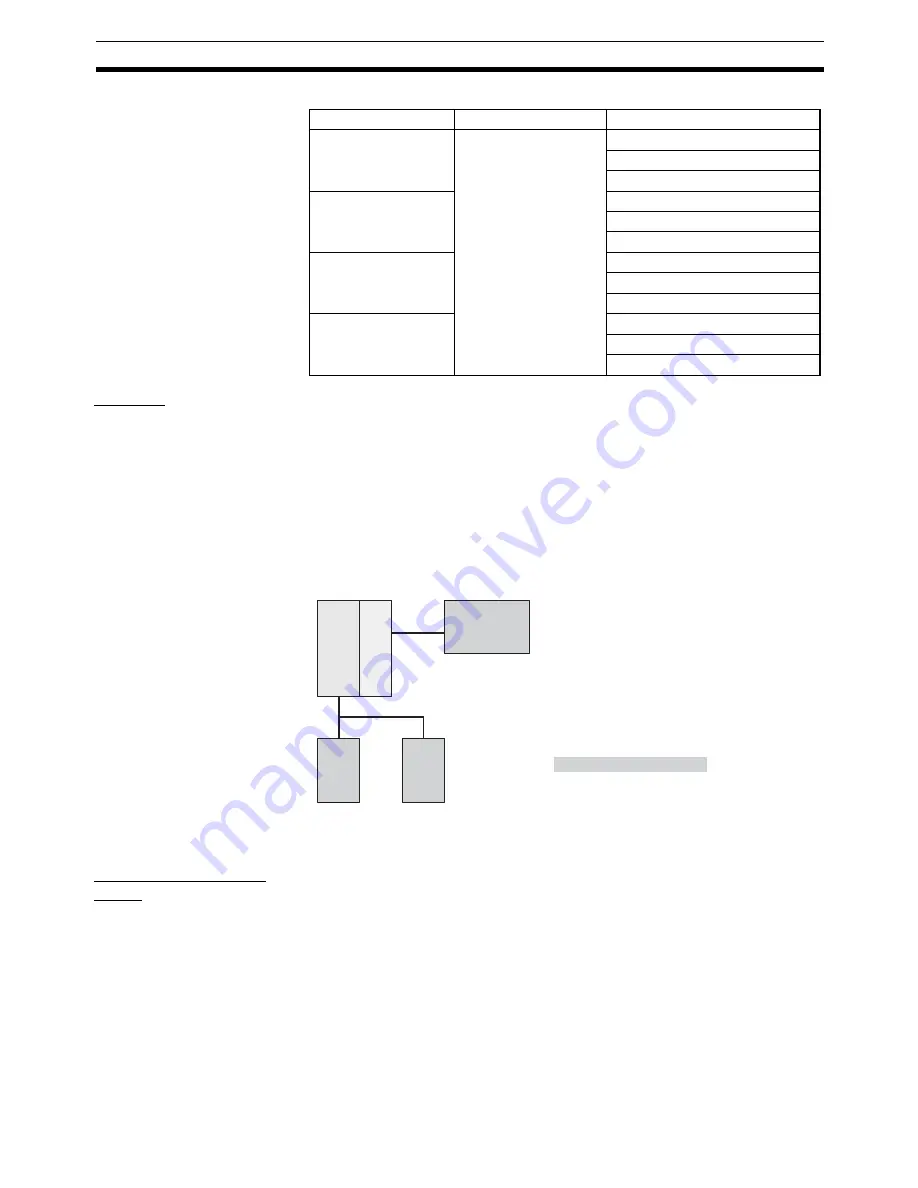
57
Other Functions
Section 4-5
Settings
The G3ZA settings are read and written through the Basic Unit.
The Basic Unit has addresses allocated in its variable area for use with the
G3ZA. The G3ZA set values can be read and written by reading and writing
that variable area. Refer to Parameter List on page 175 for details on the vari-
able area for the G3ZA. Refer to the G3ZA Multi-channel Power Controller
User’s Manual (Cat. No. Z200) for details on the corresponding functions and
settings.
■
Example
In this example, G3ZA settings are changed.
Sending MVs to the
G3ZA
The G3ZA's unit number and model determine which MVs are sent from the
EJ1G to the G3ZA.
G3ZA Models with 4
Channels
The EJ1G uses the G3ZA's unit number to determine whether to send heating
outputs or cooling outputs.
Unit number
Variable type
Parameter name
0
DA/9A
G3ZA1 - CH1 Slope
G3ZA1 - CH1 2 Slope
···
1
G3ZA2 - CH1 Slope
G3ZA2 - CH1 2 Slope
···
3
G3ZA3 - CH1 Slope
G3ZA3 - CH1 2 Slope
··
·
5
G3ZA4 - CH1 Slope
G3ZA4 - CH1 2 Slope
···
TC4
EDU
Host device
G3ZA
G3ZA
Unit No. 1
Unit No. 0
Unit No. 1
[STX]0100001029A0219000001000A[ETX][BCC]
Send the following command from the host device
to TC4 when setting the Channel 2 Heater
Burnout Detection Value to 10 A in the G3ZA with
unit number 1.
Содержание EJ1G
Страница 1: ...USER S MANUAL Modular Temperature Controllers for Gradient Temperature Control EJ1G Cat No H143 E1 01 ...
Страница 3: ...iv ...
Страница 17: ...xviii ...
Страница 21: ...xxii ...
Страница 53: ...32 Unit Configuration Examples Section 2 4 ...
Страница 69: ...48 Changing SPs During Operation Section 3 3 ...
Страница 81: ...60 Other Functions Section 4 5 ...
Страница 145: ...124 Other HFU Functions Section 5 7 ...
Страница 167: ...146 Detailed Description of Services Section 6 4 ...
Страница 189: ...168 Determining the Error from the Current Situation for Heater Burnout Alarm Errors Section 7 8 ...
Страница 229: ...208 Parameters That Can Be Allocated for Programless Communications Appendix ...
Страница 237: ......