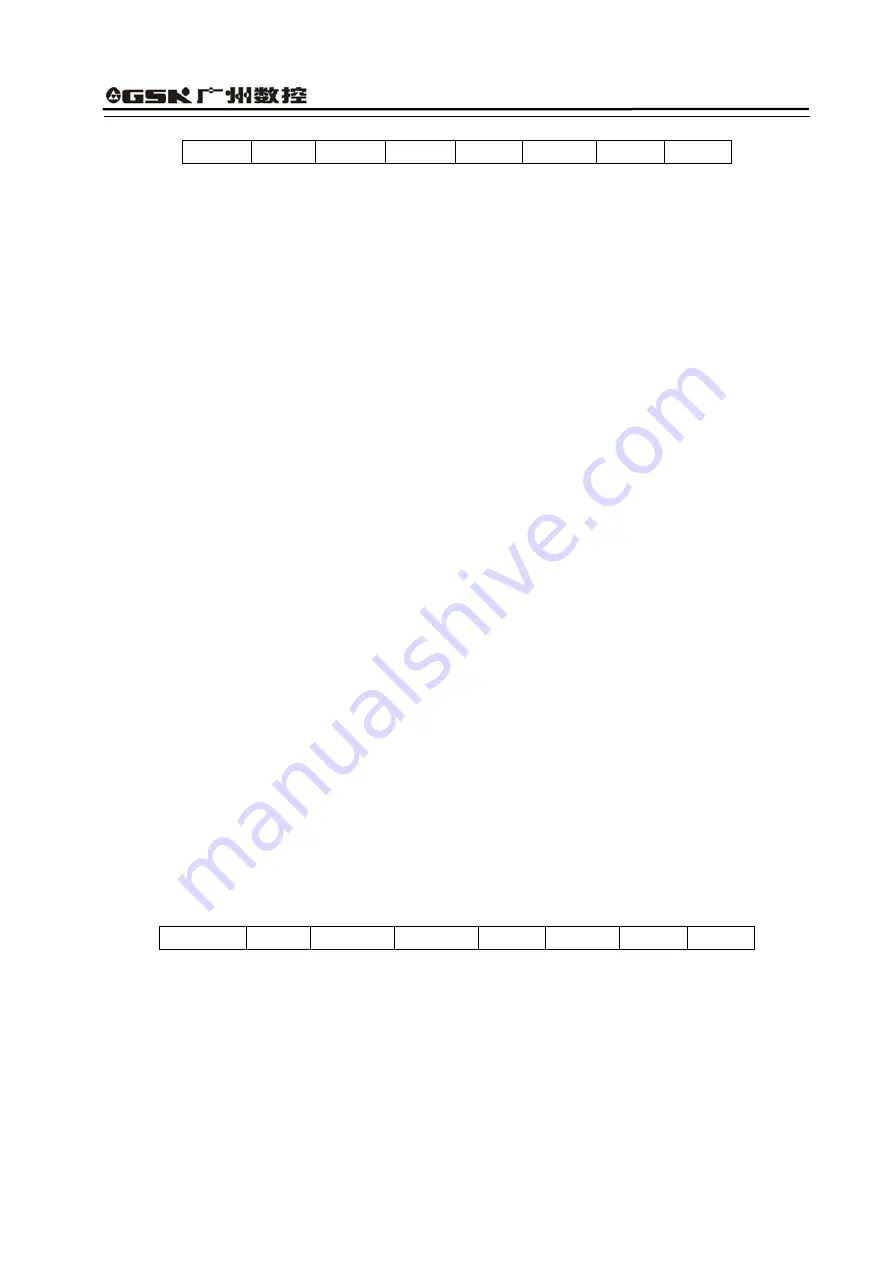
GSK928TE
Ⅱ
Turning CNC System User Manual
63
Bit 7
Bit 6
Bit 5
Bit 4
Bit 3
Bit 2
Bit 1
Bit 0
Bit 7 0 decelerating to zero is valid.
1 not decelerating to zero is valid.
The parameter decides that the connection method of two commands when the
system executes continuously the block in
AUTO
mode. If it is set to 1, after the
previous command ends and the run decelerates to zero, the next command is
executed. If it is set to 1, it is benefit for rapid transition of the tangent between arc
and arc, between arc and linear, which can avoid the trace on the workpiece.
Bit 6 0 run override of backlash is one.
1 run override of backlash is two times.
Bit 5 0 run override of backlash is four times.
1 run override of backlash is eight times.
Execution speed of backlash =lowest initial speed × (P25 Bit6) × (P25 Bit5).
P25d6/P25d5 can divide the multiple: 1, 2, 4, 8; the stepper motor should not
more than 1.
The stepper motor should not more than 1. the servo motor can be adjusted
according to the actual load.
Bit 4 0 the hydraulic chuck/tailstock control signal is LOW.
1 the hydraulic chuck/tailstock control signal is pulse. The pulse width is determined
by P15.
Bit 3 0 the hydraulic chuck control needs to check the clamp/release in-position signal.
1 the hydraulic chuck control does not check the clamp/release in-position signal.
Bit 2 0 the chuck clamp mode is outer.
1 the chuck clamp mode is inner.(clamp, release signal output is opposite to the
outer mode.)
Bit 1 0
the hydraulic chuck function is invalid.
1
the hydraulic chuck function is valid.
Bit 0 0
the hydraulic tailstock function is invalid.
1 the hydraulic tailstock function is valid.
4.6.1.22 P26—Bit Parameter 4
●
P26 Bit specifications
Unused Unused Unused
Unused
Bit 3
Bit 2
Bit 1
Bit 0
Bit 3 0 do not set the position again. The system automatically check whether the current
coordinates are same that of the defined by G50.
1 automatically set the position again. The system does not return to the initial point
of program, and directly modifies the current position into the ones defined by G50.
The parameter determines G50 mode in
AUT
O mode. P26 Bit3=1, the system
does not response the corresponding prompt, and directly modifies the current
coordinates into the ones defined by G50 to execute the next block.
Bit 2 0 limit alarm deceleration.
1 limit alarm emergency stop.
Содержание GSK928TE
Страница 1: ...GSK928TE II Turning Machine CNC System User Manual...
Страница 117: ...Programming Chapter Three Commands and Functions 112 G99 G01 X50 Z30 F0 2 G04 D2 G99 G01 X50 Z30 F0 2...
Страница 148: ...GSK928TE Turning CNC System User Manual 143 Connection Chapter One Interface 1 1 Interface Layout...
Страница 185: ...Connection Appendix 180 J3 1 AC220V J3 2 0V...