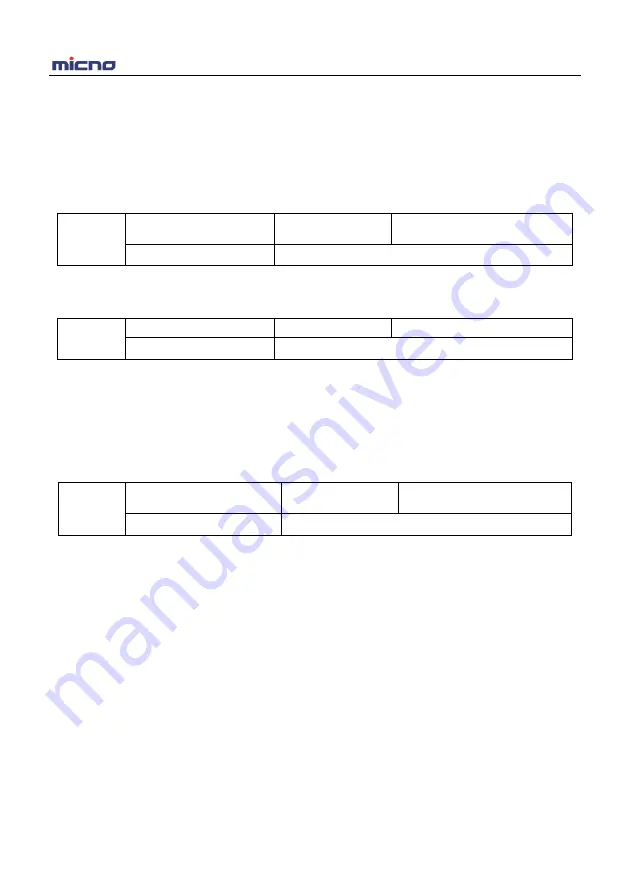
KE300A Inverter Parameter Description
89
If factory default cannot meet the requirements, the relevant parameter values can be subject to fine
tuning.
Increase the proportional gain while ensuring no oscillation to the system, and then reduce the integration
time to ensure that the system has quick response characteristics and small overshoot.
Caution: Improper PI parameter setting may cause too large speed overshoot. Voltage fault may
occur when the overshoot drops.
P2-06
Vector control slip
compensation coefficient
Factory default
100%
Setting range
50% ~ 200%
For sensorless vector control, this parameter is used to adjust the speed stabilizing precision of the motor.
When the speed is too low due to heavy load of motor, this parameter needs to be enlarged, vice versa.
P2-07
Speed loop filter time
Factory default
0.000s
Setting range
0.000s ~ 0.100s
Under vector control mode, the output of speed loop regulator is torque current command. This parameter
is used to filter the torque command. This parameter needs no adjustment generally and this filter time can
be increased in case of huge speed fluctuation. In case of oscillation of motor, this parameter should be
reduced properly.
The speed loop filter time is low, and the inverter output torque may fluctuate greatly, but the response is
quick.
P2-08
Vector control over excitation
gain
Factory default
64
Setting range
0 ~ 200
During deceleration, over excitation control can suppress bus voltage increase, avoid over voltage fault.
The bigger over excitation gain is, the better the suppression result is.
For the application which over voltage fault happens frequently during deceleration, the over excitation
gain needs to be increased. But the current would be increased if the over excitation is too bigger, so you
need to set the suitable over excitation gain.
For the small inertia situation, voltage doesn’t increase during motor deceleration, please set over
excitation gain to 0. For the application with braking resistor, please also set over excitation gain to 0.