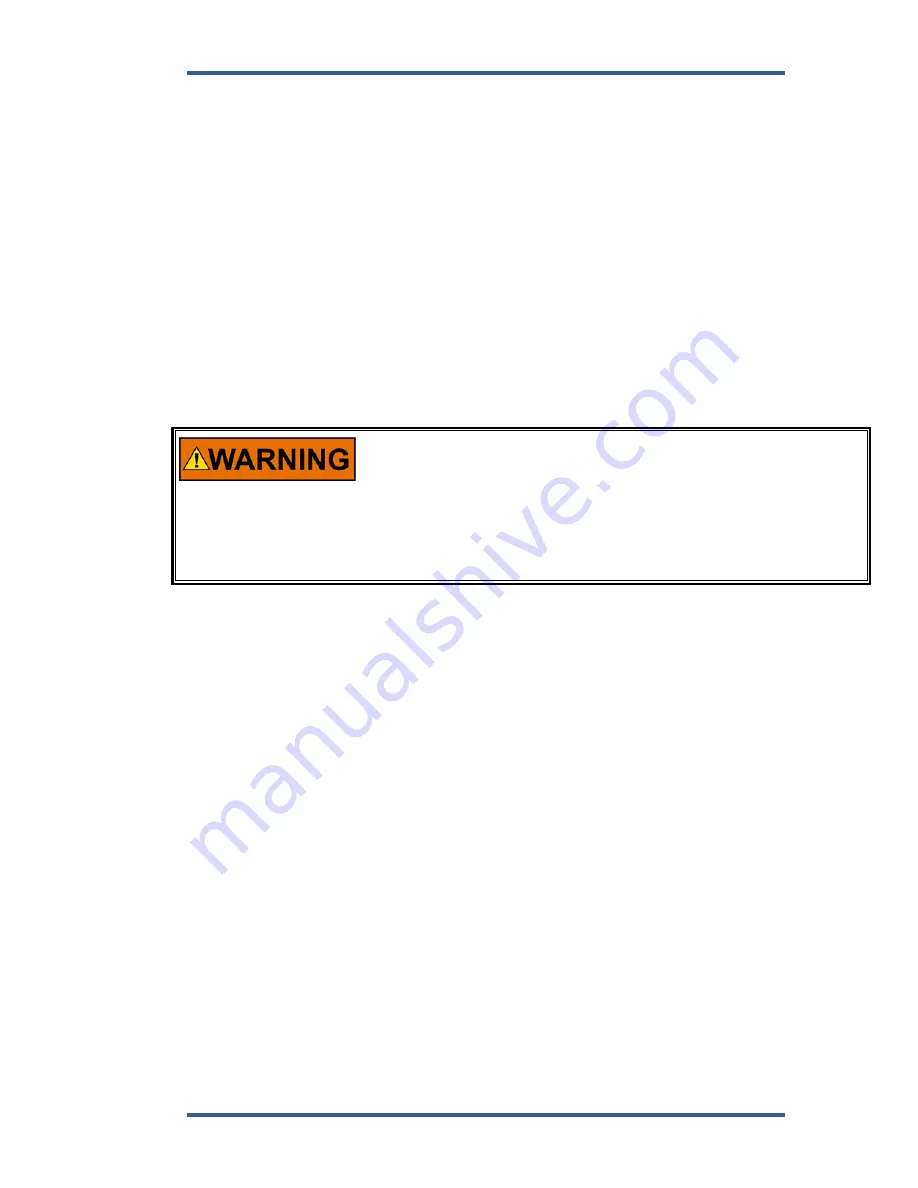
Manual 26659
ProAct P-Series FL Position Controller
Woodward
11
Typically, in a linkage system, there are links and levers that are supported by
customer-supplied bearings. However, there is often a section of the linkage
where the mass is supported fully by the actuator output shaft. When designing
linkage systems, please note that each ProAct P-Series FL actuator output shaft
accepts 1.2 kg (2.6 lb) of additional mass at a maximum vibration level of 10 G's.
Exceeding the allowable mass or vibration level may damage the actuator rotor
system and shorten actuator life.
Actuator levers are available from Woodward, which allow adjustment of the rod
end locations with respect to the center of the actuator shaft. The lever used
must have a 0.625-36 serration.
Adjust the location of the rod end on the lever to achieve the desired actuator
rotation between minimum and maximum positions. The linkage should be set to
use as much of the 75 degrees as possible (60 degrees minimum). To increase
the amount of actuator rotation, move the rod end closer to the actuator shaft or
farther away from the shaft controlling the fuel flow. To decrease the amount of
actuator rotation, move the rod end farther from the actuator shaft or closer to the
shaft controlling the fuel flow.
GAS ENGINE STOPS—Fuel gas valves and butterfly valves in
carburetors often bind if rotated too far toward minimum or
maximum. For this reason, the stops in the ProAct P-Series FL
actuator should be used at both minimum and maximum positions.
Note that the actuator internal stops allow up to 1.5 degrees of
additional rotation in both directions during impact (see Figure 2-1).
The engine must always shut down when the actuator is at the
minimum stop.
Electrical Installation
A wiring Diagram for the ProAct P-Series FL actuator is shown in Figure 2-2.
Typical connections to external devices are also shown. Prior to installation, refer
to the wiring diagram and the representative I/O interfaces schematic in this
chapter. Also, review the hardware I/O specifications in the Appendix.
All input and output signals run through an M12 and/or an M16 threaded port,
using cable glands and/or conduit as needed to maintain the Class I, Division 2
and Type 3R Enclosure Rainproof (see Regulatory Compliance). The following
section provides a description for every pin and the electrical requirements. For
functional descriptions see Chapter 3, Description of Operation.
Shielded Wiring
The use of cable with individually shielded-twisted pairs is required where
indicated by the actuator wiring diagram (Figure 2-2). Cable shields must be
terminated as indicated in the actuator wiring diagram, and following the
installation notes below. DO NOT attempt to directly ground the shield at both
ends since an undesired ground loop condition may occur.
NOTE
—The P-Series
FL actuator CAN shield connection pin is through a high-frequency capacitor only
(not directly grounded), therefore it may be grounded directly at the opposite end.
Содержание ProAct P Series FL
Страница 10: ...ProAct P Series FL Position Controller Manual 26659 viii Woodward ...
Страница 15: ...Manual 26659 ProAct P Series FL Position Controller Woodward 5 Figure 1 1 ProAct P Series FL Outline Drawing ...
Страница 23: ...Manual 26659 ProAct P Series FL Position Controller Woodward 13 Figure 2 2a Actuator Wiring Diagram ...
Страница 24: ...ProAct P Series FL Position Controller Manual 26659 14 Woodward Figure 2 2b Actuator Wiring Diagram Notes ...
Страница 79: ...Manual 26659 ProAct P Series FL Position Controller Woodward 69 Figure 6 8 Strip Chart Properties Window ...
Страница 108: ...ProAct P Series FL Position Controller Manual 26659 98 Woodward Declarations ...
Страница 109: ...Manual 26659 ProAct P Series FL Position Controller Woodward 99 ...