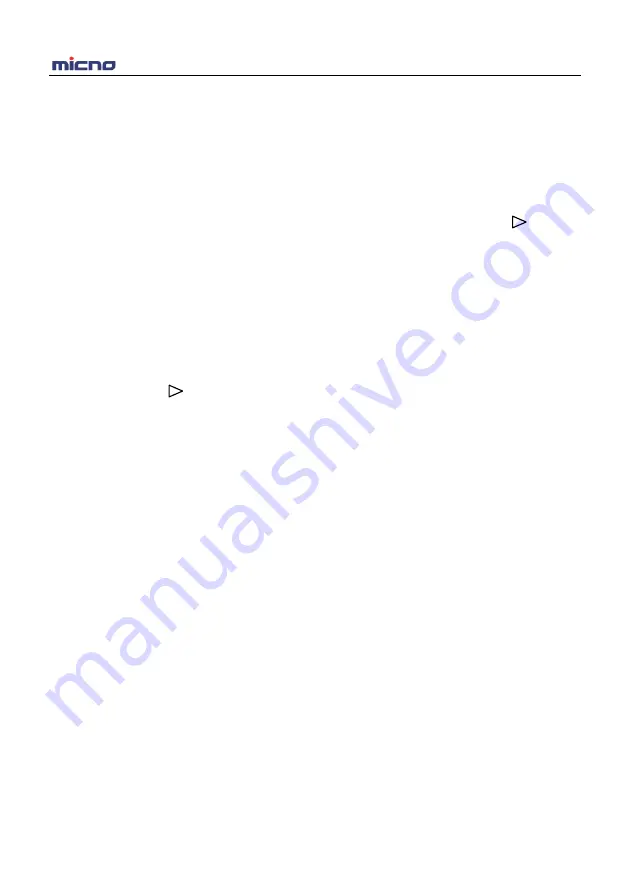
KE300A Inverter Operation and Display
46
4.5 Stand By
In stop or stand by status, parameters of multi-status can be displayed. Whether or not to display this
parameter can be chosen through function code P7-05 (Stop status display parameter) according to binary
bits.
In stop status, there are thirteen parameters can be chosen to display or not. They are: setting frequency,
bus voltage, DI input status, DO output status, analog input AI1 voltage, analog input Al2 voltage, radiator
temperature, count value, actual length, PLC running step, load speed display, PID setting, HDI input pulse
frequency. The displaying of the chosen parameters can be switched in sequence by press “ ” button.
Power on after power-off, the displayed parameters would be default considered as the chosen parameters
before power-off.
4.6 Running
In running status, there are thirty two parameters can be chosen to display or not through function code
P7-04 (running status display parameter 2) according to binary bits. They are: running frequency, setting
frequency, DC bus voltage, output voltage, output current, output torque, DI input status, DO output status,
analog input AI1 voltage, analog input AI2 voltage, radiator temperature, actual count value, actual length,
line speed, PID setting, PID feedback, etc. The displaying of the chosen parameters can be switched in
sequence by pressing “ ” button.
4.7 Password Setting
The inverter provides user password protection function. When PP-00 is set to non-zero value, it indicates
the user password, and the password protection turns valid after exiting the function code editing status.
When pressing PRG key again, “------“will be displayed, and common menu cannot be entered until user
password is input correctly.
To cancel the password protection function, enter with password and set PP-00 to “0”.
4.8 Motor Parameters Autotuning
To select the vector control running mode, it must input the nameplate parameter of the motor accurately
prior to the running of the inverter. The Inverter will select standard motor parameters matching the
nameplate parameter. Since the vector control mode relies highly on the motor parameters, it must acquire
the accurate parameters of the controlled motor to ensure the good control performance.
The procedures for the automatic tuning of motor parameters are described below:
First, select the command source (P0-02) as the command channel of the operation keypad. Second, input
the following parameters in accordance with the actual motor parameters:
P1-01: Rated motor power
P1-02: Rated motor voltage
P1-03: Rated motor current
P1-04: Rated motor frequency
P1-05: Rated rotation speed of motor
If the motor is completely disconnected from the load, set P1.11 to “2” (complete tuning), and press RUN
key on the keyboard keypad, then the inverter will automatically calculate the following parameters: