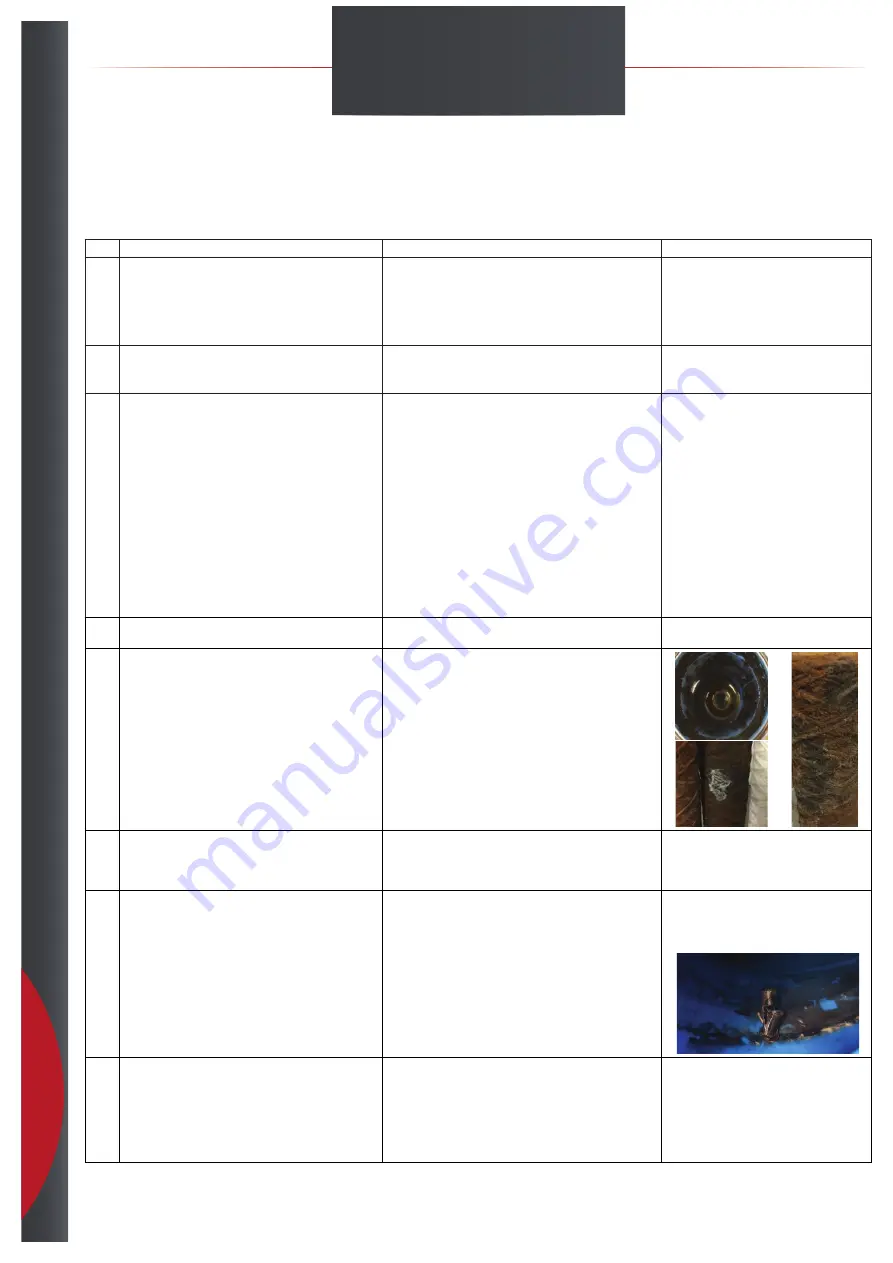
114
11.7
Hygienic
If the system is contaminated or a water sample shows value higher then recommended. Follow the guide below to eliminate the problem.
Note that the result from water report step 1, will tell you if the problem is added from the supply water source. If this is the case, you need to ensure that this issue is
fixed before moving on to step 2.
Step. What
How
Why
1
Ensure that the supply water is within drinking water standard
value.
•
Have a certified lab take a water sample from the valve where the
humidification system is connected.
- Standard test insuring that all values are within drinking water
standard.
- CFU.
- Temperature.
This is to ensure that the quality we start with is OK, or
if the problem starts before the humidification / water
treatment system..
2
Ambient conditions such as, production capacity, ventilation
volume or that the zone/room is used for something else than
when it was installed.
•
Go through the original calculation with the costumer to ensure that
the numbers are still valid.
•
Such as temperature, ventilation, recycle air. Wanted %RH.
Problem starts before the humidification / water
treatment system.
3
Go through the operation and setup with the customer.
•
Go through following list to ensure that the system is not forced into
stop.
•
Is the system ever stopped do to:
- Weekend.
- Season.
- Holidays.
- Energy savings.
- Zone or production hall not in use.
•
Check for:
- Closed units.
- Blinded hoses.
- Setpoint set lower then ordered.
•
Is there any chemical or dosing systems added as an external line
between our RO and the high pressure pump, without galvanic
separation as safety to insure back flow.
•
This is to ensure that the system isn’t controlled in
a way, that can lead to conditions where growth
is possible.
- Temperature.
- Stagnate water.
- Incorrect handling.
- Chemical.
4
Ensure that all components is serviced and maintained according
to the service guide
•
Follow the service guide and hygienic settings.
This is to ensure that lack of service has not let to
microbiologic growth.
5
Filter house and element.
•
Check the filter house and element for visible growth, and check the
filter house surface for biofilm.
6
Check that softener is working on both cylinders, and salt cylinder
is visible clean, and doesn’t have a bad smell.
•
Check the outlet water, and backwash/rinse cycles, as described in
service. Check that the brine valve is working as it should, and that
the water level is according to softener setting as when system was
ordered or adjusted last.
This is to ensure that the filtration and functionality is
as it should be, to insure there is no stagnate water.
7
Check RO system functionality and visual inspection of water tank.
•
Preform a standard service, and a visual inspection of the
water cylinder and hygienic settings.
•
Also use sterile gloves to check inside of the cylinder for biofilm.
•
Also do a capacity check.
This is to ensure that wrong settings, functionality
or handling is done right. The capacity check is to
ensure that capacity is not to high do to reduction in
humidification needs.
8
Filter after RO.
•
Do a visual inspection of the filter element and filter house.
•
Mechanical filters after RO, should be clean and
white. If they have a color, the replacement
of filters isn’t done enough, or it might be an
indicator of a fault before the filter.
•
Yellow color, can be an indicator of chemical
hardener used to print machinery, and should not
be present in humidification line.
201218