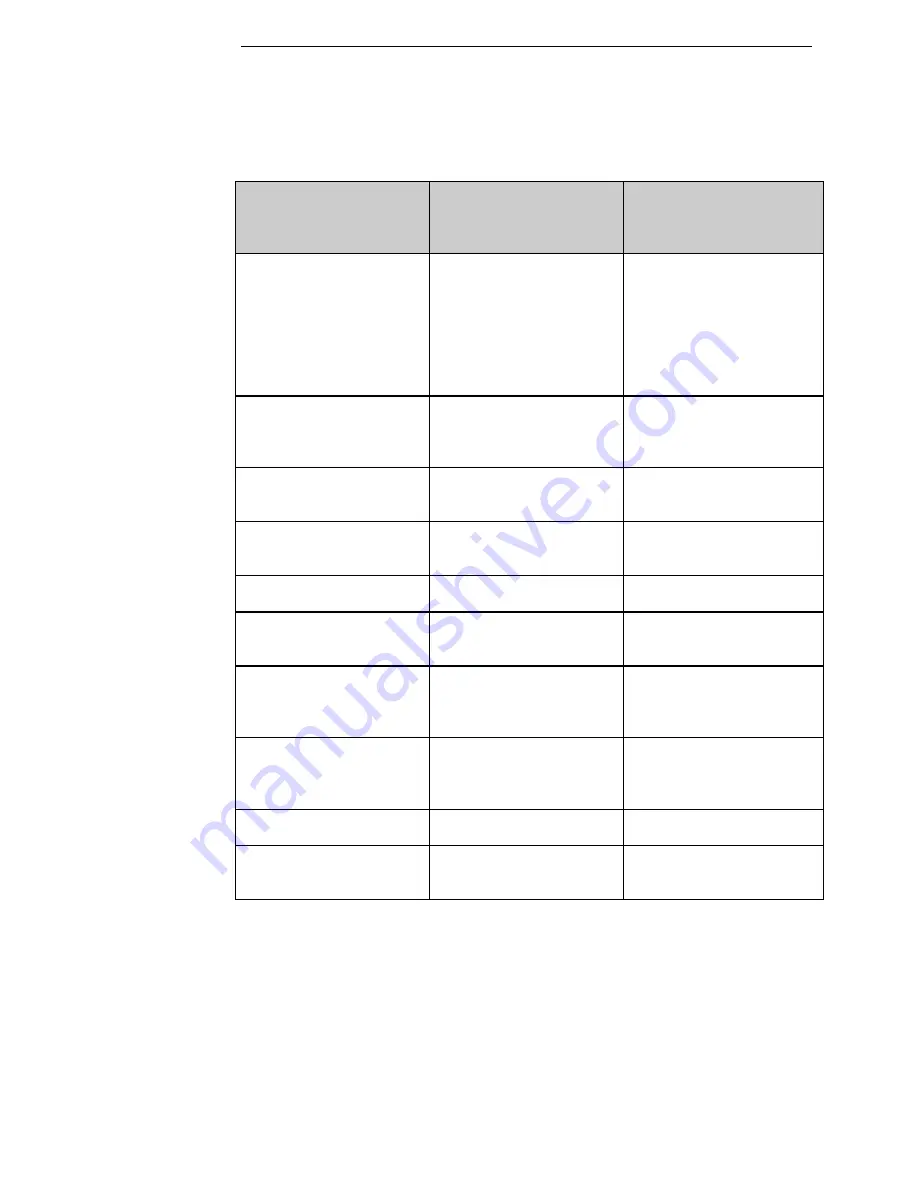
Strasbaugh
Table of Contents
Version 4.0 - February 1998
xix
Feature
Menu(s)
Where to Find Details -
Manual Location(s)
Programmable Pad
Conditioning Arm
Calibration and Setup
Calibration/Configuration
Menu
Sweep Parameters Menu
Manual Control Menu
Operations:
v
Ch. 4-Machine Setup
Maintenance:
v
Ch. 9-Mechanical
Maintenance:
v
Ch. 10-Software Calibration
v
Appendix A-Calibration
Variables
Polish and Condition Force
Units and Diameter Entry
Change
Machine Parameters Menu
Conditioning/Cleaning
Parameters Menu
Operations:
v
Ch. 4-Machine Setup
Menu "Hopping "
Available at All Menus
Operations:
v
Ch. 3-Operator Functions
(topic: Menu Selection)
"On the Fly Changes"
Auto Polish Menu
Process Parameters Menus
Operations:
v
Ch. 3-Operator Functions
v
Ch. 4-Machine Setup
Auto Cycle Features
Auto Polish Menu
Operations:
v
Ch. 3-Operator Functions
Manual Control Menu
Manual Control Menu
Maintenance:
v
Ch. 9-Mechanical
v
Ch. 10-Software Calibration
Servo Calibration
Manual Control Menu
Calibration/Configuration
Menu
Diagnostics Menu
Maintenance:
v
Ch. 9-Mechanical
v
Ch. 10-Software Calibration
Lever Type Conditioning
Arm Support
Calibration/Configuration
Menu
Maintenance:
v
Ch. 10-Software Calibration
v
Appendix A-Calibration
Variables
Single Sweep Style Choice
Conditioning/Cleaning Menu
Operations:
v
Ch. 4-Machine Setup
Wet Idle Slurry Flush
Machine Parameters Menu
Slurry Flush Menu
Operations:
v
Ch. 3-Operator Functions
v
Ch. 4-Machine Setup
Содержание 6DS-SP
Страница 1: ......
Страница 4: ...Copyright 1998 by Strasbaugh All rights reserved Document prepared by Technical Publications Group...
Страница 19: ...Introduction INTRODUCTION...
Страница 58: ......
Страница 59: ...Introduction ACHINE ESCRIPTION...
Страница 108: ...Introduction PERATOR UNCTIONS...
Страница 131: ...Strasbaugh Operator Functions Version 4 0 February 1998 3 23 Figure 3 4 Menu Selection...
Страница 134: ...Operations Model 6DS SP Planarizer 3 26 Version 4 0 February 1998 Figure 3 5 Home Machine Menu...
Страница 145: ...Strasbaugh Operator Functions Version 4 0 February 1998 3 37 Figure 3 8 Recipe Management Menu...
Страница 150: ...Operations Model 6DS SP Planarizer 3 42 Version 4 0 February 1998 Figure 3 9 Home Machine Menu...
Страница 153: ...Strasbaugh Operator Functions Version 4 0 February 1998 3 45 Figure 3 10 Auto Polish Cycle Menu...
Страница 166: ...Operations Model 6DS SP Planarizer 3 58 Version 4 0 February 1998 Figure 3 11 Slurry Flush Menu...
Страница 202: ...Operations Model 6DS SP Planarizer 3 94 Version 4 0 February 1998 This page intentionally left blank...
Страница 203: ...Introduction ACHINE ETUP...
Страница 210: ...Strasbaugh Machine Setup Version 4 0 February 1998 4 7 Figure 4 2 Slurry Flush Menu...
Страница 213: ...Operations Model 6DS SP Planarizer 4 10 Version 4 0 February 1998 Figure 4 3 Recipe Management Menu...
Страница 216: ...Strasbaugh Machine Setup Version 4 0 February 1998 4 13 Figure 4 4 Polish Parameters Menu...
Страница 223: ...Operations Model 6DS SP Planarizer 4 20 Version 4 0 February 1998 Figure 4 5 Sweep Parameters Menu...
Страница 236: ...Strasbaugh Machine Setup Version 4 0 February 1998 4 33 Figure 4 8 Machine Parameters Menu Screen Page 1...
Страница 239: ...Operations Model 6DS SP Planarizer 4 36 Version 4 0 February 1998 Figure 4 9 Machine Parameters Menu Screen Page 2...
Страница 242: ...Strasbaugh Machine Setup Version 4 0 February 1998 4 39 Figure 4 10 Machine Parameters Menu Screen Page 3...
Страница 247: ...Operations Model 6DS SP Planarizer 4 44 Version 4 0 February 1998 Figure 4 11 Alarm Parameters Menu...
Страница 251: ...Operations Model 6DS SP Planarizer 4 48 Version 4 0 February 1998 Figure 4 12 Machine Setup Menu...
Страница 254: ...Strasbaugh Machine Setup Version 4 0 February 1998 4 51 Figure 4 13 Password Menu...
Страница 257: ...Operations Model 6DS SP Planarizer 4 54 Version 4 0 February 1998 This page intentionally left blank...
Страница 258: ...Introduction TROUBLESHOOTING...
Страница 267: ...Strasbaugh Troubleshooting Version 4 0 February 1998 5 9 Figure 13 1 Alarm Log Menu...
Страница 326: ...Introduction APPENDICES...
Страница 328: ...Operations Model 6DS SP Planarizer Version 4 0 February 1998 This page intentionally left blank...
Страница 329: ...Introduction LECTRIAL NPUT UTPUT...
Страница 331: ...Operations Model 6DS SP Planarizer This page intentionally left blank...
Страница 332: ......
Страница 335: ...Copyright 1998 by Strasbaugh All rights reserved Document prepared by Technical Publications Group...
Страница 355: ...Maintenance Model 6DS SP Planarizer xxii Version 4 0 February 1998 This page intentionally left blank...
Страница 356: ...Introduction REVISIONS...
Страница 357: ...Introduction INTRODUCTION...
Страница 395: ...Maintenance Model 6DS SP Planarizer 1 38 U Version 4 0 February 1998 Update 10 19 01 GUARANTEE WARRANTY CERTIFICATE...
Страница 396: ......
Страница 407: ...Strasbaugh Installation Version 4 0 February 1998 Update 11 06 01 2 11 U...
Страница 420: ...Maintenance Model 6DS SP Planarizer 2 24 U Version 4 0 February 1998 Update 11 06 01 This page intentionally left blank...
Страница 421: ...Introduction HYSICAL ESCRIPTION...
Страница 444: ...Introduction ECHANICAL ESCRIPTION...
Страница 462: ...Maintenance Model 6DS SP Planarizer 4 18 Version 4 0 February 1998 This page intentionally left blank...
Страница 463: ...Introduction CONTROL SYSTEM DESCRIPTION...
Страница 470: ...Introduction OWER ISTRIBUTION...
Страница 478: ...Maintenance Model 6DS SP Planarizer 6 8 Version 4 0 February 1998 This page intentionally left blank...
Страница 479: ...Introduction LUMBING ESCRIPTION...
Страница 489: ...Maintenance Model 6DS SP Planarizer 7 10 Version 4 0 February 1998 This page intentionally left blank...
Страница 490: ...Introduction REVENTATIVE AINTENANCE CHEDULES...
Страница 507: ...Introduction ECHANICAL AINTENANCE ROCEDURES...
Страница 516: ......
Страница 520: ...Maintenance Model 6DS SP Planarizer 9 12 Version 4 0 February 1998 Figure 9 7 Retainer Clamp Ring...
Страница 690: ...Maintenance Model 6DS SP Planarizer 9 182 Version 4 0 February 1998 This page intentionally left blank...
Страница 691: ...Introduction OFTWARE ALIBRATION ROCEDURES...
Страница 703: ...Maintenance Model 6DS SP Planarizer 10 12 Version 4 0 February 1998 Figure 10 2 Manual Control Menu Screen Page 1...
Страница 707: ...Maintenance Model 6DS SP Planarizer 10 16 Version 4 0 February 1998 Figure 10 3 Manual Control Menu Screen Page 2...
Страница 710: ...Strasbaugh Software Calibration Procedures Version 4 0 February 1998 10 19 Figure 10 4 Manual Control Menu Screen Page 3...
Страница 713: ...Maintenance Model 6DS SP Planarizer 10 22 Version 4 0 February 1998 Figure 10 5 Diagnostics Menu...
Страница 716: ...Strasbaugh Software Calibration Procedures Version 4 0 February 1998 10 25 Figure 10 6 Calibration Configuration Menu...
Страница 862: ...Introduction NEUMATIC DJUSTMENTS...
Страница 897: ...Introduction OFTWARE ONTROL OMPUTER AINTENANCE...
Страница 912: ...Introduction TROUBLESHOOTING...
Страница 921: ...Strasbaugh Troubleshooting Version 4 0 February 1998 13 9 Figure 13 1 Alarm Log Menu...
Страница 980: ...Maintenance Model 6DS SP Planarizer 13 68 Version 4 0 February 1998 This page intentionally left blank...
Страница 981: ......
Страница 984: ...Copyright 1998 by Strasbaugh All rights reserved Document prepared by Technical Publications Group...
Страница 1004: ...Maintenance Model 6DS SP Planarizer xxii Version 4 0 February 1998 This page intentionally left blank...
Страница 1005: ...Introduction APPENDICES...
Страница 1006: ...Introduction ALIBRATION ARIABLES IST...
Страница 1008: ...Maintenance Model 6DS SP Planarizer This page intentionally left blank...
Страница 1071: ...STRASBAUGH INC 6DS SP User Interface Reference May 31 2001 Ver 4 37 This page intentionally left blank...
Страница 1073: ...STRASBAUGH INC 6DS SP User Interface Reference May 31 2001 Ver 4 37 This page intentionally left blank...
Страница 1082: ...STRASBAUGH INC May 31 2001 Ver 4 37 6DS SP User Interface Reference Page 9 This page intentionally left blank...
Страница 1086: ...STRASBAUGH INC May 31 2001 Ver 4 37 6DS SP User Interface Reference Page 13 This page intentionally left blank...
Страница 1094: ...STRASBAUGH INC May 31 2001 Ver 4 37 6DS SP User Interface Reference Page 21...
Страница 1103: ...STRASBAUGH INC Page 30 6DS SP User Interface Reference May 31 2001 Ver 4 37...
Страница 1105: ...STRASBAUGH INC Page 32 6DS SP User Interface Reference May 31 2001 Ver 4 37 Continued on next page...
Страница 1111: ...STRASBAUGH INC Page 38 6DS SP User Interface Reference May 31 2001 Ver 4 37 This page intentionally left blank...
Страница 1115: ...STRASBAUGH INC Page 42 6DS SP User Interface Reference May 31 2001 Ver 4 37 This page intentionally left blank...
Страница 1119: ...STRASBAUGH INC Page 46 6DS SP User Interface Reference May 31 2001 Ver 4 37 This page intentionally left blank...
Страница 1123: ...STRASBAUGH INC Page 50 6DS SP User Interface Reference May 31 2001 Ver 4 37 This page intentionally left blank...
Страница 1467: ...Introduction SSEMBLY RAWINGS...
Страница 1468: ...Strasbaugh Appendices Version 4 0 February 1998 Appendix B Engineering Drawings bound under separate cover Customer Parts Lists...
Страница 1469: ...Maintenance Model 6DS SP Planarizer This page intentionally left blank...
Страница 1470: ...Introduction ARTS IST...
Страница 1471: ...Introduction LECTRICAL NPUT UTPUT...
Страница 1473: ...Maintenance Model 6DS SP Planarizer This page intentionally left blank...
Страница 1474: ...Introduction PTIONS...
Страница 1476: ...Strasbaugh Appendices Version 4 0 February 1998 Appendix D Options...
Страница 1477: ...Maintenance Model 6DS SP Planarizer This page intentionally left blank...
Страница 1478: ...Introduction AINTENANCE OG HEETS...
Страница 1479: ...Strasbaugh Appendices Version 4 0 February 1998 Appendix E Maintenance Log Sheets...
Страница 1480: ...Maintenance Model 6DS SP Planarizer This page intentionally left blank...
Страница 1481: ......
Страница 1482: ......
Страница 1483: ......
Страница 1484: ......
Страница 1485: ......
Страница 1507: ...Maintenance Model 6DS SP Planarizer xxii Version 4 0 February 1998 This page intentionally left blank...
Страница 1508: ...Introduction APPENDICES...
Страница 1509: ...Strasbaugh Appendices Version 4 0 February 1998 Appendix F Manufacturer Data Attached CD...
Страница 1510: ...Maintenance Model 6DS SP Planarizer This page intentionally left blank...
Страница 1511: ......
Страница 1533: ...Maintenance Model 6DS SP Planarizer xxii Version 4 0 February 1998 This page intentionally left blank...
Страница 1534: ...Introduction APPENDICES...
Страница 1535: ...Strasbaugh Appendices Version 4 0 February 1998 Appendix F Part 2 Manufacturers Data Sheets...
Страница 1536: ...Maintenance Model 6DS SP Planarizer This page intentionally left blank...
Страница 1537: ......
Страница 1559: ...Maintenance Model 6DS SP Planarizer xxii Version 4 0 February 1998 This page intentionally left blank...
Страница 1560: ...Introduction APPENDICES...
Страница 1561: ...Strasbaugh Appendices Version 4 0 February 1998 Appendix F Part 3 Manufacturers Data Sheets Go to Manufacturer Data...
Страница 1562: ...Maintenance Model 6DS SP Planarizer This page intentionally left blank...