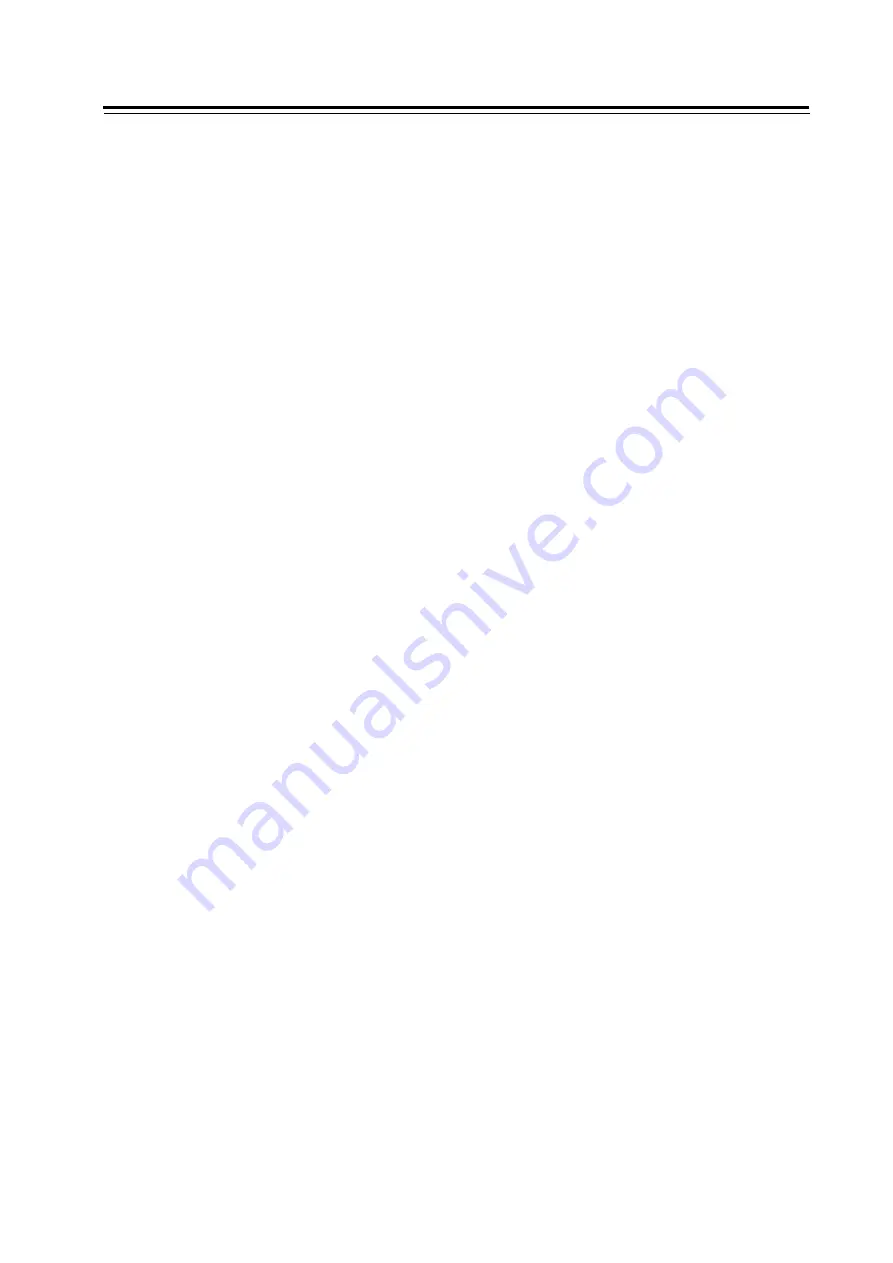
Programming Chapter Three Commands and Functions
94
Do not execute the constant surface speed control in G96 if the system adopts the
gear shifting spindle.
Note 2:
The constant surface speed control is valid only in AUTO
mode
and the system will
automatically cancel the constant surface speed control after escaping from AUTO
mode or resetting.
Note 3:
The constant surface speed control is valid in the end point in G00. Execute the constant
surface speed control anytime in G01, G02, G03.
Note 4:
Max. speed of constant surface speed control is defined by P09, P10, and min. speed
set by the system is 25 r/min.
Note 5:
The constant surface speed defined by S in the constant surface speed control is not
one after the tool compensation or the offset but the programming path.
Note 6:
The rotary axis must be positioned on Z workpiece coordinate system (X=0) in the
constant surface speed control.
Note 7:
G96 is modal. When G96 is valid, the single S
command
is taken as the new surface
speed data.
Note 8:
In DRY RUN mode, the surface speed control is valid but the single S command cannot
update the previous surface speed.
Note 9:
The constant surface speed control is valid when executing the thread cutting. Ensure
the constant surface speed control is invalid with G97 to make the spindle speed
constantly.
Note 10:
Before using the constant surface speed control, it is necessary to make sure the
current spindle speed approaches the initial speed of constant surface speed. They
must coincide with each other by tuning the spindle speed to approach the initial speed
of constant surface speed if there is big different, otherwise the spindle speed is
suddenly changed which also be caused by the big tool compensation value when the
tool compensation is modified to the coordinate mode.
3.1.13 Single Canned Cycle
It is necessary to cut repeatedly the same machining path in the course of some special roughing.
To simplify the programming, improve the programming and the machining efficiency, the canned
cycle is set. The tool will automatically return to the coordinate position before execution when
executing the canned cycle once. If the cycle is executed again, do not rewrite the cycle
commands but execute the programming of feeding data again. Return to the starting point of
cycle after executing the cycle. If other commands G, M, S, T are contained in the block behind
the cycle ones, the cycle automatically ends.
3.1.13.1 G90
—
Inner/Outer Surface Turning Cycle
Command format
:
G90 X(U) Z(W) R F ;
X
(
U
)
Z
(
W
)
—end point of cylindrical(taper) surface
,
The two axes must be given and the
incremental coordinates cannot be zero.
R—diameter difference between the starting point and the end point of cycle. It is the axis surface
cutting if R is omitted.
F—feedrate.
G90 cycle process
:
1. X rapidly moves from A to B.
2. X, Z cut at F speed from B to C (X does not move without R).
3. X cut at F speed from C to D.
4. Z rapidly moves from D to A.
The tool is still at the starting point of cycle after G90 cycle ends. If only X coordinate of end point
is defined again (or incremental coordinate U), the above-mentioned cycle is repeated according
to the new X (U) coordinate value.
When using the incremental coordinates, U sign is defined by X from A to B, and W sign is
defined by Z from B to C.
Содержание GSK928TE
Страница 1: ...GSK928TE II Turning Machine CNC System User Manual...
Страница 117: ...Programming Chapter Three Commands and Functions 112 G99 G01 X50 Z30 F0 2 G04 D2 G99 G01 X50 Z30 F0 2...
Страница 148: ...GSK928TE Turning CNC System User Manual 143 Connection Chapter One Interface 1 1 Interface Layout...
Страница 185: ...Connection Appendix 180 J3 1 AC220V J3 2 0V...