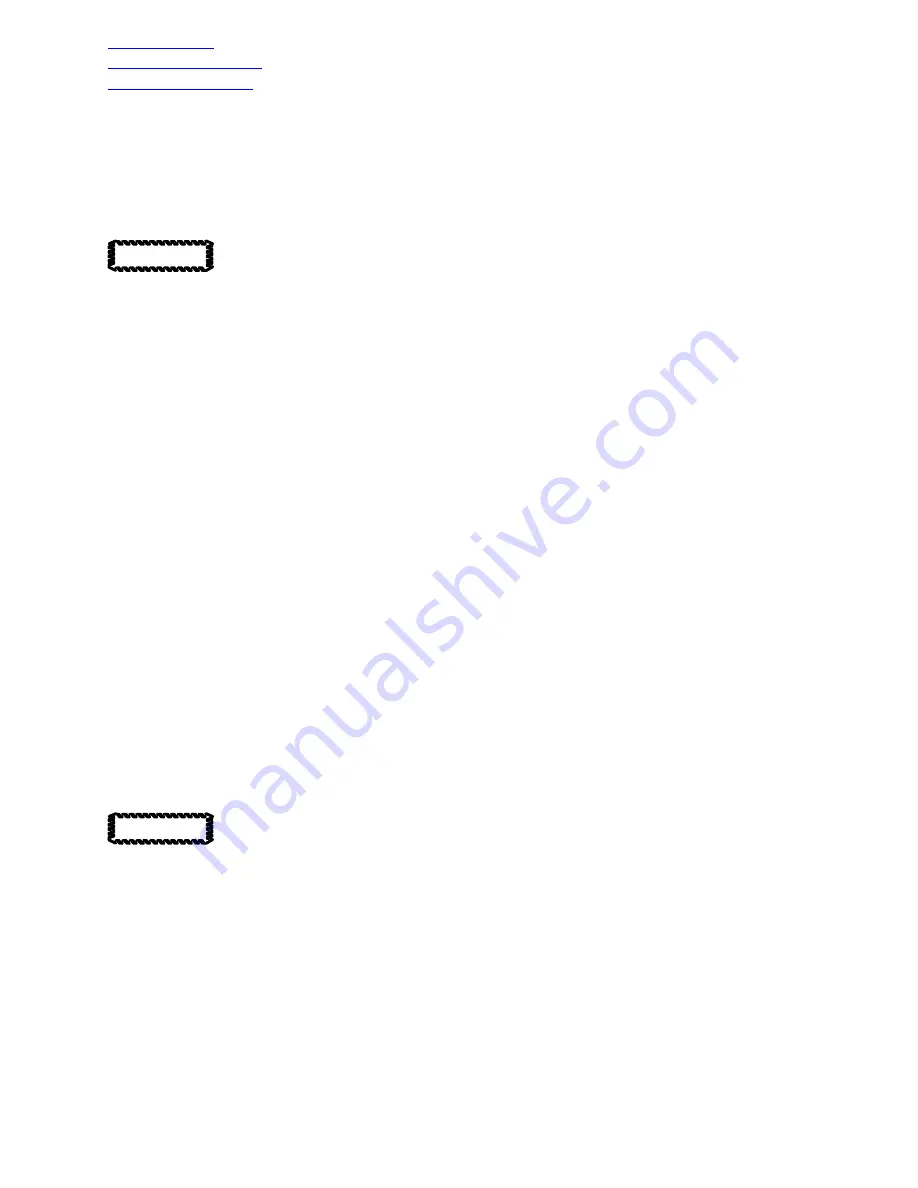
CSP-HMI-3
MD Helicopters, Inc
.
MAINTENANCE MANUAL
96-05-00
Page 207
Revision 8
The information disclosed herein is proprietary to MD Helicopters, Inc.
Neither this document nor any part hereof may be reproduced or transferred to
other documents or used or disclosed to others for manufacturing or any other
purpose except as specifically authorized in writing by MD Helicopters, Inc.
Copyright
©
1999
−
2016 by MD Helicopters, Inc.
(c). Reassemble battery components in
new base.
(d). Perform Battery Charging - Deep
Cycling Procedure.
(5). Installing Receptacle;
Comply with polarity require
ments when connecting recep
tacle bus strips and wires to receptacle. Re
versed connections may damage battery
when connected in helicopter electrical sys
tem.
(a). Using tin alloy solder (CM815),
solder two receptacle bus strips and
temperature sensing switch wires to
back of receptacle.
(b). Insert receptacle in battery case and
secure. Using lockwire (CM702),
safety nut to holes in case.
(c). Fill receptacle back and cover bus
strips with sealant (CM425). (Recep
tacle back and strips are covered to
within 0.62 inch (15.748 mm) of cell
terminals with 0.060 inch (1.524
mm) thick sealant coating.)
(d). Position connector separator inside
battery case so that open end butts
against end of case, enclosing two
receptacle bus strips and receptacle.
(e). Install nylon separator and cells.
(6). Installing Cells;
Do not intermix different man
ufacturer's cells. (Refer to bat
tery manufacturer's instructions).
(a). Use new or serviceable cell to replace
defective cell.
(b). Ensure cell is clean and position
same in battery case for correct
polarity orientation.
NOTE:
When replacing the complete set of
cells, install cells, in order - No. 1 thru No.
9; then nylon separator; No. 19, and then
No. 10 thru No. 18.
(c). Connect bus bars and strips and
secure with attaching hardware; cup
side of washer shall be down. Torque
screws to
15 - 18 inch-pounds
(1.69 - 2.03 Nm)
.
(d). Install holddown bars on case.
(e). Spray thin film of rust inhibitor
(CM232) over entire top surface of
battery and inside connector recep
tacle or coat all exposed metal parts
with petrolatum (CM114).
(f). Perform Battery Charging - Deep
Cycling Procedure before returning
battery to service.
(7). Temperature Sensing Switches Re
placement;
(a). Remove sealant covering switches
and remove switch.
(b). Install correct replacement switch in
location shown (Ref. Figure 201) and
torque to
5 - 15 inch-pounds (0.56
- 1.69 Nm)
.
(c). Install fiberglass sleeving and solder
wire connections; red wire to high
temperature switch and yellow to low
temperature switch.
(d). Cover switch connections with
(e). Ensure high temperature switch is
identified with red paint mark on bus
bar. If required, renew paint mark.
11. Battery Temperature Sensing Equipment
and Indicators
(Ref. Figure 202) Battery temperature sensing
equipment basically consists of two tempera
ture indicator light switches, two temperature
sensing switches inside the battery , intercon
necting wiring and associated attaching and
mounting hardware, The indicator light/
switches are located either in a light/switch
and horn housing or are part of a caution and
warning light assembly. The sensing equip
ment provides a means of visually monitoring
for battery over temperature with caution
(amber) and warning (red) light indicators on
the instrument panel.
CAUTION
CAUTION
Содержание 369-500
Страница 14: ......
Страница 30: ......
Страница 82: ......
Страница 94: ......
Страница 106: ......
Страница 116: ......
Страница 134: ......
Страница 150: ......
Страница 162: ......
Страница 168: ......
Страница 178: ......
Страница 226: ......
Страница 232: ......
Страница 244: ......
Страница 346: ......
Страница 416: ......
Страница 444: ......
Страница 458: ......
Страница 472: ......
Страница 490: ......
Страница 536: ......
Страница 560: ......
Страница 578: ......
Страница 604: ......
Страница 612: ......
Страница 616: ......
Страница 628: ......
Страница 654: ......
Страница 678: ......
Страница 706: ......