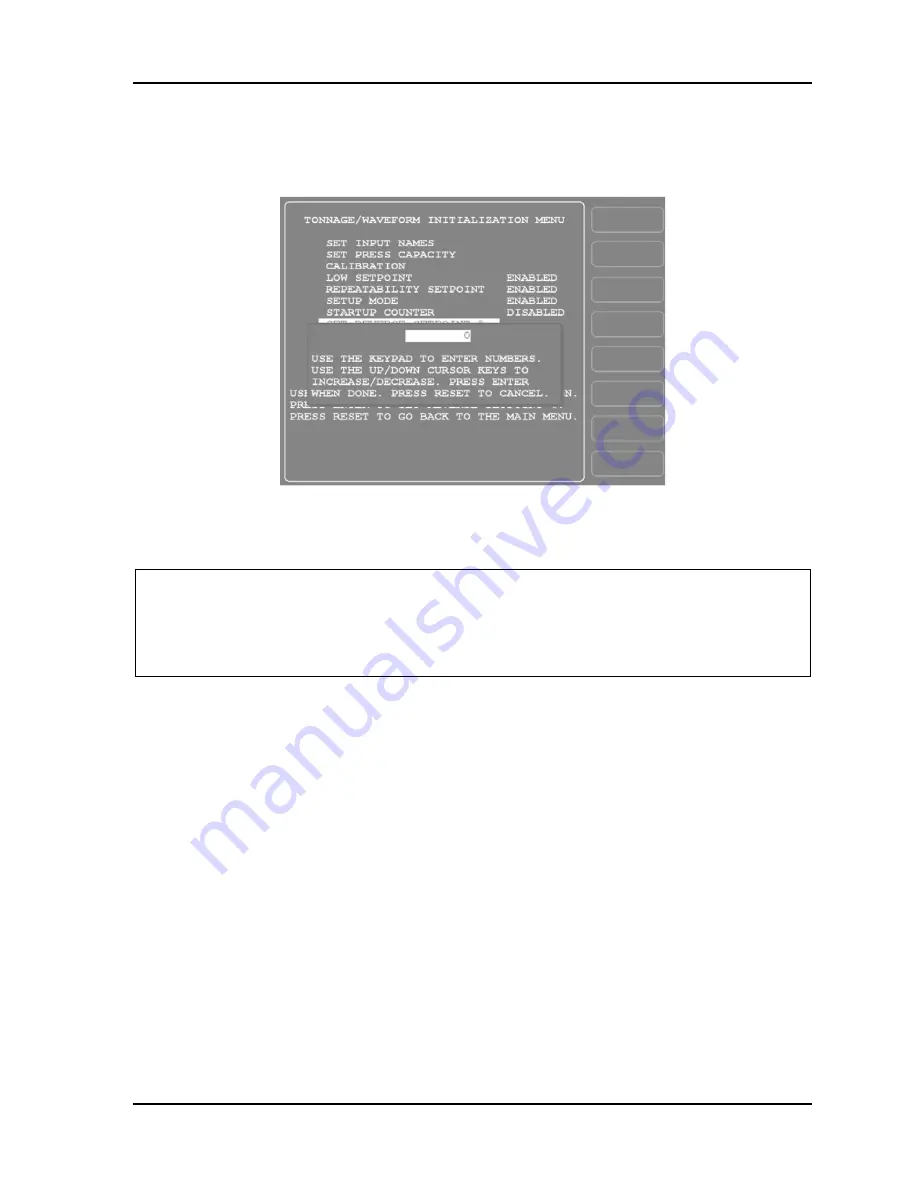
AutoSetPAC User Manual
1101600
Chapter 3 Initialization and Calibration
69
To set the reverse tonnage setpoint percentage, do the following:
1.
Select “SET REVERSE SETPOINT %.” When the Numeric Entry window (see Figure 3-8)
displays, key in the desired percentage value, following the directions in the window.
Figure 3-8.
Numeric Entry Window Superimposed on Tonnage Monitor Initialization Menu
2.
Press ENTER to confirm your entry, or press RESET to cancel.
NOTICE
YOU CANNOT DISABLE REVERSE SETPOINT %
Reverse Setpoint % cannot be disabled. The default for this setting is 20%. However, we
recommend that you set this value according to the specifications for your press.
Locking Run Mode Actions
You can prevent unauthorized personnel from recalculating setpoints or making adjustments to
setpoint percentages in Run mode. To do so, you “lock out” these capabilities from Run mode on the
Security Access Menu and remove the “Program/Run” key when SmartPAC is switched to Run
mode. When setpoint recalculation and adjustment capabilities are locked out of Run mode, they are
still functional in Program mode.
To “lock out” one or both of these actions in Run mode, do the following:
1.
Select “SECURITY ACCESS” on the Main Initialization Menu (see Figure 3-2). A screen like
the one shown in Figure 3-9 displays. (The items on your menu may differ depending on installed
options.) Note that the LOAD MONITOR item shown in Figure 3-9 is set to “ALLOW
RECALC/ADJUST,” a setting that allows the operator to recalculate and adjust setpoints in Run
mode. This is the factory setting.
Содержание AutoSet PAC 120 VAC
Страница 2: ......
Страница 4: ......
Страница 6: ......
Страница 12: ...12 Table of Contents ...
Страница 14: ...14 ...
Страница 16: ...16 ...
Страница 18: ...18 ...
Страница 28: ...1101600 AutoSetPAC User Manual 28 Chapter 1 Installation ...
Страница 106: ...1101600 AutoSetPAC User Manual 106 Chapter 4 Using AutoSetPAC in Program Mode ...
Страница 122: ...1101600 AutoSetPAC User Manual 122 Chapter 5 Using AutoSetPAC in Run Mode Figure 5 18 Tool Loading Message ...
Страница 133: ......
Страница 134: ......
Страница 135: ......
Страница 136: ......
Страница 137: ......
Страница 138: ......
Страница 139: ......
Страница 140: ......
Страница 141: ......
Страница 142: ......
Страница 143: ......
Страница 144: ......
Страница 145: ......
Страница 146: ......
Страница 147: ......
Страница 148: ......
Страница 149: ......
Страница 150: ......
Страница 151: ......
Страница 152: ......
Страница 153: ......
Страница 154: ......
Страница 155: ......
Страница 156: ......