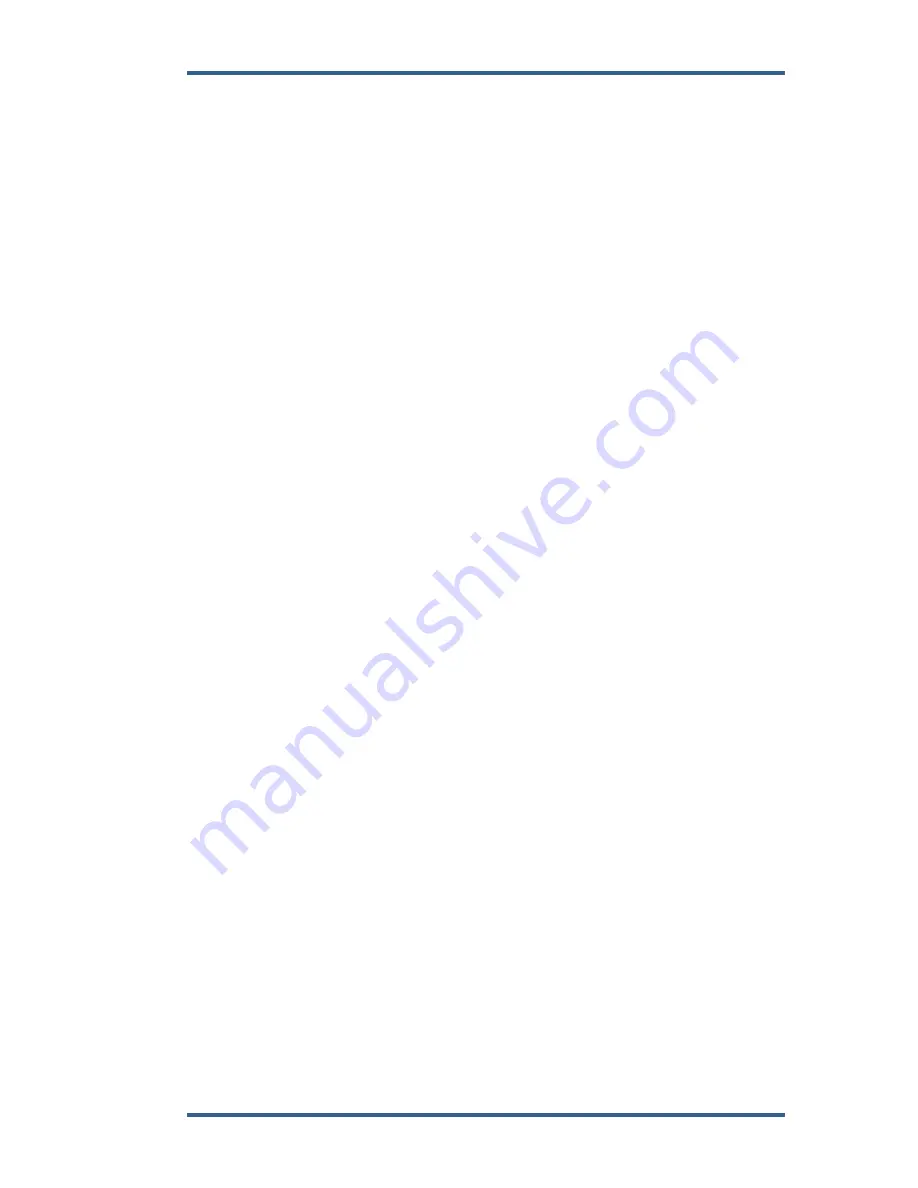
Manual 26659
ProAct P-Series FL Position Controller
Woodward
9
Mounting the ProAct P-Series FL with an ITB
The ProAct ITBs with model II actuators are designed to be mounted on the
valve flange. However, the end-user may also want to support the actuator to
minimize the loads on their piping. The ProAct ITBs with model III and model IV
actuators are designed to be base-mounted due to the higher mass of the
actuator and the increased lever arm between the center of the bore and the
center of gravity. Flange mounting of model III may be allowed, but the vibration
level must be assessed in order to ensure a low level of stress on the
component.
Refer to the ITB manual for mounting details.
ProAct P-Series FL Grounding
The ProAct P-Series FL must be grounded to the engine structure through a low-
impedance connection in order to ensure proper EMC performance. This may be
accomplished through the mechanical mounting of the actuator/throttle itself
(preferred), or through a wired connection to a designated ground screw on the
unit. If a wired connection is used as the primary EMC ground, it must be through
a low-impedance wire or strap < 30 cm (12 inches) in length, 3 mm² (12 AWG)
minimum. See Figure 1-1 for the ground screw location on each model.
Output Shaft
The ProAct P-Series FL has 73° to 77° of available travel. The max fuel direction
of this travel is software configurable in the clockwise or counterclockwise
direction through the Service Tool.
Mechanical Stops
Internal mechanical actuator stops will only survive a maximum kinetic energy of
0.011 J (0.097 in-lb). If the actuator internal stops are used, the load inertia
should not exceed 4.25E-4 kg-m² (3.76E-3 in-lb-s²). In service, electrical and
engine stops should be set inside the actuator stops. Electrical stops are set via
the Service Tool.
Fuel Position Stops
Diesel Stops
—Diesel installations generally use the fuel system minimum and
maximum position stops. Diesel engine racks are normally designed to provide the
minimum and maximum stops without binding. The actuator's stops must not prevent
the actuator from driving the fuel linkage to the minimum and maximum positions.
The linkage should be designed to use as much actuator travel as possible, without
preventing minimum and maximum fuel positions (see Figure 2-1).
Gas Engine Stops
—Fuel gas valves and butterfly valves in carburetors often
bind if rotated too far toward minimum or maximum. For this reason, the stops in
the ProAct P-Series FL actuator should be used at both minimum and maximum
positions. Note that the actuator internal stops allow up to 1.5 degrees of
additional rotation in both directions during impact (see Figure 2-1). The engine
must always shut down when the actuator is at the minimum stop.
Содержание ProAct P Series FL
Страница 10: ...ProAct P Series FL Position Controller Manual 26659 viii Woodward ...
Страница 15: ...Manual 26659 ProAct P Series FL Position Controller Woodward 5 Figure 1 1 ProAct P Series FL Outline Drawing ...
Страница 23: ...Manual 26659 ProAct P Series FL Position Controller Woodward 13 Figure 2 2a Actuator Wiring Diagram ...
Страница 24: ...ProAct P Series FL Position Controller Manual 26659 14 Woodward Figure 2 2b Actuator Wiring Diagram Notes ...
Страница 79: ...Manual 26659 ProAct P Series FL Position Controller Woodward 69 Figure 6 8 Strip Chart Properties Window ...
Страница 108: ...ProAct P Series FL Position Controller Manual 26659 98 Woodward Declarations ...
Страница 109: ...Manual 26659 ProAct P Series FL Position Controller Woodward 99 ...