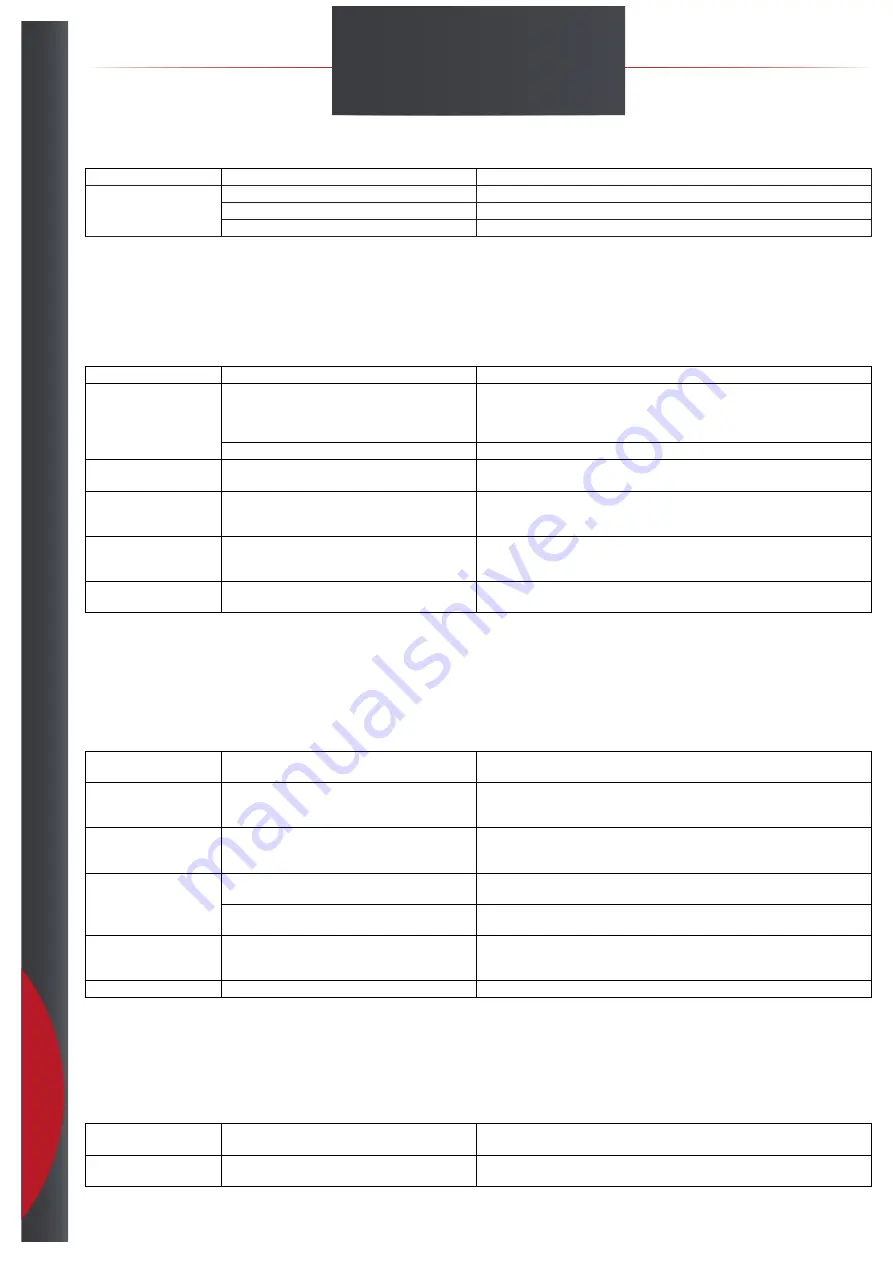
85
Softening - High Salt Consumption
Problem
Cause
Solution
1. Regenerates too frequently.
See the section entitled ”Softening - frequent regeneration”.
See the section entitled ”Softening - frequent regeneration”.
2. Water level in the brine drum
is too high.
The brine valve is set wrong or non-conforming.
Verify the brine valve setting. Replace non-conforming brine valve.
The brine valve or the brine drum is dirty.
Clean brine valve and drum.
The brine valve leaks.
Tighten the connectors on the brine valve.
Softening - salty treated water
Problem
Cause
Solution
1. Restricted drain line.
The drain is kinked or clogged.
Clear any obstructions. Make sure that the drain line flows smoothly and unrestricted.
2. Low water pressure.
The unit should not see water pressure drop below 1 bar / 15 psi
on the outlet at any time. During the backwash portion of the
regeneration cycle, it must hold at least 1 bar / 15 psi or the brine
may not rinse out completely.
Test the outlet pressure with the unit in backwash and one faucet at high flow. Measure the pressure by
placing a gauge on the brine fitting. Raise pressure if below 1 bar / 15 psi.
The prefilter cartridge is clogged.
Replace prefilter cartridge.
3. The backwash flow control is
clogged.
Without enough backwash flow to the drain, the unit cannot
wash all the salt from the media tanks.
Clean the backwash flow control.
4. The drain is extremely long or
placed higher than 2,4 m / 8 ft
above the floor.
Such drain runs can put back-pressure on the unit and restrict the
drain flow. This causes the same result as number 3 above.
Locate a closer drain or use a larger diameter drain line.
5. The upper distributors are
plugged. (This does not apply
to High Efficiency softeners.
Foreign material that finds its way into the media tanks may
be collected around the upper distributors during backwash,
clogging them.
Clean upper distributors. Install a prefilter.
6. Water level in the brine drum
is too high.
The brine valve is set wrong or non-conforming.
Verify the brine valve setting. Replace non-conforming brine valve.
Softening - iron bleed-through
Problem
Cause
Solution
1. Customer plumbing.
Previous iron buildup inside existing plumbing after the water
softener.
Verify that customer plumbing is the problem by testing the water quality at the brine fitting with
water running.
2. The water meter disc is not set
properly for current raw water
conditions.
The composition of raw water can change with time.
Check the hardness and iron content of raw water. Install the correct disc for current raw water
conditions.
3. The salt setting is not set
properly for current raw water
conditions.
The composition of raw water can change with time.
Check the hardness and iron content of raw water. Set the brine valve for current raw water conditions.
4. The iron may be ferric iron.
Ferric iron is not removable by ion exchange.
Verify by using the demo softener to determine if iron is removable by ion exchange. Add additional
equipment if needed.
The iron may be finer than the micron rating of the installed
prefilter cartridge.
Install a cartridge with finer micron rating.
5. The customer’s plumbing may
include a galvanized pressure
tank.
A galvanized pressure tank will create oxidized iron.
Replace the galvanized pressure tank with a bladder style pressure tank.
6. Iron build-up in the softener. High iron bearing water.
Use salt that contains resin cleaning additives.
Softening - pressure loss
Problem
Cause
Solution
1. Reduced pressure entering
the unit.
The prefilter is clogged.
Replace the clogged prefilter.
2. The upper and/or lower
distributors are clogged.
Foreign matter from the input lines is accumulating in the
distributors.
Clean the distributors. Add a prefilter to eliminate the foreign matter before it enters the unit.
201218